There really are several trends pushing US companies to consider moving at least some production back to US shores.
Those include rising wages offshore, especially in China; pressures to shorten supply chains and become more responsive; and a new president who has vowed to rejuvenate American manufacturing might, and may change tax and other policies to encourage Made in USA.
Supply Chain Digest Says... |
|
|
Companies are taking notice, and many are making the move back to the US - but the journey is often not be easy nor inexpensive.
For example, the Wall Street Journal recently told the story of a company called GAM Enterprises, an Illinois-based manufacturer of manufactuprecision mechanical components used in factory automation. The company started returning some manufacturing to the US three years ago, looking to reduce lead times.
There were challenges. The move ultimately cost the small company almost $4 million and required technical and financial assistance from Illinois and the US Commerce Department's Manufacturing Extension Partnership. It also had huge troubles finding machinists who could operate new small-batch production technology. Even after resorting to a recruiter to fill the spots, the new hires required months of on-the-job training.
But despite all that, it is really happening at GAM. The company doubled its workforce to 30 employees and now makes more than half its components domestically, up from 11% four years ago.
Reshoring is especially challenging for smaller manufacturers. They generally have limited funds, and maybe more importantly lack easy access to credit that most larger firms, especially public companies, enjoy.
And many firms run into a lack of US suppliers for key components, as thousands of factories closed their doors over the past two decades, victims of the offshoring wave. As can be seen in the seen in the chart below, the number of US factories has declined from about 400,000 in 2001 to more like 340,000 in recent years, eliminating waves of potential suppliers in many sectors.
Number of US Factories Down by 20% Since 2001
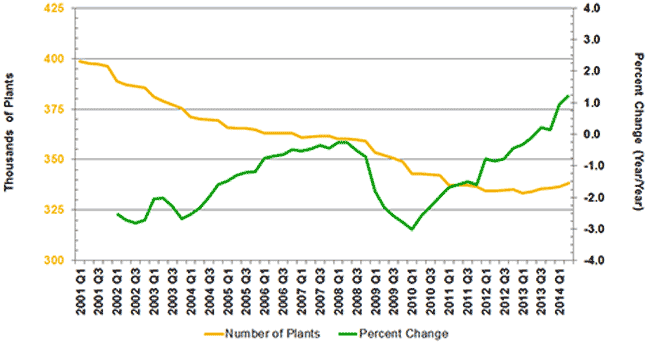
Source: US Bureau of Labor Statistics
The lack of a supply base is a barrier to US production that is cited by many existing companies and potential entrepreneurs considering starting US-based manufacturing firms.
Take the example of a company Mobile Outfitters, which sells cellphone accessories. The company produces most of its screen protectors in-house or under contract with US manufacturers, the Wall Street Journal reports. But the Philadelphia company, which has 18 employees, hasn't been able to make some products domestically because of production complexity, such as an ultrathin bumper that it imports from South Korea.
"Cost is not our issue, it is purely the complexity. We spent six months talking to US manufacturers, all who told us what we're trying to accomplish 'is not possible,'" said co-founder Eric Griffin, who expects to sell 250,000 of the items this year. "We looked overseas and got this beautiful product that has everything we wanted."
(Article Continued Below)
|
CATEGORY SPONSOR: SOFTEON |
|
|
|
|
The situation is even worse for a company called ElliptiGO, wich makes elliptical exercise bikes. While some of the basic frames for the machines are built in the US, most of the nearly 30 parts used to build a single cycle are made in Asia - with US suppliers basically impossible to find. As a result, the possibility of reshoring production here is a non-starter, even though the market for the end product in the US remains strong.
There are exceptions to this supply challenge. The Wall Street Journal also cited the case of Horst Engineering & Manufacturing Co., a Connecticut maker of precision machine components. The company recently shut down a nine-year-old facility in Mexico and opened a new, 16,000-square-foot shop in the state. Now located four miles from its two older plants and within 30 minutes of most of the company's main suppliers, "it definitely reduces the complexity of our business," said Arthur Roti, general manager of the family-run business. "That supply chain doesn't exist in Mexico."
Despite the challenges, many companies are still looking at reshoring. About 70% of US and European manufacturing companies said that they were considering moving production closer to their home countries, according to a 2016 survey by the consulting firm AlixPartners. That is up from 40% in 2015, according to the survey, which included responses from 107 small, midsize and large companies.
In addition, the use of more robotics is likely to make the US more competitive versus many foreign rivals, as the technology takes much of the labor costs that drove offshore production out of the equation. The problem, however, is that the number of US jobs in factories is reduced as a result, often substantially, from the use of the robots.
The economics of robotics continues to become more attractive. Owning and operating a robotic spot welder cost an average $182,000 in 2005 and $133,000 in 2014 and will likely run $103,000 by 2025, Boston Consulting says. Robots will shrink labor costs by 22% in the United States, 25% in Japan and 33% in South Korea, the firm estimates.
What are the challenges in bringing production back to the US? How big is the supply base issue? Let us know your thoughts at the Feedback section below.
Your Comments/Feedback
|
Shelley Jordan
Industrial & Supply Chain Engineer & Consultant / Partner, Synergy Solutions Group |
Posted on: Apr, 19 2017 |
|
I agree with a lot of the obstacles in the article in bringing production back to the USA. However, I do believe that it is a matter of time and that we can bring production back to the USA. The more complex the production is in terms of the number of supplies and complexity of supplies, the complexity of manufacturing machinery, the longer it will take. However, that does not mean that the production will not occur in the U.S.
Just like over time manufacturing left U.S., it can come back. Things happen in cycles. I am a supply chain strategist and have been involved in long term planning for companies for many years and know that when you have a goal and you stick with a plan, you will accomplish your goal.
Additionally, we have so many great universities and young engineers in U.S., even ones that came here from other countries that would rather stay here and work, if the work is here. So it is a matter of putting these engineers to work in manufacturing, research, management, training, development, and more. One major area that is offshore and not here is high tech involving electrical engineering. But I know that we have great electrical engineers here. Are they all leaving and going overseas to work or are they not staying in their field because there aren't any jobs? A major need we do have for them is to ramp up manufacturing of anything involving EE in U.S. I believe that covers a lot of our supplies that are stuck in other countries.
Also, if each of the U.S. manufacturers were to define their goals and the problems in the way of their goals and which supplies are not here, then there could be a way to collaborate with other companies that also have the same problems and missing the same supplies. I believe that the problems can be solved faster (such as ways to train workers faster and better). For the supplies that are not developed here, there are many companies that need the same supplies, so if it is known across the U.S. what supplies are required, then a bigger manufacturer can be created (maybe a smaller one exists but is having trouble because they are small), to produce these supplies at lower costs and higher quality given that we do have the expertise in U.S. and people can be trained.
It is all a matter of planning, time management and staying focused and believing in your company and the U.S. and beyond that collaboration.
|
|
|