In case you haven't noticed, something like 9 out of 10 articles on supply chain in recent days have something to do with the impact of the dreaded coronavirus crisis.
OK, I may be exaggerating a bit, but it sure seems that's about the ratio. I've read quite a few. Most were bland and boring.
Gilmore Says.... |
 |
Among the eye openers from this crisis is the news that the Western pharmaceutical industry is hugely dependent on finished products and ingredients from Chinese factories.
|
 |
What do you say? |
|
Click here to send us your comments |
|
|
|
|
So the supply chain industry needs yet another coronavirus article like the proverbial hole in the head, but I couldn't resist the opportunity to see if I could find anything interesting to add to the discussion.
Let's start with this.
Supply chain risk management rose in prominence let's say about 20 years ago. Then, we started to see some basic models for deciding what risks to mitigate, as shown in the graphic below. Those basic models - still in widespread use - have two dimensions, the likelihood of a given event, and the corresponding financial impact.
Naturally enough, those models drive companies to focus on risks that are high probability and likely to have a big impact. Low likelihood, low impact events can mostly be ignored. What to do with those risks in the middle create the tough questions.
So where would a global virus breakout fall on the basic model framework? Probably nowhere. It is what Dr. David Simchi-Levi of MIT calls one of the "unknown unknowns" – and it is not clear what to do with those risks in the existing frameworks (though Simchi-Levi came up with a very smart approach we covered several years ago that I don't have room to cover in this column).
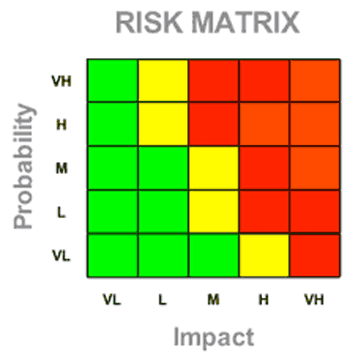
Another observation is that while risk management has become a core supply chain discipline, the emphasis tends to wane and wax depending on events. Until this current crisis – if it really is a full blown crisis – the last major supply chain risk management inflection point came with nuclear reactor disaster in Fukushima, Japan in March of 2011.
That event – another unknown unknown – caused hundreds of Japanese factories to close for weeks, putting a big hit on output from companies across the globe, many of which had no idea their supply chains were dependent on tier 2 or tier 3 suppliers they didn't even know existed.
It also generated one of my all-time favorite supply chain quotes from mighty Toyota's head procurement, who said, paraphrasing from memory just a bit, "We thought we had complete control of our supply chain. It was an illusion."
I am going to come back to the key point here at the end of the column.
What is interesting to me is just how quickly the coronavirus impact is felt even in areas well outside the few hot zones. For example, Maersk Line, the largest ocean container carrier, has canceled more than 50 sailings from China to the rest of the world since late January. That represents hundreds of thousands of containers full of goods and components that will be significantly delayed getting retail shelves or factory floors.
Airlines are now massively cancelling flights into and out of China. The same thing is happening now for flights to/from Italy, where a modest virus outbreak has occurred.
It won't take a whole lot more for global commerce to basically shut down – and what happens then? Economic chaos at minimum, that's for sure.
Among the eye openers from this crisis is the news that the Western pharmaceutical industry is hugely dependent on finished products and ingredients from Chinese factories. If that supply chain is cut off for any extended period, you may soon not be able to go down to CVS to pick up your prescriptions because the drugs just won't be there.
The Wall Street Journal last week wrote an interesting article noting how much the supply chain world has changed since 2003, when there was another but relatively contained coronavirus outbreak in China. Keep in mind China only joined the World Trade Organization, which dramatically expanded its market reach, at the end of 2001.
In 2000, China's share of global trade was 1.2%. It was 34% in 2018. Interestingly, the rise has been much less in US trade, where China's share has grown from 2.1% in 2000 to a much smaller 7.2% in 2018, but that still more than tripled over the period.
So when China's supply chain get a cold – in this case unfortunately in a sort of literal sense - the rest of the world might get pneumonia.
The Journal piece includes the story of Mostafiz Uddin, who owns a bluejeans manufacturer in southeastern Bangladeshi. He said he has been unable to fulfill an order for 100,000 women's jeans because he can't get the fabric he needs from China.
"I am just waiting," he said. "We have no option."
Or consider Australia, still heavily dependent on exports of coal, iron ore, wheat and other commodities to fuel its strong economy. China accounted for nearly 40% of Australia's exports in 2019. Coronavirus is a huge risk to its economy even if it doesn't get a single case.
This with, if I may daresay, at least for now what is a relatively small level of cases outside the worst areas of Wunan city in China. If this thing really does become something like a pandemic, the costs will monumental.
Dr. Yossi Sheffi, also of MIT has written a couple of excellent books on supply chain risk management (e.g., "The Resilient Enterprise"), so he comes with some credentials in terms of offering thoughts on the current coronavirus crisis.
Writing recently in the Wall Street Journal, Sheffi offers five actions companies should consider right now:
1. Set up a central emergency management center: At this point it can be virtual but should include a clear roster of participants with clear decision-making rules in case of a pandemic.
2. Review the company's product portfolio and the customer base in order to set priorities: If capacity is reduced, there will need to be rules for which products should be built and which customers should be supplied first.
3. Review suppliers: Who makes critical parts? Are there alternate sources? What is the suppliers' inventory status?
4. Plan for operating to maximize cash flow rather than profits.
5. Maintain communications with federal and local authorities, as well as Chinese and other Southeast Asian friends and colleagues on the ground.
I am going to focus on number 3, relative to the point I said I would come back to regarding Toyota – and that is the need to map your supply chain at multiple tiers, an exercise Toyota undertook with vigor after Fukushima – but never could fully complete.
But such an exercise will prove very valuable in the event of the next unknown unknown in terms of rapid understanding of potential disruptions. That mapping can also uncover risks a company didn't know it had - for example, as many companies found in 2011, that in some cases dual sourcing to reduce risk was for naught because both of the two suppliers were dependent on the same single source for a part or other input.
So what's the takeaway from all that? I would say that most of our risk models are still not sufficient for the job – and too much reliance on China is a very risky proposition indeed.
What are your thoughts on coronavirus and supply chain? Let us know your thought at the Feedback section below.
Your Comments/Feedback
|