From SCDigest's On-Target E-Magazine
- Dec. 12, 2012 -
Logistics News: Batch Picking and Sortation Systems in Distribution
Understanding How Batch Picking Delivers ROI from Sortation System Investment; Throughput Increases Can be Just as Important as Operational Savings
SCDigest Editorial Staff
Automated sortation systems have provided significant productivity and/or throughput gains for hundreds of distribution centers since the late 1970s.
That distinction (productivity versus throughput) is important because while investment in sortation often provides a solid enough payback based on improved labor efficiencies, even when the core operational ROI is dicey, in many cases the system can still be justified by improved throughput at an existing distribution center that can avoid or defer investment in a new or larger DC. Since that facility expansion or build would involve many millions of dollars in capital, a few million for a sortation system may seem cheap by comparison.
SCDigest Says: |
 |
Are the labor savings from batch picking significant enough to justify the investments in the sortation system? That of course is the multi-million dollar question. |
|
What Do You Say?
|
|
|
|
In most scenarios, the fundamental concept is to improve the "case picking" process by adopting some form of "batch order picking." As described and illustrated in the below, in traditional "discrete" order picking systems, associates pick at an individual order level, with each picker visiting a picking location separately for each order line.
In other words, the driver of picking activity in discrete picking is the individual order. A pick face is visited each time for each order that contains that SKU. With batch picking, however, the driver of picker activity is instead the SKU/Location.
With batch picking, order lines are instead combined (usually by a Warehouse Management System), generally in a "wave," so that an order picker visits a location just one time across orders, using the sortation system to break down the cartons into discrete customer orders after the picks. This can substantially reduce picking labor costs through a reduction in travel time.
This mostly is executed in a "pick to belt" scenario, in which the picker puts the picked cases on a conveyor, which transports them out of the pick area for eventual merge onto the sortation conveyor itself. There, these picks will be combined with cartons coming from other areas, such as "split case" picking, and then diverted off the sorter for specific customer orders. In other words, cases are aggregated for picking, and then dis-aggregated for specific orders.
In recent years some experts and vendors have been arguing for a "waveless," more continuous form of order release that they believe can offer improved sorter utilization while keeping most of the labor efficiencies of traditional wave-based order release. More on that debate soon.
Note that while the downstream sortation is truly automated, the picking process is what might be termed "mechanized," with the belt conveyor takeaway assisting what is in effect manual case picking, albeit consolidated across orders in the wave.
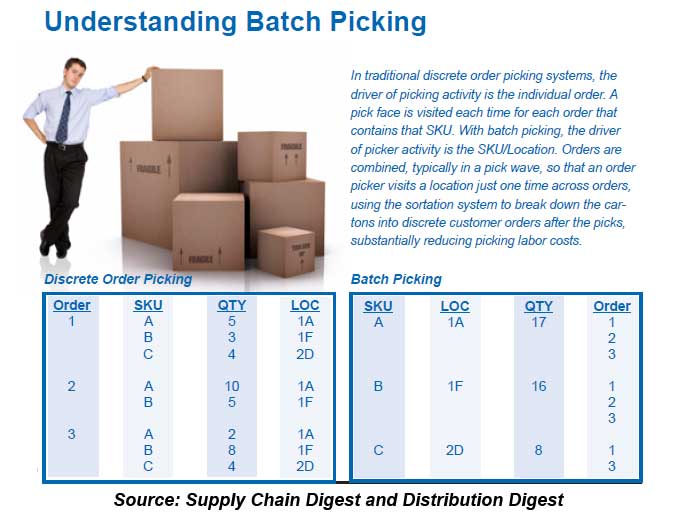
Order picking activity frequently represents as much as 50% of total DC labor costs. By enabling pickers to visit a location just one time per wave or other picking period, those labor costs can be significantly reduced. The sortation system does the work of separating the product back into discrete orders.
(Distribution/Materials Handling Story Continues Below
)
|