OK, I admit this has been"Gartner month" here in this column, with my review of the keynote presentations at the Gartner Supply Chain Executive Conference in Scottsdale, AZ two weeks ago, followed last week by Understanding the 2017 Gartner Top 25 Supply Chain Rankings, after that annual list was announced as usual at the Executive Conference.
So this week I return with an Executive Conference trip report part 2, and add for the first time a new conference review system hat rates this and I hope future events that I attend across key attributes, from content to food, just for fun and maybe to stir up some discussion. See that later in this column.
Gilmore Says.... |
 |
J&J is "over-investing" at the start of this effort in high-priced talent in operations research and data science, because it wants to ensure initial success that will fuel expansion of the program. |
 |
What do you say? |
|
Click here to send us your comments |
|
|
|
|
After having looked at the keynote presentations in part 1, this week I will summarize several breakout sessions, again with the note that it is important to understand the structure of these presentations.
Some breakouts feature only a single or pair of Gartner analysts. In a few sessions, a Gartner analyst press jointly with a supply chain practitioner from usually a large company, with the Garner analyst generally starting with some overall observations/research on a given topic, followed by a case study from the practitioner.
Then there are sponsored sessions, which sort of look like regular breakout sessions on the agenda (though are reasonably well marked as such), but are in fact bought and paid for by software/consulting vendors for large amounts of money. A given 45-minute breakout time slot will be given to all sponsored sessions, with generally five alternatives.
Sometimes I attend one of these, and sometimes I don't, while I viewed a non-sponsored breakout in every available time slot while I was there.
With that introduction, on Tuesday I attended a good presentation on inventory management by Gartner’s Paul Lord, the net off which that the standard accounting system views of inventory - percent of sales, inventory turns, etc.- are really not adequate to drive the right inventory performance.
So as others have also noted, part of thinking about this differently starts with understanding the purpose of inventory - why do we have cycle stock, safety stock, anticipatory inventory, etc. - and how and when does inventory truly add value, not just soak up working capital.
Believe it or not, this is something many supply chain professionals- let alone company or commercial managers and executives - don't understand, and is really the place to start to get more enlightened in terms of inventory management practices.
Lord believes we have a decent understanding of what he called "structural inventory" - inventory sort of inevitable based on the network design, the number of SKUs, etc., and also for "operational inventory," which has to do with the day to day jobs of ordering, scheduling, replenishing, etc. and how they impact inventories.
But there is a third category Lord calls "situational inventory," which is inventory based on things like seasonality, events and promotions, new product introductions, volume buying opportunities. and more. Here, he says, the ability to apply business rules and traditonal supply chain math are more limited - and we need more work to get this type of inventory right.
This is sort of research in progress for Lord, but it looks promising, though I will observe the smart guys at some of the inventory optimization vendors can talk very insightfully about much of this.
Also on Monday, Gartner’s Noha Tohamy and Filip de Keersmaeker of Johnson & Johnson gave a solid presentation on use of modeling techniques in the supply chain. Tohamy began with a sort of "modeling 101" overview, noting that many different types of approaches are used to leverage models (heuristics, statistical, optimization, etc.).
Certain techniques lend themselves to different supply chain problems, such as heuristics for demand-supply matching in S&OP, and optimization in network design. It is good to have some basic understanding of this, Tohamy said.
de Keersmaeker began by noting the tremendous challenges in optimizing the full supply chain, given all the interconnected trade-offs across many areas, and the huge amount of data that must be acquired and leveraged.
The focus at J&J was "end-to-end" and the implication it seemed to me was that J&J was running one giant galactic "solve" to optimize the entire supply chain. That it turns out is not the case, as separate optimizations are run for things like network design, what plants and lines should make what products, etc. But J&J is doing this in an iterative fashion that remains aware of the impact on other areas - a step forward.
There was a long search for a tool provider, and J&J selected LLamasoft, and the company is indeed using different approaches to different problems, such as mixed integer optimization for network design, standard linear programming optimization for other areas, etc. de Keersmaeker said the focus is on "high impact, low frequency" decisions, meaning not day to day or week to week decision processes, but rather those run monthly, and especially quarterly, semi-annually, and annually.
A couple of interesting points. J&J is "over-investing" at the start of this effort in high-priced talent in operations research and data science, because it wants to ensure initial success that will fuel expansion of the program based on clear results. It plans to build a more balanced team in terms of experience/education down the road, including a role I had not heard of called "citizen data scientist" - non-formally trained supply chain practitioners who get very good at this.
Second, in a recent "run" of optimization across several of these process areas, a full 40% of J&J SKUs were affected - meaning safety stock, sourcing, manufacturing "cadence" or other decisions were changed versus before the new modelling process - and the model considered some 4 million variables. Try managing that in a spreadsheet.
The last breakout session I attended (I have skipped a couple of other just OK breakouts I do not have room for here) was one of the sponsored presentations from consulting form Accenture late Wednesday morning, on what Accenture calls "supply chain X.0." The claim is companies need to pivot to new models for things like organizational structure - less hierarchical and functionally siloed - along with greater use of supply chain segmentation, digitization, and other newer age techniques
It sounded interesting, and I think Accenture would have been better served by going through all this in detail. Instead, it was covered really at just very high level in only a few minutes, with most of the session then allotted to supply chain execs from Estee Lauder, Merck and HP, all of whom were OK, but oddly none of them really connected to this notion of supply chain X.0.
Most interesting of the three was the Merck executive, whose name I did not catch - they flashed the slide for like 5 seconds and his was the one name I didn’t get - who said the company was implementing a new planning system (Kinaxis).
The issue was this: the goal and the technology were meant to drive more end-to-end supply chain thinking. But Merck’s planners have operated for years in a more transactional, node-to-node way, not end-to-end.
So Merck actually put the project on hold, and is going back to retrain all these planners in the new way before restarting.
I will note that In part 1 of this review I summarized the observation from Gartner keynote speaker general Vince Boles that the reason the US M1 Tank wins in battle is not because of far superior technology but rather great technology combined with far superior operator training. Well with the Merck story you have that concept well echoed in a supply chain context.
Finally, as promised, below is my event evauation template for this year's Garner conference. If you were there, how do my scores stack up with your experience?
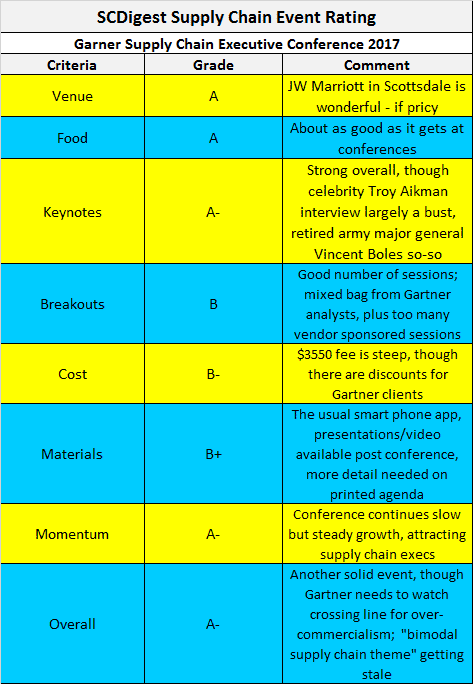
All told, a solid event again at Gartner this year.
What is your reaction to Gilmore's Gartner trip report - and new conference review system? Let us know your thoughts at the Feedback button below.
Your Comments/Feedback
|