Supply Chain Comment: Three Ways to Minimize the Cost and Impact of a Product Recall
Identification, Automation, and Collaboration Must Form the Foundation of an Effective System
Ask anyone working in CPG, food service, automotive, pharmaceutical or life sciences industries and they will tell you their number one fear is a product recall. Barely a week goes by without the media covering a recall and, according to the Stericycle ExpertRECALL Quarterly Recall Index, there were 576 product recalls in the first quarter of 2012 alone.
Few industries are immune to the very public nature of a product recall, not to mention the financial fallout and potential liability issues. A May 2010 report issued by Deloitte on behalf of the Food Marketing Institute (FMI), the Grocery Manufacturers Association (GMA) and GS1 determined the average cost of a product recall to be $10 million. That cost alone is enough to bring a large public corporation to its knees, not to mention the unquantifiable effect on reputation.
Fralick Says: |
 |
Complicating issues is the reality that most companies today do not have the ability to see real-time inventory positions or manage inventory across their extended supply chains. . |
|
What Do You Say?
|
|
|
|
When performing a recall, time is of the essence. But managing, monitoring and auditing the procurement, production, storage, transportation and handling of inventory during a recall presents a significant challenge to businesses up and down the supply chain. As the complexities expand, so do the laws and regulations enacted by countries around the globe designed to govern food and product handling and ensure consumer safety.
A recent study of senior supply chain executives at 130 brands with revenues in excess of $500M revealed some disconcerting findings about the current state of their companies' trace, track and recall capabilities. The study revealed a surprising degree of confidence among almost 30 percent of the executives surveyed, despite the fact that almost half of the companies admitted their inability to execute a recall within hours. (The study cited can be downloaded at http://www.commerceinmotion.com/feature/on-the-trail-to-traceability.)
Other striking findings included:
• More than half of executives are concerned about their ability to isolate items with their own supply chain.
• Coordinating recall issues with suppliers and distributors is a real concern for almost 70 percent of executives surveyed.
• Less than 20 percent have deployed technology solutions to help fully-automate trace and recall processes.
• Forty-six percent said their companies are struggling to stay compliant with regulations.
Clearly there is room for improvement, especially with so much at stake. Today, the majority of businesses rely on spreadsheets or homegrown solutions to track products and processes. Fumbling through paperwork is not an optimal approach when you need the information immediately and to ensure you haven't missed anything.
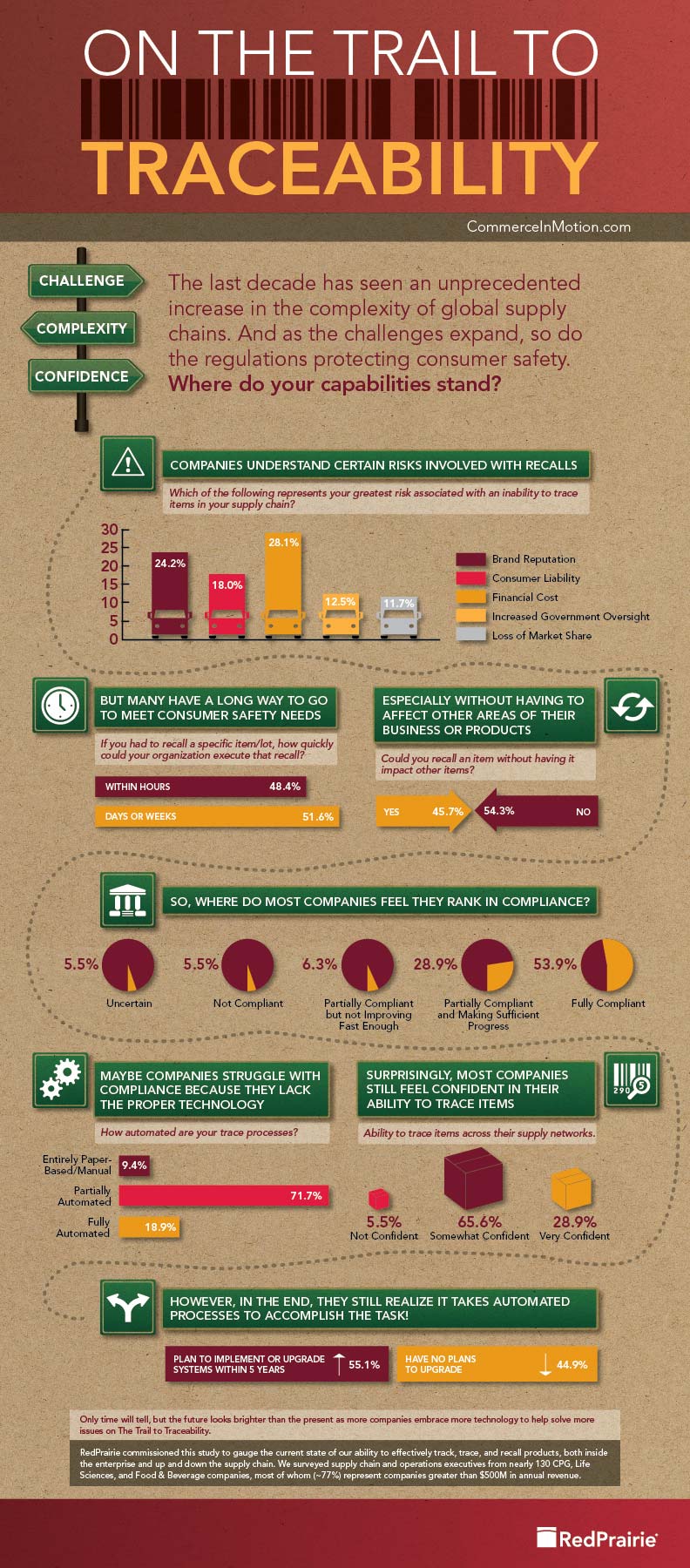
Complicating issues is the reality that most companies today do not have the ability to see real-time inventory positions or manage inventory across their extended supply chains.
Despite the immense impact of a product recall, there are actually three distinct ways to significantly improve trace and recall efficiency, and minimize the punitive effect on finances and brand.
• Identification: The importance of knowing, at any given moment, the location and volume of inventory, not just in your warehouses and distribution centers, but also units on the move, cannot be understated. Achieving a single view of inventory movement, not just within your own organization but also through the extended supply chain, is the single most important improvement you can make to optimize your traceability capabilities. What's more, the process does not end once the tainted item is recalled: inventory reconciliation and replenishment must happen.
• Automation: Deploying a system that can track products on a very granular level is critical to the traceability process. Solutions exist that can isolate a product lot right down to the specific license plate number of the pallet it resides upon. This level of precision not only focuses on the accuracy and speed of the recall process but also saves the cost and effort of recalling more inventory than necessary. Furthermore, these systems enable the real-time capture of detailed inventory information and order history, essential for any company striving for the ability to perform a "1-Touch Product Hold and Recall." Being able to issue targeted proactive notifications and narrowcasting alerts creates a more efficient recall process, minimizing supply chain disruption and panic.
• Collaboration: Product recalls have a ripple effect up and down the extended supply chain. Everyone in your network of suppliers and partners, all the way from raw materials through manufacturing and distribution to your customer-facing channels, is implicated in and has a role to play during a recall. Proactive communication and the real-time sharing of data between partners are fundamental. Systems must be able to send and receive information, no matter which platform they run on.
The opportunity exists today to substantially improve product trace and recall efficiencies with tangible benefits to risk and cost mitigation, compliance adherence and customer loyalty. After all, who has $10M to spare?
Agree or disagree with this experts' perspective? Let us know your thoughts at the Feedback section below.
|