A couple of months ago, I wrote a column about supply chain flexibility, focused around the fact that most everyone seemed to agree that SCM flexibility was important, but how to define it and measure it was not clear at all. (See What is Supply Chain Flexibility?)
In that column, I noted my belief that supply chain flexibility needed to be thought of as compromising at least two levels:
- “Micro-flexibility,” which has to do with how rapidly a supply chain can effectively respond in near real-time when something goes wrong or an opportunity arises (e.g., the truck is late, an unexpected order comes in, the machine in one factory goes down, etc.).
- “Macro-flexibility,” which has to do with how fast and efficiently a company’s supply chain can respond to broader strategy changes or customer needs (e.g., developing a new distribution channel, finding new sourcing points, changing postponement strategies, etc.).
My view linked nicely with the classic Harvard Business Review article “The Triple A Supply Chain” by Stanford’s Dr. Hau Lee, in which he described “Agility” (close to my micro-flexibility) and “Adaptability” (close to my macro-flexibility) as two of the three A’s (the other was Alignment).
Gilmore Says:
|
|
"Dr. Simchi-Levi says that he defines supply chain flexibility as the ability to respond to change without increasing operational and supply chain costs and with little or no delay in response time."
What do you say? |
|
Send us
your Feedback here |
|
But we still didn’t have much of an answer to a real definition – and certainly not close to how supply chain flexibility might actually be measured.
So I decided to reach out to some supply chain friends and colleagues whom I thought might be able to add some clarity here. My questions: What is SCM flexibility, and can it be measured?
I started with Dr. Lee, whom I know modestly well. He offered a succinct response:
“Flexibility should be measured with a time-element in it,” Dr. Lee told me. “Hence, the flexibility to change volumes and mix must be time-based. Flexibility one month out versus flexibility three months out are very different. We should look at the whole time profile of flexibility in evaluating an operation - what is the flexibility over different time frames?”
That clearly is part of the essence – most everyone can do anything eventually. So yes, time is a critical dimension. But we need more.
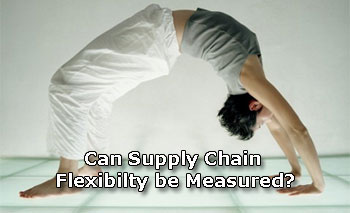
Our friend Tom Dadmun, once Supply Chain VP at network gear maker Adtran and now somewhere higher in the org chart, had this to add to the subject:
“To me supply chain flexibility is about responsiveness to the customer. We can all debate whether we should call the process “Demand Chain” or “Value Chain,” but the key here is to have the Supply Chain respond to the customer’s demand,” Dadmun said.
“To be truly flexible is to have a responsive process at every link in the chain that will quickly respond to the new input signal,” Dadmun added. “Who’s in this control tower overseeing the entire value chain, even beyond the 4 walls of the enterprise? The Chief Supply Chain Officer of course. And his or her measuring stick of success is a hierarchical list of KPIs, with alerts triggered by real time events identified by control limits on the BI Dashboard. ‘Beam me up Scotty.’”
Bob Nardone is a former VP of supply chain planning at Unilever/Best Foods and now running his own consulting firm (Supply Chain Guidance). He notes that “Defining Supply Chain flexibility concisely is a challenge and one that probably has different nuances for different businesses.”
That said, he believes that “supply chain flexibility is the ability to quickly respond to changes in demand while achieving your customer service, cost, inventory and return on assets (ROA) objectives.”
That’s an important nuance – can you respond rapidly without breaking the bank?
He adds that “I don’t think flexibility can be determined by one measurement but rather by a composite of metrics that many businesses currently measure,” and that “A business should only invest in the level of supply chain flexibility (supply and distribution networks, systems, and people) needed to be competitive and grow.”
As I mentioned in the first piece, my friend Dr. David Simchi-Levi of MIT has done some great work lately that looks very specifically at supply chain flexibility. As I said then, he offers a specific definition of what supply chain flexibility means for manufacturers. If you have 5 manufacturing plants for a given business and each one can only produce one family of products, you have 1X flexibility. If each can make two families, you have 2X, etc. “Full flexibility,” or 5X in this example, would mean every plant can make every product.
The question then becomes what are the costs and benefits of achieving these different levels of flexibility? Those trade-offs can be specifically measured, he says.
In subsequent comments to me, Dr. Simchi-Levi noted the connection of supply chain flexibility to the growing importance of supply chain risk management.
“Little can be done after a disaster has occurred,” Dr. Simchi-Levi says. “Companies therefore need to plan their supply chains so that they can better respond to both mega-disasters and mundane operational problems.”
He added that “flexibility into manufacturing, supply chain, and network strategies is essential if companies are to respond effectively to on-going change. Of course, the question is how to achieve flexibility and how much of it is required since flexibility does not come free.”
And I like this. Dr. Simchi-Levi says that he defines supply chain flexibility as “the ability to respond to change without increasing operational and supply chain costs and with little or no delay in response time.”
In this definition, he says, “change refers to change in demand volume and mix, commodity prices, labor costs, exchange rates, technology, equipment availability, market conditions, the production and logistics environment or any supply disruption.”
Now we are getting closer.
My colleague Gene Tyndall of Tompkins Associates added some interesting additional comments on this topic.
Tyndall observes that “Supply chain managers to be cautious about flexibility. While customers may want it, financial, security, and risk controls may limit the ability to achieve it.”
He adds that “Flexibility usually comes with an added cost, and this must be weighed against the value proposition for it. Supply chain managers strive for predictability and consistency, mostly for cost control reasons. When flexibility is introduced, so often are uncertainly and exceptions.”
Interesting and valuable comments from all our experts, and thanks to each for the time spent to give this subject some thought.
Yet, my sense remains that for all the emphasis on supply chain flexibility and agility these days, we have nothing even resembling a standard definition or set of metrics to use to track where a company stands or what progress it is making (though Dr. Simchi-Levi is getting close).
Isn’t it about time we had some better clarity here?
So we are going to do some more work on this at SCDigest – and if you are interested in participating in the effort, or have some specific ideas, I would love to hear from you.
The full comments from our experts will be published next week in Supply Chain Digest On-Target – be sure to take a look.
You will also find a link to our Cartoon Caption Contest winner for the first half of 2010 nearby - see who took home the $50 prize!
Can you offer a way to define or measure SCM flexibility? Would you be interested in an effort to make progress on these issues? Let us know your thoughts at the Feedback button below.
Web Page/Printable Version of Column
|