The following column comes through special arrangement with the Lean Enterprise Institute. It is an article written by Lean expert Art Byrne, CEO of The Wiremold Company, and author of The Lean Turnaround and The Lean Turnaround Action Guide.
If you’re like more than 90% of the traditional managers and engineers I’ve met, you likely consider setup times as just some minor manufacturing thing and believe “there’s nothing we can do about it.” So, you run large batches at a higher speed to lower unit costs — and ignore setup times, which you never considered when ordering the machines. You also trust your highly skilled operators who insist there is no way to reduce the setup times and argue that running large batches at high speed already gives you the lowest “cents each” costs.
While these beliefs persist, Eiji Toyoda and Taiichi Ohno demonstrated the error of that thinking generations ago when they introduced the Toyota Production System after World War II. Discounting the value of setup time reduction was the prevailing attitude then, and lowering setup reduction emerged as a key hurdle to overcome when developing their just-in-time approach to meet customers’ needs.
Supply Chain Digest Says... |
|
|
With the help of an outside consultant named Shigeo Shingo, Toyota made huge progress. Shingo, who proved to be one of their most important collaborators, developed the concept of Single Minute Exchange of Dies (SMED). (To clarify a common misunderstanding, SMED didn’t require one-minute setup times but setup times of less than 10 minutes, i.e., in the single digits of time). Shingo perfected this approach and wrote definitive books on the subject. (See his A Revolution in Manufacturing: The SMED System.) And without SMED, Toyoda and Ohno would never have succeeded in creating the Toyota Production System.
Understanding the Strategic Benefits of Setup Reduction
What’s surprising is that anyone would even ask why setup reduction is essential. It should be obvious. For starters, a one-minute setup is much more efficient than a one-hour setup, if nothing more than you free up 59 minutes of capacity. In addition, you can make smaller batches more cost-effectively by saving money in moving, storing, and possibly writing off obsolete parts. A company with faster setup times can also respond quickly to the customers’ needs and cut lead time from weeks to days.
Also, you cannot transition from traditional batch manufacturing to lean without paring long setup times — which is why people batch in the first place. Becoming lean will force you to reduce your setups early on. Lean is about “sell one-make one,” which requires a one-piece flow production process. As soon as you try to sell one-make one, you will discover that you can’t do it with two- to four-hour setup times. You must reduce those first, or there is no flow. No flow equals no lean.
Above all, you should recognize that the strategic implications of setup reduction are enormous. Doing so is not just “some manufacturing thing.” Notably, long setup times create long lead times (say six to eight weeks) and excess inventory due to the big batch sizes, which in turn require 40% to 50% too much space with all the associated costs. In contrast, quick setups drive one- to two-day lead times, minimum inventory, 50% less space, and much lower costs. That sounds strategic to me.
(Article Continues Below)
|
CATEGORY SPONSOR: SOFTEON |
|
|
|
|
Getting Started with Reducing Setup Times
Over the years, I have been involved with and led many setup reduction efforts, and without claiming to be Shingo, I can share some of the things I have seen and learned.
Let’s start with one of the most important things that Shingo taught us:
Start your setup reduction efforts by separating those tasks that can be done external to the setup from those that can only be done internally when the machine is turned off. While this may sound simple, doing so will almost always cut your setup time by 50% or more without any financial investment. That is because the traditional approach to setup starts with turning the machine off, which makes everything internal to the setup.
If you spend the time while the machine is running getting everything ready for the next setup, you will drastically reduce the time that the machine is off, reducing setup time. Do this before you try your first setup reduction, and you will already have a 50% reduction.
Next, observe and film the setup itself. Create a spaghetti chart showing each of the operators’ movements. Prepare for a shock when you see each step — and the huge opportunities to eliminate waste. This exercise is a bit like creating a value-stream map, which may sound elementary to you, but most traditional companies simply accept their setup times as they are. If you ask management how often they watch a full two- or three-hour setup, the answer will almost always be never.
You will get significant gains from these first few steps and should now consider additional ones such as:
* Get rid of cranes and forklifts for setup.
* Reduce or eliminate the number of wrenches and tools needed.
* Eliminate bolts where you can and standardize on one size.
* Create guides to move the new tools into place in one shot.
* Place any tools you need at the point of use.
* Store the needed dies or molds near the point of use.
Also, when you begin to focus on setup reduction, a good kaizen mix would be two setup reductions, one flow kaizen, and one office kaizen for every four you do.
Taking the First Steps Toward Setup Reduction
Let me share some steps we took at Wiremold with our punch press dies and injection molds.
One of the first things we did was tackle a common challenge by establishing that a punch press die could never be out of service for repair. To implement this new rule, we created a set of spare parts for every die that could quickly replace broken parts (high-volume dies first). Then we established a satellite tool room next to the production floor so that we could open, inspect, oil, and, if needed, repair every die immediately after every use. Then we created a standard height for every die: one for progressive dies and one for our secondary tools. We had 1,600 dies to alter, so this took some time.
Once some of these basics were underway, we focused on how to move the dies in and out of the presses during setup without using a crane or a forklift. First, we created V-shaped roller tables next to every press so that an operator could quickly and easily pull out the old die and push in the new one.
Next, we put a backstop on each press with a V-shaped extrusion and a matching V-shaped indenture on the bottom plate of each die. These changes allowed the operator to position the die perfectly by pushing it into the press. Finally, we worked on holding the die in place with the minimum number of tools and bolts.
Breaking the Mold of Old Practices
When we started to make these changes, we were doing changeovers from overhead using a crane. But, because we only had a couple of cranes, people and machines had to wait far too long. So, the first thing we did was to side-load the molds, which required mold alterations and adding roller rails, so we could easily slide the molds into the machine.
Next, we had to build two carts for each machine and mount them on rails next to the machine: one to receive the mold coming out and one to hold the mold for the next setup. This arrangement had the added benefit of enabling us to, when needed, preheat the new mold while it was in the waiting position.
Then we moved all the connections, like cooling lines, to one side of the mold so the operator could do the changeover from one position. We also consolidated multiple hookups on each side of the mold into one easy snap-in device. Then we added hydraulic clamping to secure the mold in place with the touch of a button. We then built storage racks at the end of each molding machine and dedicated molds to specific machines, even though the molds were compatible with many machines.
Tallying the Results of Setup Reduction
Below is a sample of results from setup reduction efforts I have participated in on many different types of machines. Also, at Wiremold, we found that a one-week kaizen event on almost any equipment would yield an average reduction of nearly 90% in setup time.
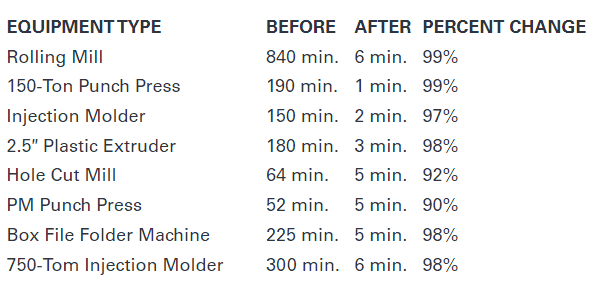
Many of these examples took more than one kaizen to accomplish. For example, our initial punch press and injection mold kaizens reduced the time to about 30 minutes, but we did not stop there. Several more kaizens got us to the one- to-two-minute range, where we stayed. Note that this work was never capital intensive — it was the reverse, as we freed up money by reducing the need for inventory and floor space. Just as important, it built a sense of accomplishment and teamwork among our workforce, which was priceless.
So, for zero (or tiny) capital spending, we brought our lead times from four to six days weeks to one to two days, lowered our costs, and gained a lot of market share. Setup reduction is a must if you want to become lean. It is a strategic weapon, not just “some manufacturing thing.”
What are your thoughts on Lean Setup Time Reduction? Let us know your thoughts at the Feedback section below.
Your Comments/Feedback
|