Last week, I provided a trip report of the 2016 JDA Focus user conference in Nashville, primarily focused on where JDA is heading as a whole.
This week, I am back with some summaries of the best keynote and breakout presentations. As always, in my selection of sessions to attend and then these summaries, I try to focus on insights and practices that will be of potential use to all readers, not just JDA customers.
Gilmore Says.... |
 |
IKEA plans to extend the system to its suppliers' suppliers, and says it had had a demonstrable impact on availability at the store. |
 |
What do you say? |
|
Click here to send us your comments |
|
|
|
|
That said, I am going first to briefly summarize the discussion at what JDA calls its Demand Optimization Council, a group of some of its best retail, consumer goods and wholesale customers that meets the day before the conference formally starts, with presentations by members on some theme. This year it was new product introductions and the supply chain.
I am there as a participant, and thus very limited in what I can report back, but can comment on some things at a high level, starting with a couple of interesting notes. One large regional grocery chain has a new mandate to achieve 100% in stocks in store. It already had very high service levels, but the new goal is zero out-of-stocks.
As you might imagine, a company manager said it really needs to make some significant changes in processes to reach to the goal. Can it really be done? More importantly, is it worth it? I would say those are both open questions. But this is now the quest.
Another retail DOC member interestingly noted that the company had moved in the last year to what is called an "open-to-buy” concept, where merchants are basically given a budget for a given category that constrains their spending, with the obvious goal of reducing inventories.
But it is not working out nearly as well as expected. Why? Because if something is a hot seller, of course the buyer can purchase more from suppliers to take advantage of the opportunity. No one is going to constrain the spend to the original open-to-buy number and lose sales for the SKUs that are exceeding forecast. Meanwhile. the buyers have probably hit their open-to-buy maxes on other items. Interesting.
On NPI, virtually every company has a fairly sophisticated process for getting new product to market, with many stages and several gates along the way. A few were a bit more sophisticated than others - yet, as other research has confirmed over many years, the majority of new product fail, either completely and are pulled from market, or do not meet sales expectations. In a survey I did of about 15 DOC members prior to the meeting, the highest score anyone had for the percent of new products that meet sales expectations was 50%. The lowest was 10%, with the average in the 30% range.
So, as I somewhat provocatively observed at the end of the meeting, are we all just fooling ourselves? What would happen if companies got much more rigorous about NPI forecasting? Would we have a lot fewer new products? I have an emerging theory that we need to move to a more probabilistic approach to NPI - more on that before too long.
In the one sort of meaty non-JDA keynote on Monday, analyst Kevin O'Mara of Supply Chain World emphasized the good that supply chains and practitioners are doing to make the world a better place. He noted that activists often target industry as the bad guys, when they usually have it exactly backwards - industry is what is driving gains against hunger and for a clean environment and improved healthcare, etc.
O'Mara believes that a combination of continued supply chain productivity and flattening population growth (likely to even decline soon in Asia) could enable us to largely eliminate world hunger by 2050, a possibility that most would have laughed at not many years ago. We'll see about that, but O'Mara's presentation was a very positive one for the supply chain discipline.
I noted last week that I would have liked to have seen a bit more "vision” about where supply chains are headed from JDA during the day 1 keynotes, but did not mention that this was partly offset by some half dozen "future” presentations on various topics, structured to look out five years as to changes we can expect.
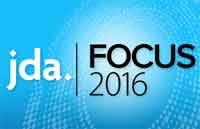
I went to two of these, one on supply chain generally (Kelly Thomas) and one on transportation/TMS (Fab Brasca), and both were very good. I am going to summarize each in future OnTarget newsletter articles, but will just note here that Brasca discussed how analytics across shippers running TMS in the Cloud could lead to valuable insights about what strategies work and what don't - but will shippers allow their data to be used in such a fashion, even if kept anonymous or aggregated? That will be interesting to see.
The best breakout of the two days was by a trio of managers from German semiconductor maker Infineon, on its journey to integrated business planning (IBP). Infineon has created a toolset and a process that completely links the three sides of what it calls the cube: the demand side, the operations or supply side, and the finance side.
The catalyst for the transformation, interestingly, was the recognition a few years ago that even modestly far out, Infineon simply could not forecast future demand very well. So it was agreed the company should just stop pretending that it could. Instead, the focus now is on presenting to executives and the board different scenarios, interlinked across the three dimensions I just mentioned, and forcing decisions at that level.
So the cube notion comes in because everything is completely interlinked. Make a change on the demand side in terms of volume or price, and the impact on operations and the financial plan is instantly adjusted and visible. The system also looks at investments in capacity that would be needed to support a given sales plan, and even considers the cost of idling a given production line or piece of equipment for some period of time.
So, for example, if a decision is made to not make investments in certain areas of manufacturing, then the system automatically constrains the sales plan, and therefore changes the financial plan. This is very cool, and is as good an example of IBP of anything I have heard.
On day 1, Mark Kidwell of OHL Logistics gave a good presentation on its implementation of JDA's workforce management in it many DCs. Kidwell noted early on that labor management is not an engineering or technology project, but a change management one. Right on.
A big part of the goal at OHL was to develop an incentive program for workers. The company actually had incentive programs in place but they varied by facility, and were based on far from perfect data from home grown systems, with a lot of key entry, such that OHL often had to pull incentive programs back because they were too costly - not a popular move for employees.
There was also time urgency to the project, and for that reason - as well as bang for the buck - OHL just applied engineered standards to three areas: putaway, picking and replenishment, which represent 80% of its direct labor costs. Kidwell said it's really not clear if there is a payback for going beyond those three tasks.
The system really just got going in early 2016, so results are not clear yet, but I am pretty sure Kidwell said productivity has already increased on average from 71% of standard when it turned the system on to 90%. That's quite a jump - and the system has allowed OHL to implemented incentive programs that are accurate and fair to the company and the workers.
Paul Bjornsson of IKEA gave a very good presentation on the retailer's development of a capacity management system for its 1000 suppliers. He started with some interesting questions, such as how do you really define capacity? What are the metrics or units of measure?
Turns out a few years ago IKEA mostly managed capacity locally, out of its different global procurement offices for the suppliers in each region, so there was no global view. In addition, there was no standard way to define or measure that capacity, and much of the data they did have was suspect, resulting often in overestimation of a given supplier's real capacity. This then led to many cancelled or partial fulfillment of IKEA purchase orders, Impacting product availability at the store.
IKEA has spent that last several years building a centralized, global system, starting out with some Excel and some homegrown tools, recently moving to a JDA product. How is the data collected? It starts basically with Excel templates completed by its suppliers, which are then generally followed up with actual site visits, and in some cases stop watches and other tools to get as accurate as it can for a given supplier's capacity.
It's organized by major product category - let's say window frames - and now IKEA can see what its global capacity is across all suppliers in that category. I also like the concept IKEA has adopted that it calls "demonstrated capacity.” So, if a supplier says it has a capacity of 1000, but it always delivers 800, the system changes the capacity to 800.
IKEA plans to extend the system to its suppliers' suppliers, and says it had had a demonstrable impact on availability at the store, such that the payback from its rather modest investment was just two days. Bjornsson has indications it has reduced inventory costs as well, but he needs a bit more time to prove that.
OK, good insights from JDA Focus 2016. I am off to both WERC and Gartner next week - look for summaries of each. Please say hello if you see me.
Any reaction to this this summary of JDA's 2016 breakout sessions ? Were you there? What were your thoughts? Let us know your thoughts at the Feedback section below.
Your Comments/Feedback
|