Distributing Order Management
Suddenly, order management is back in style - but now of a "distributed" kind.
Today, I will summarize some key points from our newest Supply Chain Digest Letter, this month on the very interesting topic of Distributed Order Management (DOM) systems. This really is one of the most dynamic areas of supply chain technology right now, for reasons I'll discuss below.
Many of you should have or will shortly be receiving a hard copy of that Letter. But to download an e-version, and to find some excellent white papers, see related videos and more, go to our Distributed Order Management Resources Page.
Throughout the mid-1990s to the early 2000s, order management was quite the hot topic. Part of that stemmed from a seminal Harvard Business Review article in 1992 called "Staple Yourself to an Order," by Benjamin Shapiro, Kasturi Rangan, and John Sviokla, which quite persuasively argued that "Every time a customer order is handled, the customer is being handled at the same time."
The "stapling" part suggested that executives should literally follow an order as it moves across various functions and processes, from the time the customer first begins to show interest in a company's product or service, all the way through to after sale delivery and follow through. For many companies then and now, that can involve quite a large number of steps (the article itself offered 10 steps in the "order management cycle"). The article is still highly relevant some 20 years later.
GILMORE SAYS: |
"The "order hub" concept needs to be powered by something like today's distributed order management software."
WHAT DO YOU SAY?
Send us your
feedback here
|
Back in that late 1990s period, order management was a frequent topic of industry analysts, and there was lots of talk about "the order is king" and notions along those lines. Thousands of companies implemented new order management systems as part of larger ERP implementations - even if often taking a step back in functionality from the mainframe-based systems most had built over many years. Those were difficult and expensive to maintain, but they did exactly what the company needed them to do. (There are more of these original systems out there, even if front ended with a more modern user interface to replace the green screen, than many observers realize.)
However, many companies had separate systems for each factory, and customers had to place orders at each facility, leading to separate invoices from each location. ERP was often implemented in part to solve that problem.
So, in a greatly condensed version of the story, by about 2005 or so, most companies had placed their ERP bets, and the topic of Order Management dramatically dropped off as a matter of industry discussion and the technology priority list of companies.
But also in the late 1990s, the roots of what we call today Distributed Order Management came into being. Actually, one of the true pioneers was a company called Yantra, which was later acquired by Sterling Commerce, which was in turn acquired by IBM, which is now one of the market's DOM leaders.
Yantra was primarily trying to solve the problems of the e-commerce merchants, which often didn't carry any inventory themselves, but had to source and coordinate fulfillment across dozens of hundreds of suppliers, often in "drop ship" mode.
But the e-commerce bubble burst. DOM solutions hung around, finding customers here and there, but struggled to gain critical mass. But over the last 2-3 years, that has started to change dramatically. Why? Three main reasons.
1. Multi-Channel Commerce: Companies in many industries, particularly but by no means exclusively retail, now find that they must manage and execute holistically across multiple channels, such as traditional brick and mortar stores, various forms of e-commerce, a catalog channel, order in-store for home delivery, and other channels perhaps coming soon (vending, kiosks, etc.). This presents a number of challenges around inventory management and the need to consistently present pricing, fulfillment, and other details regardless of point of interaction (POI).
2. Multiple ERP Systems: A funny thing happened on the way to single system ERP nirvana: a combination of roll-out challenges and mergers and acquisitions often left manufacturers or distributors with multiple ERP systems and/or multiple versions of a single system vendor. This led to the concept of "order hub," a central place for managing orders and their fulfillment across disparate systems. An order management system of order management systems, if you will.
3. Increased Customer and Competitive Pressures: For a variety of reasons, such as virtualization, order management and fulfillment seem to just getting harder, while companies continue to push for greater inventory efficiency and fulfillment precision. Existing systems often just weren't very good at that.
DOM technology is capable of addressing all three of these challenges. The "order hub" concept needs to be powered by something like today's distributed order management software, for example. While a few companies have tried to build their own order hub technology, like most other areas of software the commercial solutions today have grown so powerful in most cases that it rarely makes sense to recreate the order management wheel.
In retail, almost everyone is looking for more support for multi-channel strategies, with all the permutations of order online, pick-up in store, return anywhere, etc. Some articles, however, will position DOM as almost exclusively a retail phenomenon, but that is far from the case. Though the needs differ, companies in many industries - from service parts to consumer goods - have needs for and have deployed DOM technology. The full Letter has a nice sidebar on the needs for DOM by different sectors.
What exactly does a DOM system do? Again it varies by industry, and I can't fully explain in the space I have here what we provide in the full 16-page Letter, but in great summary one can think of a DOM system as being a flexible order management engine that can capture or bring in orders from multiple channels or points of interaction (POIs), directly or indirectly, and then determine the best fulfillment strategy considering customer service commitments, inventory placements, shipping costs, and much more.
The twin hearts or the system, if you will, should be the ability to model the full order lifecycle, and a powerful rules-engine in which order management and fulfillment process decisions can be defined for automatic execution. But there can be big differences across vendors in how both of these are handled.
So, I am out of space, but will note the Letter also contains a nice summary of a recent article by Gartner's Jeff Woods on understanding order management "styles" - the different types of order execution processes out there, and a reminder of the need for companies to understand which of the eight order management "metatypes" exist in your company.
Yes, order management is back, and I think that's good to see. The order really is still king, whether it's "distributed" or not.
Again, you'll find the Letter and much more at the Resources page.
What do you think of DOM technology? Are you using it? Where do you see this headed? Let us know your thoughts at the Feedback button below.
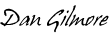
|
|
Supply Chain Graphic of the Week: Reader Submission on the Sorry State of US Bridges
This Week's Supply Chain by the Numbers for Dec. 2 2011:
- US Manufacturing Up - but China is Really Slowing
- Big Changes in Union Vote Rules
- Seagate Says Flood Disruption to Continue On
- Shippers Cheering Still Lower China to US Ocean Rates
|
CARTOON
CAPTION CONTEST WINNERS
ANNOUNCED THIS WEEK!
November 14, 2011 Contest
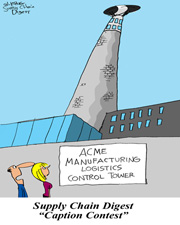
See This Week's Winner!
New Cartoon Monday on www.scdigest.com
|
NEW EXPERT CONTRIBUTOR
Discrete Manufacturers Forced to take Supply Chain Visibility from Wish List to Reality in 2012
By Marriam Kinny
Director, Industry Marketing
RedPrairie
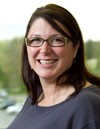
|
ONTARGET e-MAGAZINE
Last Chance Cartoon, TL Carrier Q3 Results, WMS Testing
and more
|
5th Annual Gartner-SCDigest
Supply Chain Study
Participate Now in this Important Study - Receive Complimentary Valuable Gartner Research
In addition to participating in this important research and seeing the results back in Q1 2012, respondents who complete the full survey can access immediately and at no charge any of the three valuable Gartner research reports:
• The Gartner Supply Chain Top 25 for 2011 -- a $995.00 value
• The Impact of the Cloud on Supply Chain Management -- a $495.00 value
• Supply Chain Management Market and Vendor Guide, 2010 -- a $995.00 value
TAKE THE SURVEY NOW
|
 |
Holste's Blog:Top Performing Companies Are Constantly Strive For Higher Levels Of Improvement
|
|
THIS WEEK ON
DISTRIBUTION DIGEST
Top Video: When it Comes to WMS User Testing, Short Cuts Usually Lead to Implementation Disaster
Top Story: Slowly, Warehouse Space Overcapacity is Turning, and Rates Heading Upward
Top Story: Managing Future Logistics Operations Will Require The Ability To Navigate Through Uncharted Waters - and Simulation will be Key
Visit Distribution Digest
|
SUPPLY CHAIN TRIVIA
In the most recent Logistics Performance Index from the World Bank (2010), what were the top five countries in terms of that evaluation of logistics competence (infrastructure, customs, talent, etc.)?
Answer Found at the Bottom of the Page |
|