As I have written before, I actually believe now is a fantastic time to rethink and rebuild your supply chain strategy.
Obviously, there are some companies (e.g., automotive OEMs and their long suffering suppliers, some retailers, and others) for which it is, or has been, just a game of survival. We can put them in a separate category.
Most others, understandably, have been in cost-cutting mode, sometimes in the extreme, even if the overall survival of the company is not really in doubt. There are a lot of distribution center consolidation projects going on right now, as one of just many examples of the kinds of things companies are doing. In fact, I recently spoke to one book publisher that was cramming three former DCs into one building and, for now, was going to operate them all independently, with their own footprint in the DC, warehouse management systems, etc., I think because they had immediate opportunities to get out of the other two leases.
Gilmore Says: |
|
“Whether it’s in our personal lives or the business, the “urgent” tends to crowd out the “important.” "
What do you say?
|
Send us your Feedback here
|
|
Amidst all that though, I really believe it is also a time to really think through your “supply chain of the future.” Or maybe just your “distribution center of the future,” or whatever your neck of the woods happens to be.
Another view of the same thing: I recently heard legendary strategy guru Michael Porter of Harvard say “Now is the time to do the really hard things that you just haven’t been able to get done before.”
In other words, a lot of the things that seemed like barriers to making something happen in the past may not loom so large right now. Just as importantly, the “change management” issues that are key to the success of any initiative, and which have killed or weakened many of them, may be a lot more manageable in the current environment as well.
I believe it was in the early 1990s that Stephen Covey wrote his famous book on “The Seven Habits of Highly Effective People.” I was early in my career then, and for those that started out later than that, let me just say that the book and Covey himself were everywhere for a few years. Many companies bought related training materials, etc. We got “Seven Habits of Highly Effective Corporations, and many other permutations of the first book.
It is a good work. Though, I must say that I don’t specifically remember a single one of the seven habits; I hope I am following at least a few of them.
But what almost everyone exposed to the book remembers is this: the urgent drives out the important.
Covey had a famous quadrant with two dimensions: urgency and importance, each high and low. As you can imagine, at whatever level you are, things that are both “urgent and important” get high attention and action, as they should. The exact opposite is true for “unimportant and not urgent.” If you are working there, something is wrong. Or, if it has to be done, that effort is obviously a candidate for process re-engineering and outsourcing.
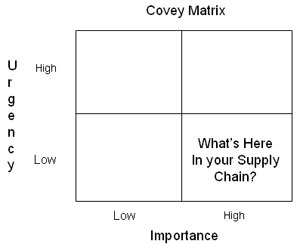
It’s the other quadrants that cause the problems. Whether it’s in our personal lives or the business, the “urgent” tends to crowd out the “important.” The “urgency” makes us devote time and resources, even if the issue itself is really not that impactful.
The real key, Covey said, was disciplining yourself to focus on the things that are important but not urgent. In both our business and personal lives, and the “lives” of companies themselves, we tend to simply put off items in this quadrant.
It is not hard in either personal or business situations to think of many examples of important, but not urgent, needs that don’t get addressed in a timely fashion – or maybe at all. In the supply chain: SKU rationalization, network redesign, activity profiling in the DC, routing guide compliance, etc.
What I haven’t seen much written about in this context, however, is the role of your boss. Often (usually?) what is “urgent” for you is what is at the top of your boss’ current agenda, whether that’s the CEO, the VP of Supply Chain, or the distribution center manager.
So, whereas in our personal lives we might have more direct control over putting a focus on what is important but not urgent, in our business lives, often it is someone else who largely dictates our current focus. Often, we in fact believe that what is urgent to the boss is in fact not really that important at all in the bigger picture. Not that that is going to change anything. Been there, done that. I am sure I have had at times a similar effect on the people who reported to me.
Given conditions now, we probably have an increase in things that are both urgent and important. Sony, for example, citing not only overall slowdown in consumer spending, but also the “commoditization” of consumer electronics, is at last taking real action to spur its “sluggish” supply chain.
"We have a weak supply chain, we don't have common procurement, and we need to get that done. The factory organizations need to be rationalized,” CEO Howard Stringer recently said.
Regardless, I would just argue you should be using this time in part to tackle the tough things you know should be done, but you haven’t made happen yet, and to look at how what changes you can make that will not only reduce costs now, but give you a better platform and increased performance in the future.
“Urgency” right now is down with lower volumes and companies playing everything safe. Use that to focus on the important. Recovery is really not that far away.
Let us know your thoughts.
Web Page/Printable Version of Column
|