Like many Rust Belt cities, Dayton, OH - home of Supply Chain Digest - was once a manufacturing powerhouse, with many large factories, especially in the automotive sector (both OEM assembly and many parts suppliers).
But offshoring, the move of many manufacturers to the Sun Belt, the impact of the Great Recession and more walloped manufacturing in Dayton, as with many other cities in the Rust Belt and beyond.
Supply Chain Digest Says... |
|
|
But lately, consistent with signs of revitalization of US manufacturing generally, Dayton has seen manufacturing begin to return. There is just one (major) issue - most manufacturers cannot find anywhere near enough workers to meet demand.
A recent article in the Dayton Daily News by reporter Thomas Gnau nicely summarized the situation, starting with this anecdote: executives at Rack Processing Co., located in the Dayton suburb of Moraine, struck a deal last year nearly unheard of in the manufacturing sector.
Faced with the possibility of losing a customer because the company didn't have enough workers to fulfill an order, the company borrowed five employees from another local company for about six weeks.
"I think most of us are struggling [to find workers]," Jim Bowman, vice president and chief operating officer of Rack Processing, told the Dayton Daily News.
To secure the workers, Bowman had to promise not to hire them permanently.
"Companies like Rack Processing say they no longer have a shortage of jobs. They have a shortage of qualified workers," Gnau wrote.
The need is acutely felt and widespread, Gnau said. The Dayton area and West Central Ohio are home to about 2,500 manufacturers trying to fill some 3,400 new positions every year, according to Jon Foley, a trustee of the Dayton Region Manufacturers Association (DRMA), which has members in 14 counties.
From 2015 to 2025, the DRMA expects an average of 3,301 annual manufacturing openings in its service area, Gnau reports.
But Steve Staub, co-owner of nearby Staub Manufacturing Solutions, said area manufacturing openings are closer to 4,000 annually.
That during a period while the city of Dayton proper has been losing residents for many years, but the greater Dayton region itself still ranks at number 72 in terms of the US' largest metropolitan areas, with a population of some 800,000 people.
It's not enough.
Millennials Don't Want to Work in Factories
There are a variety of factors behind the near crisis for Dayton manufacturers, but one of them is basic and fundamental - younger workers simply do not want to work in factories the way their parents and grandparents did.
(Article Continued Below)
|
CATEGORY SPONSOR: SOFTEON |
|
|
|
|
Other factors include the growing in the level of technical skills required for manufacturing jobs - skills many potential workers do not have - as well as the growing number of baby boomers entering retirement and leaving the workforce, swelling the ranks of openings even when there isn't an organic increase in demand.
Then there are issues with regarding to personal behaviors of potential workers, such as just coming to work on time, staying at work - and being able to pass a drug test.
Scot McLemore, manager of talent acquisition and deployment for Honda North America, told Gnau that "It's the perfect storm that we're having" when it comes to finding production workers. Honda has several factories in the Central Ohio area.
The issue is certainly not isolated to Dayton even just in Ohio. In Northeast Ohio, including Cleveland, there was recently demand for 5,538 skilled production workers - a category that includes repair technicians and workers with advanced manufacturing skills - but only 3,112 relevant training credentials obtained by workers in the region.
Of course, the problem is national in scope. There are growing reports of worker shortages in many areas of the country. As SCDigest recently reported, the number of US manufacturing job openings in March rose to 394,000, the Department of Labor recently said, matching the highest level since April of 2006. (See Is US Manufacturing Glass Half Full or Half Empty?)
US Manufacturing Job Openings Continue to Grow
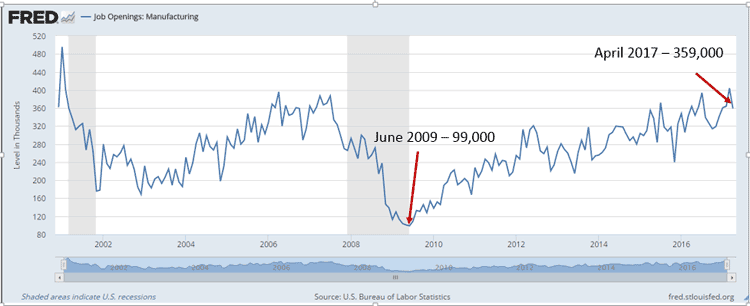
In January, consulting firm Deloitte estimated that there will be a shortage of two million manufacturing workers in the US within the next decade.
In Dayton specifically, and perhaps many other regions, large manufacturers, while struggling to find workers too, have the budgets and name recognition to attract the preponderance of available workers.
Really hit hard are smaller manufacturers without name recognition.
Most manufacturers are small, family-owned businesses with 50 or fewer employees, where the retirement or other loss of even a few workers can have a big impact on output levels.
What to do? There is general agreement that manufacturers need to do more to promote manufacturing as an attractive career path. There are also calls for manufacturing and education, such as at the community college and even high school level, to develop programs together that better prepare workers for the growing number of manufacturing jobs that are available.
"High school, college-age - it needs to start younger than that," Brian Ault of Bruns General Contracting in Dayton, told Gnau. "I think it needs to start at the elementary level. We need to at least talk about manufacturing at that age."
Honda, for example, has training partnerships with six Ohio community colleges and three Central Ohio high schools.
But in the end, there are no easy answers, though many may turn to robots to fill the void - and quickly.
What do you think of Dayton manufacturers' struggle to find workers? Are you seeing that same thing where you are? What is the answer, if any? tLet us know your thoughts at the Feedback section below.
Your Comments/Feedback
|
Steve White
Career Connections Coordinator, Spectrum Career, LLC / Job Search That Works |
Posted on: Jun, 07 2017 |
|
I live in the Dayton area. I see two sides to this situation.
One. Yes indeed! I read about and hear from leaders in manufacturing in the Dayton area about how much of a struggle it is to find enough people with the skills necessary to fill so many skilled trade jobs. There are over 500,000 skilled labor jobs available in Ohio with thousands of them in the Miami Valley area. I really think the challenge is much greater than not being able to find the people who have a good work ethic, pass a drug test, or don't show any interest.
There is so much emphasis on talking about the manufacturing job openings in advertisements, articles, social networks and job boards that only around 5% of potential people who could fill those positions are even paying attention and responding. I really believe the other 95% are being ignored because they are not being emotionally compelled to respond. Companies and colleges market too much about themselves and completely ignore the real issues facing the potential workforce (that is all around us).
This leads me to the second side of this whole thing...
Two. Even if we don't count the people who can't pass a drug test, there are plenty of people who love to work with there hands and will be very interested in working for some of our local manufacturers. They just don't know they would be interested because no one has really talked to them about "them" and helped them with the missing step (in most job readiness programs) which takes them into a deep conversation to do some "self exploration".
Most people are not aware of what they can do and what skills they have or could acquire. There are not aware of what their purpose is and cannot figure out what their "life's work" or true career path is in which they will have many different jobs.
When more time is spent on helping the workforce determine what they have liked/disliked at their previous jobs; what there are good at AND what they aren't so good at in their previous jobs; identify their transferrable skills are as well as their soft skills. This conversation will draw out so much information about what they are "thinking & feeling" about their interests and abilities that they will be more open to looking at other opportunities (jobs) they never thought they would actually consider. There MUST be a conversation from where they are sitting and what their challenges are; NOT from the manufacturer's position. (this is sales 101)
MAKE A BIG DEAL ABOUT THEM!!!
Once they have gone through this self-exploration step, they will be more confident about themselves and feel a sense of hope about their financial future and career path.
Then, and only then, will they begin to make connections to opportunities (job openings) that are in alignment with WHO THEY ARE. Once they get a sense of confidence that "just maybe" they could be interested in these skilled labor positions at manufacturing companies (or what ever is in alignment with who they are), then they will be more comfortable with what it takes to acquire the skills necessary. That can be determined by Career coaches at employers, community colleges, or at workshops like the one's we are conducting with Sinclair College.
They will be open to investing in training to acquire these needed skills like the 16-week Accelerate Manufacturing Certificate Program at Sinclair College. Before they even complete the training, they will receive an offer at one of our local manufacturers.
We would love to have a deeper conversation about how we can help build more interest about these type of jobs as well as what are some of the missing steps to help prepare a local workforce for the future.
Thank you.
Steve White
(937) 701-7303 x504
www.JobSearchThatWorks.com/jstw-careers/events-calendar/
|
|
Bob McIntyre
National Account Executive, DBK Concepts |
Posted on: Jun, 14 2017 |
|
I've done business in Ohio, and the Dayton region since 1979. All of the manfacturers here have been my customers. (Even many years ago, Rack Processing). You've been in the area long enough to know that the High Schools here push college over any sort of technical training. That's part of the problem. Dayton used to be a big tool and die manufacturing city. In the day, those were well paying jobs.
Having sold safety equipment during Dayton's manufacturing heyday, I saw ther old guys with the secure union jobs take advantage of the great pay, and job security. Moving from safety equipment (worn, and used, by people) to the barcode and automation industry, was necessitated by the decline in the labor workforce numbers.
Two things happened. First - Union contracts were renegotiated, where potential employees no longer viewed manufacturing as a job that paid enough to be considered a long-term career. Second - Companies no longer hired permanent staffs, but rather relied upon staffing companies for their employees.
I was very involved with all of the manufacturers. I trained manufacturing people on barcode technology, as I watched the workforce I had formerly supplied with safety equipment decline. For several years, one local customer who also had a Fort Wayne plant, constantly asked if I knew which plant was closing. Another, where I dealt closely with both management, and their highly skilled workers (Everyone would know their name), moved their production to a less expensive (But, not nearly as productive) non-union out-of-state plant.
As far as the workforce goes, I saw the days when the unions had the power to make the GM plants pay workers who sat in break rooms because they were too drunk to work, and it was too hard to fire them. These days, the pay is far lower, the workforce is totally unmotivated, and they do not view these jobs as 'careers'. (I'm a part owner of a retail company, and we have the same employee issues).
One of the big manufacturers in the area, who is working six day weeks, used to actually hire employees directly. Now they use a staffing company. Employees sense of commitment to the company is gone.
Several years ago, Jon Boehner was interviewed on local TV at one of my customers who had just cut their manufacturing staff of 400 down to 100. The only reason the 100 were still working was to correct flaws in the production from the overseas plant, and fill critical emergency orders whan overseas production delays occured.
For companies to attract a stable and well trained workforce, they're going to have to convince the willing and motivated employees that it's the correct career path to pursue.
Steve White had some good ideas for any manufacturing centered geographic area in his post on this subject.
I can be reached at 937-815-7146.
|
|
|