From SCDigest's On-Target E-Magazine
Aug. 31, 2011
Logistics News: The Load Control Center Continues to Evolve
Opportunity Now for Many Shippers to Advance LCCs to Version 2.0, even as Many have Yet to Centralize
SCDigest Editorial Staff
Transportation is inherently an area that can benefit from at least a modest and sometimes high level of centralization. The concept of the centralized “load control center” (LCC) has been around for more than three decades, with most crediting industrial giant 3M as building the first LCC in North America in the late 1970s.
3M's initiative, one of SCDigest Top 10 Supply Chain Innovations of All-Time, used very manual methods of communication, and a transportation management system (TMS) of sorts, a main frame application originally developed by Schneider National for managing its network fleet that was re-engineered to meet the needs of a shipper. 3M LCC at first managed freight movements just around its own network of 41 plants and distribution centers.
SCDigest Says: |
 |
The "shared services" concept makes sense, as there are often many efficiencies to be gained by leveraging people, transportation spend, and load linking across more volume. |
|
What Do You Say?
|
|
|
|
Over succeeding years, of course, hundreds of other companies have followed suit, though many others still operate in a decentralized mode. What is a load control center? As seen in the graphic nearby, it is an approach to transportation in which most transportation planning and sourcing functions, and some execution processes, are pulled together into a single group, rather than being managed regionally or at individual ship sites.
The benefits of the LCC concept are many, and include:
• Ability to centralize transportation sourcing and better leverage total freight spend
• Development of standard processes that are consistent, rather than the disparate transportation processes found inherently in decentralized operations
• Greater efficiency – generally, a fewer number of planners are needed in total than when transportation is being managed at each site
• Improved opportunities for optimization through combining shipments or loads that were not visible to the planners previously
• Improved overall professionalism
• Improved electronic integration with carriers
• Opportunity for improved overall network visibility
• Improved metric management and therefore the chance to spot opportunities and drive continuous improvement
In fact, the decision to build a centralized transportation function remains the most common driver of adoption for Transportation Management Systems (TMS).
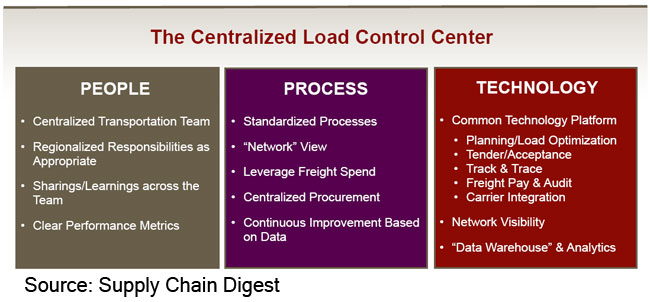
But as many companies now have years of experience in a centralized model, the concept is continuing to expand and evolve.
For example, many Load Control Centers were first developed to support a given business or division of a corporation. But now, the concept is expanding in some companies to a “shared services model,” in which a single centralized transportation group is set up to service the needs of multiple business units or divisions.
The “shared services” concept makes sense, as there are often many efficiencies to be gained by leveraging people, transportation spend, and load linking across more volume.
But it’s not that easy. Just as with plants or DCs that are reluctant to give up shipping control to a centralized LCC, business units may be reluctant to give up their own logistics destiny to a shared services group – especially if it grows out of another business unit that may deal with very different products or customers.
Consider an aluminum company, for example, that ships consumer products to retail and also rolls of aluminum to manufacturers on flatbed trucks. Should those two transportation operations be combined? That’s much less clear.
So, a shared services LCC may need to acquire and build a very diverse set of transportation planning and execution skills – and to operate truly “independent” from the division from which it arose.
Load Control Center Accounting is also Tricky
Another real challenge of the “shared services” model is the accounting.
In any sort of shared service set-up, different business units or product lines are “billed” for the cost of the freight itself and usually the cost of providing the services – in fact, the shared services organization often looks quite a lot like an internal 3PL or managed services provider.
The question of course, is how these costs will be calculated and “allocated.”
(Transportation Management Article Continued Below)
|