Holste Says... |
 |
Streamlining processes and taking full advantage of embedded equipment and system features should be the first steps in the quest to keep DC systems performing at their highest level. |
 |
What do you say? |
 |
Click here to send us your comments |
|
|
|
- One of the major challenges shippers face today relates to the down-sizing of packaging. Manufacturers are being forced to reduce package sizes to better accommodate demand for smaller units and/or quantities. This tends to increase the volume of small to very small (< 9″ lg.) cartons that have to be handled on conveyor and sorting systems.
The majority of powered roller conveyor installed in consumer goods distribution centers, are equipped with 1.9″ diameter carrying rollers spaced at 3″ centers. This works well when the smallest carton is 9″ long, or longer. Cartons shorter than 9″ can get stuck in the space between the rollers increasing the possibility of jams, frequent shut-downs, and product damage.
The good news is that a “modification” for this small carton handling problem may already be built-in. This is because when conveyor side frames are manufactured, the axle holes for the carrying rollers are punched at 1″ spacing. Therefore, if the conveyor needs to handle cartons less than 9″ in length, the carrying rollers can be spaced at 2″centers. Driving all those additional rollers may require an increase in motor horsepower along with other minor mechanical adjustments easily completed by the conveyor service provider. Once the modifications are completed the existing system will be able to handle a larger range of small cartons.
- Another update possibility is on systems that have mechanical sensors in the accumulation conveyor that no longer activate reliably (especially on small, and/or light weight cartons) and can be a performance as well as a maintenance issue. These mechanical sensors can be replaced with photo eye sensors. Retrofit kits for this fix are available from most conveyor manufacturers. This update could be done at the same time additional carrying rollers are added as described above.
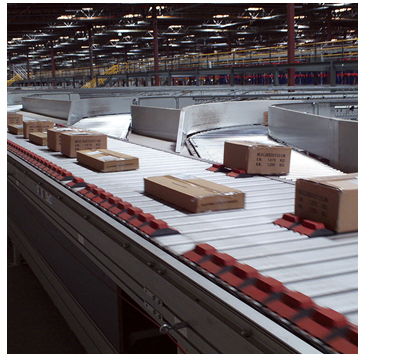
- Many shippers are experiencing higher case shipping volumes, which is the result of the higher order frequency of small packages. A good example can be found in the typical shipping sortation system. Many of these systems are capable of providing higher sorting rates than what was initially required. With a few simple equipment changes, like changing the ratio of the drive sprockets and re-calibrating the sorter tracking system (usually done automatically), higher speeds and sorting rates can be achieved.
- Another example where capacity can be increased would be to reduce gaps between cases at critical merge points and at the induction to the sorter, which will immediately increase throughput capacity. Control and software upgrades are readily available.
- You may also be surprised to find out that your current 1 or 2 level high picking module may be capable of supporting a 2nd or 3rd level. While you are in the picking module (if cartons are being picked from pallets) check the amount of clear space over the top of a full pallet load – because you may have sufficient space to add a shelf of carton flow lanes.
Industry experts know that oftentimes real payback can be found in thoroughly examining order processing, and smoothing out the peaks and valleys in receiving, inventory, picking, and shipping systems. Streamlining processes and taking full advantage of embedded equipment and system features should be the first steps in the quest to keep DC systems performing at their highest level. The above modifications are actually quite common and should be considered before making a large expenditure for new equipment. Still, in the final analysis, new more automated technology may be required in order to properly serve current and future customer needs.
Final Thoughts
The bottom line is that by making a few equipment and system operational updates you can pick more SKUs, handle a larger range of carton sizes, and ship more volume – all with essentially the same updated system.
Any reaction to this Expert Insight column? Send below.
Your Comments/Feedback
|