While traditional DCs are designed to handle medium to large order volumes, the Internet consumer typically orders one to two SKUs in small quantities. The frequency of these smaller orders can potentially be astronomical. Therefore, to avoid operational ciaos, shippers who are pursuing e-Commerce business must proactively adapt their operations to efficiently and productively satisfy this market segment.
The three main fulfillment areas impacted by internet orders include order picking, packaging, and returns. If the original operating plans did not include e-Commerce, the order fulfillment system may lack the required functionality to successfully support a high frequency of small orders. If that’s the case, there are a few operational changes that should be considered, such as:
Holste Says... |
 |
Success in the on-line sales marketplace then requires adopting a pick/pack strategy that provides the ability to easily process the number of orders during peak periods, with no additional labor and/or capital investment. |
 |
What do you say? |
 |
Click here to send us your comments |
|
|
|
- Optimize existing pick/pack operation relative to small single line orders
- Re-arrange and/or expand existing facility to include an e-fulfillment area
- Design/Build a new facility with integrated e-fulfillment capability
- Utilize a 3rd Party e-fulfillment center
- Set-up suppliers to ship direct to your internet customers
In general, establishing best practice operations for a successful e-fulfillment operation involves:
- Modifications to order entry software and control systems
- Operating a high-frequency, open-case (split-case) picking area
- Maintaining 100% inventory accuracy
- Utilizing advance picking technologies (Pick-to-Light, Voice, RF Terminals, and more automated methods)
- Achieving a one day or same day order shipping cycle time
- Handling a high number of small shipping packages
- Providing special packaging services (i.e. gift wrapping, monogramming)
- Supporting increased system transactions
- Running an efficient Reverse Logistics (Returns) Process
Because the majority of internet orders can be picked complete from one product location. There is no need to travel through multiple pick zones to complete these orders. Fast, efficient picking technologies include radio frequency (RF) terminals, voice recognition technology, and pick/put-to-light systems.
- In an RF terminal system, the location and quantity for each product is displayed on the terminal screen. Wrist mounted RF terminals are available to provide a more efficient RF picking operation.
- In a voice recognition system, terminals convert electronic text into voice commands that guide the operator during picking. A headset is worn to send and receive commands and the terminal receiver is worn around the operator’s waist.
- In a pick/put-to-light system, bay and location displays are illuminated to guide the operator through the picking process. Location buttons are used to confirm the completion of tasks. More advanced pick to-light systems exist that do not require the operator to confirm each pick because they are equipped with motion sensors that detect the operator’s arm movement when the pick face opening is crossed.
Comparing qualitative issues (see chart below) among these technologies will most likely show that a pick/put to light system provides the best solution, with the least risk. As shown in the following chart, depending on the weight or importance of each criteria and the shipper’s specific application, each of these technologies provides a viable solution for e-commerce picking operations.
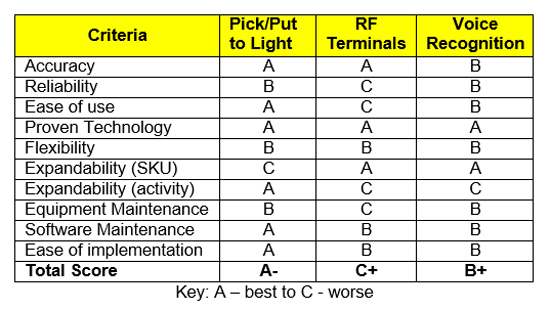
Financially, there are trade-offs between technologies. A pick/put to light system has a high initial investment cost, but lower annual labor costs. An RF terminal system has a medium to low initial investment cost, but higher annual labor costs. And, voice system investment and labor costs rank somewhere in the middle.
The investment cost for a pick to light system is impacted more by an increase in the number of pick locations rather than an increase in order activity. Conversely, RF terminal and voice systems are impacted by order activity requiring additional operators.
Final Thoughts
The business level of e-commerce sales volume can be unpredictable, but generally falls into the category of stable product lines and a high fluctuation in order activity. Success in the on-line sales marketplace then requires adopting a pick/pack strategy that provides the ability to easily process the number of orders during peak periods, with no additional labor and/or capital investment.
The best opportunity to learn more about e-Commerce order fulfillment and shipping technologies can be found at: ProMat 2017 April 3-6, 2017, Chicago, IL. www.promatshow.com
Any reaction to this Expert Insight column? Send below.
Your Comments/Feedback
|