Crossdocking is a term that gets thrown about quite a bit in the distribution world. Let’s take a look.
In general, crossdocking refers to product that is received in one door and taken directly to staging/outbound doors (i.e., is not put away) without re-packing or other value-added services.
Supply Chain Digest Says... |
|
|
That seems simple enough, right? Well, not so fast. Turns out there are several different types of crossdocking.
“Planned cross docking,” for example, involves as the name suggests planning in advance to crossdock expected receipts. Often, this is based on receiving an advanced ship notice (ASN) from the supplier on exactly what has been shipped, whether, from an internal or external source.
This type of crossdocking is very popular in the retail world, based on vendor ASNs, and then pre-receipt store allocation. But some companies, even retailers, crossdock without ASNs, with goods allocated to stores after merchandise is received and exactly what was shipped from the vendor is known.
Planned cross docking can also be used based on PO information, but at the risk that what was shipped does not match what was ordered.
This planned crosddocking perhaps reaches it most advanced state when retailers send order information to vendors that includes both the distribution center the order should be sent to and also the final store destination. This is often executed through the “mark for” GS1 128 label: to this distribution center, marked for this store.
To add one more wrinkle, if there are back orders due to out-of-stocks, a company can perhaps plan to automatically move those SKUs to shipping upon receipt, or leave them in receiving staging if the WMS can allocate goods from that area. In either case, inbound receipts are used to fill back orders without putting them away.
Another form of planned crossdocks is when trucks with inbound goods from a central DC or plant are take to a crossdock faclily directly loaded on to smaller trucks for local distribution.
Finally, many 3PLs provide crossdock services when they receive generally full pallets from multple consumer goods companies and segregate and load the pallets across vendors for one shipment to retail DCs.
There are also what are called “opportunistic” crossdocks. Here, goods are received for which there are current orders, and some portion of the receipt is used to fill those orders to eliminate a putaway and pick.
This sounds good in theory, but is difficult to execute operationally. For example, such a move would likely violate FIFO/expiration date policies, and the timing can be tricky in terms of matching receipts with active orders, and likely the need to match picks from regular storage and combine them with crossdocked receipts to complete the full order.
But it can be done with the right WMS.
As a note for both types of cross docking discussed thus far, many retailers have a process advantage if they handle orders on a “door per store” model, where trailers are in effect fluid loaded for each store, eliminating many of the timing issues.
(See More Below)
|
CATEGORY SPONSOR: SOFTEON |
|
|
|
|
Another process that might be considered a form of opportunistic crossdocking is to take some or all of a receipt and move it directly to forward pick locations without going to reserve storage first, eliminating a replenishment task.
Again, there are some timing issues here, but this can work verry well for items that were out of stock prior to the receipt.
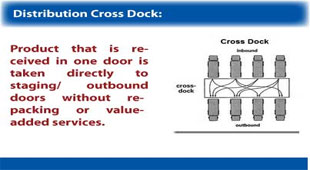
On a final note, is crossdocking, especially in retail, the same as what is called “flow through” processing?
Although we sometimes see the terms used interchangeably, they are different things. With crossdocking, a receipt is moved directly to shipping without any additional processing.
In flow through, some level of repacking or value-added services are involved between receipt and shipping. So, for example, full pallets are brought in, and operators break those pallets down and rebuild mixed-SKU pallets for outbound shipping. In retail, price ticketing or other services may need to be executed for the received goods, or cases of items broken to eaches for store distribution.
The key is that the products involved in flow through are never actually putaway for later picking before they are sent to shipping.
Crossdocking is much talked about and is broadly used in retail, but as we hope we have convinced you it can be challenging, especially from a timing perspective.
To do so effectively also generally requires an advanced WMS.
Do you have any thoughts on crossdocking? Let us know your thoughts at the Feedback button below (email) or in the Feedback section.
|