In the March 2017 the Retail Performance Management Bulletin, we discussed the roles of ASN performance and carton content accuracy in facilitating inventory availability for the "now economy." That article (Retailers are Driving Improved ASN Performance at Vendors) tackled the issues of why ASN accuracy is critical. This time, we focus on how ASN performance improvements are being achieved.
Compliance Networks Says... |
 |
As long as randomization is ensured, the samples provide virtually identical performance characteristics relative to those of the overall order. |
 |
|
|
These important issues were addressed through expert interviews and surveys in the most recent ASN study led by the Center for Supply Chain Innovation at Auburn University. We talked to a dozen leading suppliers and retailers about best-in-class practices for improving ASN performance.
The table below highlights the retailers' desired supplier capabilities. Though most suppliers have not fully developed these advanced levels of expertise, some are leading the pack. Discussed below are two best-in-class processes for ensuring retailer satisfaction, inventory accuracy, and chargeback reduction.
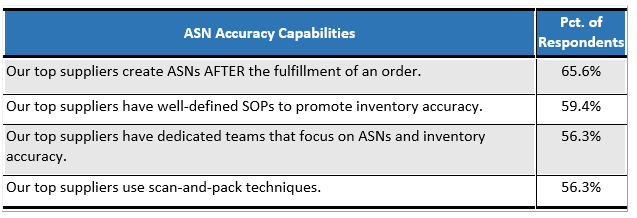
Visit the Retail Vendor Performance Management home page to learn more
and subscribe to the monthly newsletter.
Best Practice 1: The smartest move that suppliers can make is to combine the use of scan-and-pack processes with post order picking paperwork creation. With scan-and-pack, the supplier's distribution center associates scan each item's bar code label as they pick and fill the carton for a retailer order.
An apparel executive explains this best practice: "We scan and pack out all cartons in all of our buildings. That's how we ensure our accuracy. The scans are recorded and then when you're done packing the carton, the carton label is produced. The carton number is associated with the scan of all the pieces that were put into that carton. We build the ASN from this information when the truck leaves our building."
By delaying ASN creation until after the order is complete, potential misinformation errors are avoided.
Best Practice 2: Sampling is used to speed the flow of goods and reduce inspection costs without sacrificing audit integrity. Rather than count the contents of every case, retailers randomly select cases from an inbound shipment for comparison to the ASN documentation. Suppliers perform similar sampling audits with their offshore manufacturing facilities at their US distribution facilities. Many also perform audits of their distribution employees to ensure order picking and shipping accuracy.
Sampling lets the retailers and suppliers draw conclusions about the performance of their upstream supply chain partners. As long as randomization is ensured, the samples provide virtually identical performance characteristics relative to those of the overall order.
"We take the first 10% of the cartons and we check every unit against the ASN," explains a retail executive. "If there's even one error, then we check every carton on the purchase order. If we get through 10% without finding an error, then the remaining 90% flow through and we'll do an assumed receipt based off of the ASN."
Leading companies create programs that base sample frequency and size on past performance. All orders from new suppliers are audited until they achieve an acceptable level of performance. As consistent performance is achieved and trust is built, the supplier status level increases and the audit scope is reduced. When a supplier performs flawlessly, the sampling activity is eliminated or greatly streamlined.
"Once a vendor has achieved gold status, we can actually perform the receipt against the ASN without performing a QA check," explains the retailer.
ASN accuracy and carton content integrity are never-ending battles. Suppliers and retailers must work closely to develop collaborative processes to promote perfect order fulfillment. That involves well-linked systems, ongoing communication, and rapid problem resolution. As that is achieved, revenue enhancement will come from greater product on-shelf availability rather than vendor chargebacks.
Watch for the release of the 2017 ASN and Carton Content Accuracy Report in September, sponsored by Compliance Networks.
Any comments on this article? Please send below.
Your Comments/Feedback
|