|
|
About the Author |
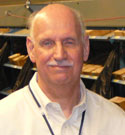 |
Cliff Holste is Supply Chain Digest's Material Handling Editor. With more than 30 years experience in designing and implementing material handling and order picking systems in distribution, Holste has worked with dozens of large and smaller companies to improve distribution performance. |
|
Logistics News
By Cliff Holste
April 2, 2014
|
|
Don't Confuse DC Shipping Volume with MHS Handling Capacity
Bridging The Gap Between DC Shipping Volume & Material Handling System Capacity
|
|
Shippers need to ship “X” amount of product per day. That volume can be expressed in a variety of ways, such as: pieces, units, cases, pounds, containers, pallets loads, trucks loads, etc. However, the order fulfillment conveyor system provider can only guarantee that the material handling system (MHS) is capable of delivering “Y” cartons per minute to the shipping dock. The “X” verse “Y” metrics are very different.
The first thing to understand about the shipping volume of a typical consumer goods DC is that not all of the volume being shipped goes through the MHS. A few obvious examples are as follows:
|
Holste Says: |
 |
DC shipping volume is a shared responsibility among the various system equipment, control, and software vendors with the company assuming performance risk relative to satisfying its daily shipping volume expectations. |
|
What Do You Say?
|
|
|
|
Previous Columns by
Cliff Holste |
|
|
|
• |
Drop shipments – they don’t actually flow through the DC,
|
|
• |
*full pallet loads of product that are basically crossed docked from receiving or WH storage to shipping by lift truck and/or AGV,
|
|
• |
* non-conveyable products,
|
|
• |
hazardous and/or dangerous materials,
|
|
• |
fragile items,
|
|
• |
high dollar value items – jewelry, small electronics, etc that are subject to shrinkage,
|
|
• |
various types of store displays, kits, etc.
|
|
|
|
|
* |
Note: While non-conveyable products typically represent less than 5% of the volume, full pallet loads of vendor product can be a significant percentage of the total DC shipping volume.
|
Because items such as the above are excluded from the MHS, there will be a gap and perhaps some confusion between the companies’ expected shipping volume and the MHS.
Understanding flow & volumetric data
When a company purchases a MHS, the system provider is obligated to satisfy specified handling rates for that system. Typically, in order to identify input and output rates for the MHS a flow chart is constructed – see “Uncovering Pathways To Greater DC Performance”. The flow chart shows all the departments that input volume into the system and the output requirements. At the completion of this flow charting analysis system planners will gain an understanding of what the handling rate requirements are for all of the functional areas within the system. This will then drive system design including equipment, controls, software, and cost.
It takes a considerable amount of analysis in order to determine the required handling rates of the various DC departments, i.e., receiving, picking, packing, shipping, etc. Handling rate calculations have a direct impact on system design, equipment selection, and cost. If the rates are understated, the company may need to frequently operate the system on an overtime schedule. If the rates are overstated, the system cost may be excessive.
Using volumetric data from the flow chart and factoring in forecasted sales growth, plus estimated system efficiency factors (loss time due to anticipated interruptions in flow), system designers will be able to determine flow rates for equipment and processes within the MHS. These flow rates are referred to as “Demonstrable Rate” and are used to “prove” system handling capability as follows:
|
|
Demonstrable Rate: |
During acceptance testing the MHS (some portion thereof) will be turned off and loaded with a given number of average carton sizes and/or totes. The system will then be turned on and allowed to run. The time it takes to transport the cases through that portion of the system will be noted. By simply dividing the number of cases by the run time in minutes (CPM) the demonstrable rate of each portion of the system can be verified. |
Theoretically, if the MHS can meet, or exceed, the rate requirements (as stated in the flow chart), the “physical” system is then proven to be capable of satisfying the company’s requirements. However, the company is responsible for providing sufficient staffing levels to satisfy input and output production requirements. Peak periods may require extended hours and/or higher staffing levels.
Once the completed and proven MHS is placed into daily operation there will most likely be operational factors beyond the control of the system provider that can impact on MHS capacity, such as:
|
|
Variation in carton length, and conveyable product mix from the original design specifications |
|
|
|
Excessive re-handling of cartons from re-circulation and/or cartons with bad (non-scannable) labels |
|
|
|
Shipping lane and/or dock space availability issues |
|
|
|
Inability to close out orders in a timely manner |
|
|
|
Staffing, operator training and order accuracy issues |
Taking the above into consideration, the company must understand the difference between demonstrable rates and expected shipping volume. There must be a clear understanding right from the get go as to who is responsible for satisfying expected shipping volume. For instance, when it is all said and done, if it takes more staff and/or time to ship the required volume than was originally forecasted, who is responsible?
An important clue lays in the fact that as long as the system provider can demonstrate that the MHS can perform at the specified rates, it has satisfied its contractual obligations – even if the overall DC operation is viewed as not meeting shipping volume expectations.
Many of these “risk” issues can be minimized (but not entirely eliminated) if the system provider is also the DC system planner/developer/designer. By accepting responsibility for the planning and development of the overall DC operation, the provider “owns” more of the integrated operational aspects of the DC relative to satisfying daily shipping volume requirements. However, this approach typically is based on a design-build negotiated contract instead of the more common bid-to-spec contract.
|
Final Thoughts
Much of the performance of a typical order fulfillment DC is beyond the control of the MHS provider. System providers can only take performance responsibility for what they provide and even that is limited to the unimpeded rate product moves through the system. Therefore, DC shipping volume is a shared responsibility among the various system equipment, control, and software vendors with the company assuming performance risk relative to satisfying its daily shipping volume expectations.
|
|
|
Recent Feedback |
No Feedback on this article yet
|
|
|
|
|
|
|