|
|
|
|
 |
Supply
Chain by the Numbers |
|
|
|
- July 30, 2020 -
|
|
|
|
|
|
|
|
Worst Quarter for US GDP in History; Big Savings for Some for Moving Out of China, PwC Study Says; eTruck Maker Nikola Breaks Ground on Giant Factory; General Mills Needs more Co-Packers |
|
|
|
|
|
|
32.9% |
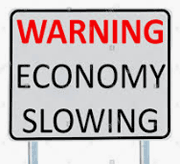 |
That was the record setting drop in US real gross domestic on an annualized basis in Q2, in the first estimate of economic output from the Commerce Dept. That after a much lower but still significant drop of 5% in Q1. The pandemic simply pushed the economy off a cliff. The second-quarter GDP drop was nearly four times worse than during the peak of the financial crisis, when the economy contracted at an annual rate of 8.4% in the fourth quarter of 2008. The drop in Q2 was the worst quarter on record.
The US only began keeping quarterly GDP records in 1947, so it's difficult to compare the current downturn to the Great Depression. That said, in 1932 the US is estimated to have seen economy contract 12.9%. What will Q3 bring? That is the trillion dollar question. |
|
|
|
|
|
|
That is how much some US manufacturers could save in total cost if they moved production out of China to Mexico. That according to a new report from the consultants at PwC. Moving to another low cost Asian country could generate 24% savings, PwC's analysis finds. Of course, it's not easy to pull out of China for many companies, given relationships with suppliers dating back many years. China's also offers well-developed transportation infrastructure, logistics, production capacity and scale. Nevertheless, PwC believes that the virus pandemic “is casting in stark relief vulnerabilities of global footprints that have been developing for several years." Moving some production out of China, even if it is just a “China + 1” strategy, could result in lower costs and greater supply chain resilience, the report says. Numerous factors are driving this strategic change, PwC adds, including rising labor and logistics costs in China, new tariffs and trade policies, and the growing need to be more responsive to meet regional and customer-centric demand. |
|
|
|
|
|
20% |
|
That's by about how much US food giant General Mills will increase its use of outside manufacturers – often referred to as co-packers in the consumer packaged goods sector – as demand for food products continues to soar in the stay at home economy created by the coronavirus crisis. General Mills like others is struggling to keep up with its own 24 production facilities. The company already uses some 200 co-packers, but is in the process of expanding that number and plans to keep most of them at least through next summer, the company CFO told the Wall Street Journal. Co-packers already produce about 30% of General Mills' North American products. The increased use of co-packers of course will come at a cost – the CFO said that the impact will be “tens of percentage points higher cost versus an internal manufacturing cost.” But it that is still a better choice than the cost of new or expanded factories – and a faster solution to the problem. The surge in demand could also disappear – CPG companies such as General Mills were actually seeing week growth before the pandemic - so the approach also reduces demand related risk. |
|
|
|
|
|
|
|
|
|
 |
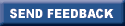 |
|
 |
![]() |
 |
|
|
 |
Feedback |
|
|
|
No Feedback on this article yet.
|
|
![]() |
|
|
|
![]() |
 |
![]() |
 |
|
|