Industry 4.0 - a term referring to the digitization of business processes, offers a huge opportunity for manufacturers, say the consultants at McKinsey.
Supply Chain Digest Says... |
 |
Of course, in today's dynamic world, any training has a short shelf-life, and new challenges will continue to arise. |
 |
What do you say? |
Click here to send us your comments |
 |
Click here to see reader feedback |
|
|
How huge?
McKinsey says digital technologies could boost the value generated by industrial companies by as much as 22%, adding $2 trillion to the global economy.
But to capture some of that, manufacturers may need to train much of the workforce - or what McKinsey refers to as "technical reskilling."
But too often, McKinsey says, companies rush to some training, any training, under the perceived pressure to get more digital right now, without analyzing what skills are really needed to drive value.
That includes answering such basic questions as what specific skills the organization requires to succeed in its digital ambitions, and determining which individuals need those skills and by when.
Failing to ask and answer those two most basic questions likely will result in companies investing time and effort to develop the wrong combination of capabilities. Also, such companies may lose the confidence of employees, with potential learners unwilling to engage because they don't see the relevance of the skills they are being asked to develop.
McKinsey suggests one approach to avoid these risk areas. That involves a tool called a learning needs analysis (LNA). An LNA, McKinsey says, is the critical step that links capability building efforts to the desired business outcomes.
The basic idea is simple: First define the business problem. Next identify the proposed solution. Then determine the skills required to deliver that solution and compare those requirements with the organization's current capabilities. Finally take the necessary steps to fill the gaps.
To illustrate the potential of LNA, McKinsey cites the example of Tata Steel in Ijmuiden, Netherlands. The company had begun to make great progress with advanced analytics, but also came to an important realization from those early efforts: results would come not from a handful of high-impact applications, but from hundreds of smaller projects scattered across its operations.
(Article Continued Below)
|
CATEGORY SPONSOR: SOFTEON |
|
|
|
|
For that to happen, however, would require a large number of people in new roles, including data scientists, data engineers and "digital translators" who could define problems and help to transform analytical insights into actionable changes to manufacturing operations.
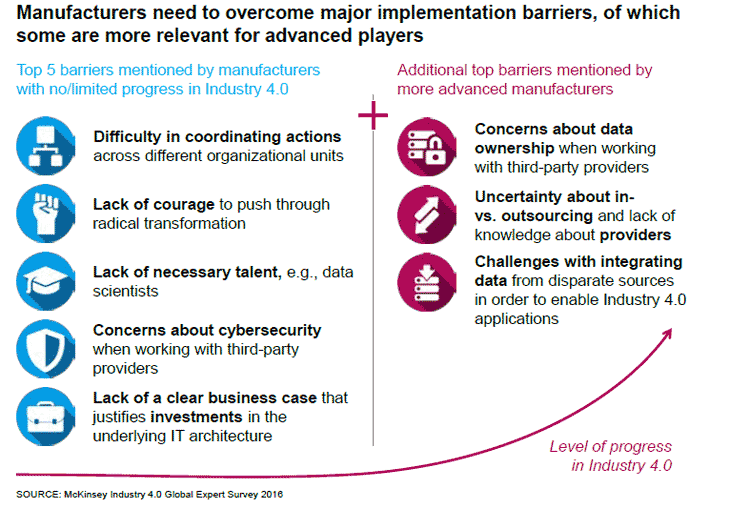
To meet those needs, Tata developed an internal Advanced Analytics Academy, which provides tailored training using real data and context-specific examples from the company's operations. More than 200 employees have already been through the training program.
Of course, in today's dynamic world, any training has a short shelf-life, and new challenges will continue to arise.
"While they can't predict the specific capabilities they will need to address every future requirement, organizations can work to create the right underlying mindsets, encouraging their people to take ownership of their own development, pursuing personal growth in a culture of life-long learning," McKinsey concludes.
Is training key to realizing the benefits of Industry 4.0? Let us know your thoughts at the Feedback section below.
Your Comments/Feedback
|