RSR Benchmark Report on Supply Chain Execution
The analysts at Retail Systems Research are out with their latest benchmark report on Supply Chain Execution.
Highlights of the research include:
• The effect Amazon has had on other retailers is profound. Retail winners believe one of their best chances to compete is by using any stores they have in a more meaningful way - as both a way to fulfill orders and to process returns.
Supply Chain Digest Says... |
 |
2017 may go down as the year retailers started to look seriously at reducing supply chain variability driven by vendor performance. |
 |
|
|
• When it comes to opportunities, retail winners look to add same-day delivery capabilities, and are open to adding more local distribution centers for forward-positioned inventory to help make that happen. Under-performers see the same opportunity, but from a very different perspective; they want to reduce inventory investments without impacting sales - an unrealistic goal, RSR says.
• Before building the business case for significant changes to the supply chain, most retailers want to address the issue of inventory visibility and accuracy. ROI is not relevant.
• The number of retailers that have achieved "a lot of visibility" has significantly improved even from the 2015 supply chain benchmark. RSR notes that inventory visibility enables other supply chain improvements, and the best performers are already using it as a competitive wedge to further separate themselves from average and under-performers.
However, even given that last point retailers don't have a high level of trust in their metrics. As seen in the chart below from the report, for example, only a little more than half of retailers have high levels of confidence in key supply chain related metrics such as inventory levels at the store and the DC. Only slightly more than one-third have a high level of confidence in predicted DC inventory levels.
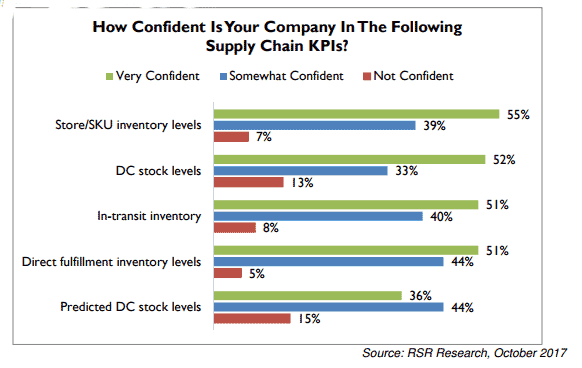
Visit the Retail Vendor Performance Management home page to learn more
and subscribe to the monthly newsletter.
There was surprisingly little focus on working with vendors in the report, but that said here are a few data points.
50% of retail winners have a high level of concern vendors will go direct to consumer faster than they can, versus just 15% of all other respondents.
In terms of opportunities for improving supply chain execution, better collaboration with trading partners was well down the list, cited by about 20% of respondents as being in the top three. Adding more local distribution centers topped the list.
The full benchmark report is available for free at the RSR web site with registration.
Straight Talk on RFID from Retail Panel
Since Walmart announced its ultimately failed RFID mandate back in 2003, it has been generally been difficult to get straight talk about the technology and its adoption due to much hype from the RFID system vendor community - and in some cases adopters of the technology themselves.
So it was refreshing to see research firm the Platt Retail Institute conduct a very balanced interview with three retailers who were very realistic about RFID adoption, benefits and challenges.
Here are some highlights:
Karl Bracken, senior vice president, supply chain transformation, Target, said that while the company's goal is to eventually tag all SKUs and categories, the reality, Bracken said, is that for Target the RFID ROI is different across product categories, of which Target has many.
It is still difficult to read tags on say bottles of water and certain electronics products, Bracken said, while a category such as cosmetics - which has inventory accuracy issues - is nevertheless challenged due to tag placement issues and difficulty reading many RFID tags in a small area.
Consistent reductions in tag and reader costs is helping ROI in more categories, Bracken said, adding that RFID ROI in retail can be challenging because it often depends on estimates of increases sales from more accurate inventory counts, especially when stores implement ecommerce efulfillment from stores.
Rene Saroukhanoff, senior director of in global merchandise planning, reporting & analytics at Levi Strauss, noted that getting results in-store pilots is much different than making that happen across hundreds of stores.
"There are impacts to business process. There's employee training. Any time you're touching store operations, it becomes a bit of a big deal,” Saroukhanoff added.
Allan Smith, former CIO at retailer Lululemon, interestingly noted that the benefits from moving RFID further upstream from the store is more challenged than you might think.
"When we started establishing priorities, we found that what really causes the inaccuracy at the end of the day is the human touch points with product. In the store is where that happens the most. As you move up the supply chain, there are fewer touches to your individual products. It's more case and pallet level,” Smith observed - meaning the ROI is harder to find.
It should be mentioned that any vendor RFID tagging program must be supported by a compliance management process in just the same way the bar code labeling has been monitored by many retailers for years. There are many ways there can be issues with vendor tagged merchandise, which often result in costly retagging at the DC or store. Compliance Networks is ready to work with retailers on vendor RFID compliance.
The Value of Reducing Vendor Variability
2017 may go down as the year retailers started to look seriously at reducing supply chain variability driven by vendor performance, with Walmart and Target both announcing major initiatives in this area.
More on this soon from the Retail Vendor Performance Management Bulletin - and of course vendor compliance is at the core of such programs.
Your Comments/Feedback
|