All told, these are pretty good times for US manufacturers, even with US tariffs on steel and many products from China impacting supply chain costs.
Supply Chain Digest Says... |
|
|
So good that the largest share of manufacturers in at least a decade is spending to expand facilities.
And US manufacturing construction spending hit a 16-month high in September, according to the Census Bureau.
That's because for many, demand remains strong. For example, travel-trailer manufacturer Airstream, owned by Thor Industries, broke ground in August on a $40 million factory adjacent to its existing plant in Jackson Center, Ohio because the existing factory had not been able to meet customer demand for three straight years.
But as they expand, soaring logistics cost and human capital considerations are huge factors in deciding where to locate.
As reported in the Wall Street Journal, Ferrellgas Partners recently added two plants in recent to make and refill its Blue Rhino propane tanks that were closer to customers. The new factories in Alabama and California will allow the company to reduce transport costs by as much as $3 million annually.
"The freight savings is so extraordinary," Paul Haeder, Blue Rhino's director of production, told the Journal.
Similar story for Italian tissue-paper maker Sofidel, which opened its sixth US plant in Circleville, Ohio, in October. It plans to open another in Oklahoma in 2020, and said it might add a few more elsewhere in the US to make its products as close to customers as possible to speed up delivery times and cut freight costs.
(See More Below)
|
CATEGORY SPONSOR: SOFTEON |
|
|
|
|
But getting closer to customers to reduce logistics costs only works if there is a sufficient labor force to fill the factories. Unemployment is at the lowest point in nearly half a century, and recently, in a rarely seen inversion, there have been more job openings posted in the US than there have been unemployed workers to fill them.
And there seems to be no end in sight to the extremely tight labor market. Manufacturing payrolls rose by 32,000 workers in October, the biggest monthly increase this year, and that number surely would have been higher if manufacturers could have found more employees.
So, Airstream CEO Bob Wheeler said the company thought about building a plant in the Western US, near many of its customers, but decided against it.
"We just didn't have any confidence we could recreate the workforce," he said.
Interestingly, manufacturers are citing constraints in both parts/materials and logistics capacity as the biggest obstacles to high production volumes, as can be seen in the chart below, based on survey data obtained by the US Census Bureau:
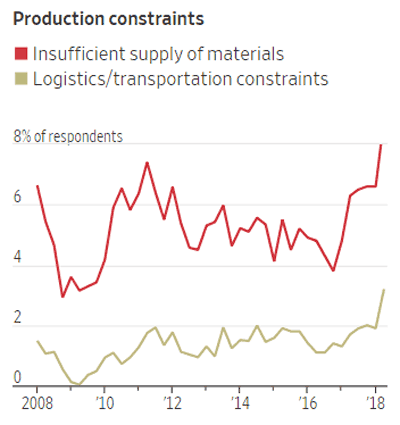
Source: Wall Street Journal
All this shows supply chain strategies are evolving quickly, with the tariff wars certainly driving some of that change.
"Globalization is becoming regionalization, and regionalization is becoming intra-national," Tom Linton, chief supply chain officer at contract manufacturer Flex.
Are you seeing plant location decisions being made to reduce logistics costs? Let us your thoughts at the Feedback section below or the link above to send an email.
Your Comments/Feedback
|