 |
SUPPLY CHAIN NEWS BITES
|
Is It Time for Amazon Logistics?
|
|
 |
US Truckload Carriers Finally Starting to Add Capacity |
 |
Lego Caught Quite Bit Short on Brick Production
|
 |
eCommerce Sales Growth will Far Outpace Brock and Mortar Again this Year
|
 |
Warehouse Market Still Tight |
|
|
|
|
NORTHWESTERN UNIVERSITY'S ONLINE MASTER OF SCIENCE IN PREDICTIVE ANALYTICS |
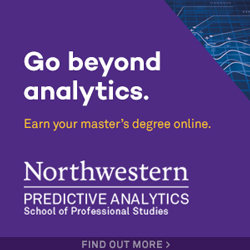
|
|
CARTOON CAPTION
CONTEST WINNERS ANNOUNCED |
October 13, 2015 Contest |
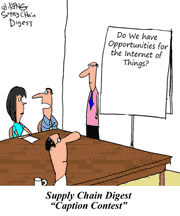
|
See Who Took Home the Prize!
|
|
|
|
|
|
Can - and Should - Western Manufacturing be Saved? ( Part 7)
"Can - and should - Western manufacturing be saved?" raises a rather significant set of questions.
This will now be the seventh column I have written in this multi-year series since 2009 - and perhaps the most negative one in the end, unfortunately.
As a quick note, The "and should" part of these titles came from some legitimate questions as to whether the US and other Western economies were simply headed down a "post manufacturing" economic path, with the ability to compete on a low cost world stage certainly in question. And with the added question of whether a future of low-skill, repetitive manufacturing work is really what is wanted. Maybe Western countries would be better off to just to dispense with the idea and move on.
GILMORE SAYS: |
"The US will once again break the record for the largest trade deficit in goods with China in 2015, surpassing the 2014 record of $343 billion, which in turn broke the 2013 record, etc."
WHAT DO YOU SAY?
Send us your
Feedback here
|
But last year, I wrote that "the "should" question has been answered, and it is certainly Yes - though what US manufacturing looks like in the future certainly won't be much like it has in the past."
I think that is still largely correct, but I am less optimistic lately about the "can" part of the question than I was last year.
Over the previous six columns I have covered a lot of ground. On the negative side, this included such issues as some questioning whether it was even possible anymore to build huge manufacturing operations in the US, and the city of Oakland needing to go to Chinese steel suppliers for a new bridge because no US producer could deliver what was needed.
On the positive side, I've also covered how extremely low natural gas costs have spurred some US resurgence in factory activity in sectors that need natural gas as feedstocks and/or as power sources (e.g., chemicals, metals, fertilizers), and also how rising wages in China and other factors were perhaps launching the trend of "reshoring" we anecdotally hear so much about. More on that in just a bit.
But a couple of stories in recent weeks relative to US manufacturing have shaken my still modestly optimistic perspective.
The first concerns US aluminum producer Alcoa, a sort of iconic American manufacturer known for years as being one of the first companies to release its earnings results each quarter, often setting the tone for that quarter's financial trends.
Well Alcoa led the earnings releases again a few weeks ago for Q3 - and the results were not good.
A slowdown in demand from China - but more importantly a flood of production from the country - have sent aluminum prices sharply down, to six year lows, hammering the bottom line of Alcoa. But more substantially, Alcoa announced it was closing about one third of its domestic operating capacity. That is a huge percentage.
The analysts at Harbor Intelligence, who follow the aluminum market, further said that if aluminum prices don't recover, almost all US smelting plants will close by the end of 2016.
Can you imagine that 127-year old Alcoa, one of the United State's great companies, could possibly close down all US production in not much more than just a year?
Silly me, I thought Alcoa was still a major global producer of aluminum - but it is simply not. Take a look at the chart below, from Bloomberg Business, showing US aluminum production - largely Alcoa - compared to Chinese output. I had no idea how irrelevant US production had become.
|
|
In fact, the 503,000 metric tons of smelting capacity Alcoa is shutting down accounts for about 31% of the US total for primary aluminum, but represents less than 1% of the total global capacity - something of a rounding error on the global stage.
The continued price declines in aluminum - due to overcapacity led by China - is "rendering American operations unprofitable and accelerating the pace of the industry's demise,” Bloomberg notes. Wow.
Story two: American Apparel is a retailer with several hundred stores selling its own privately branded clothing line. It has been known in recent years for its racy advertising, being one of the first retailers to adopt item-level RFID tagging, a quirky former CEO - and still making its clothes in the Los Angeles area.
Alas, financial results have not been good, with the company seeing heavy losses in recent years.
A few weeks ago, it finally filed for Chapter 11 bankruptcy protection. After the filing, current CEO Paula Schneider said management had no plans to move manufacturing operations from Los Angeles to offshore locations. The restructuring that lies ahead, she said, will enable American Apparel to keep production in the US.
"That's what makes us a really important company and a company that needs to thrive and be saved," Schneider said.
American Apparel has several thousand production workers in the LA area. Most make about $12 an hour - not much anywhere but especially so in Southern California - and some are reporting wages have dropped to about $9 per hour as the financial troubles mounted.
It appears you can't keep making clothes in the US even at those wages. But get a load of some of the comments made to various news sources after the company's bankruptcy filing, such as these observations from Lloyd Greif, chief executive of investment banking firm Greif & Co.
"There is too much emphasis being placed in having things made in America," Greif told the Los Angeles Times. The company needs to move offshore, he said, "If they want to survive."
Greif is hardly the only one with such a view.
"This manufacturing model makes no sense," said Josh Arnold, an equities analyst and contributor to financial site Seeking Alpha. "It costs way too much money" for American Apparel to keep production in the US.
Others said perhaps American Apparel could keep making some clothes in the US if it moved production somewhere in the South, I guess where they could find workers for lower than $9 per hour.
Keep in mind most of the company's production is within the city of Los Angeles, where the minimum wage will be rising to $15 per hour over the next several years. Let me tell you right now, American Apparel will be heading offshore soon enough.
The unfortunate takeaways: Both Alcoa and American Apparel simply can't compete producing in the US with low cost global rivals. The iconic Alcoa may shutter its last US smelters in a year or so, and the consensus of many industry experts is that trying to make apparel in the US is simply an archaic notion today, at least until they invent robotic sewers (which is being worked on).
Now back to reshoring. The US manufacturing sector in total has been growing, but slowly. Output is up roughly 5% from the 2012 average, a compound growth of about a meager 1.5% per year. Some sectors such as automobile and truck production are doing very well; others such as apparel and furniture continue to lose ground. So the story is OK, not great, and very mixed here by sector.
But imports from China continue to pour in. The US will once again break the record for the largest trade deficit in goods with China in 2015, surpassing the 2014 record of $343 billion, which in turn broke the 2013 record, etc.
Through September, the US trade deficit in goods with China is $273 billion, compared with $252 billion at the same point in 2014. The trade deficit in goods with Mexico was $53 billion in 2014, by the way, a figure that will also be easily surpassed in 2015.
If there is any real reshoring going on, we must be pulling production back from somewhere besides China and Mexico. As a JC Penny supply chain exec said a few years ago (paraphrasing): "The move offshore was like a flood, and the reshoring is coming back in as a trickle.” The numbers are what the numbers are, whatever we may hope.
So I will be back again on this theme when we have better news. Boston Consulting Group is about due for another study showing the US as being highly competitive, so I will look for that. But "factory Asia,” as The Economist calls it, with a bit of "factory Mexico” added in, continues to look mighty strong to me.
Reshoring is not going to rally the US economy, despite some occasional examples of a few companies doing it.
What is your take on the Alcoa and American Apparel stories? Do you still hold out hope for reshoring? What can be done if anything to turn things around? Let us know your thoughts at the Feedback button below. |
|

|
|
|
|
|
New Videocast: |
Using Supply Chain Modeling to Improve Operations and Outperform the Competition
|
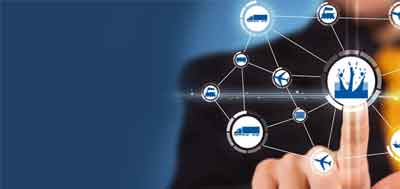 |
PriceSmart Builds Optimized, Aligned and Dynamic Supply Chain Network
You'll learn about key new trends in supply chain design, where companies are finding the value, and learn the powerful story of how leading retailer PriceSmart has used network design tools to craft its network of the future to support growth, optimize flow paths, and right size inventory levels.
Featuring Frank Diaz, senior vice president, distribution and logistics at PriceSmart, and Toby Brzoznowski executive vice president at LLamasoft and SCDigest's Dan Gilmore
|
|
Wednesday, December 2, 2015 |
|
On Demand Videocast: |
Making Supply Chain Business Intelligence Pay Off for Mid-Market Companies
|
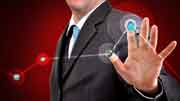 |
New Technology Options and BI Use Cases Delivering Competitive Advantage and ROI
Includes demystifying supply chain BI, the keys to deployment success, key trends such as the move beyond scorecards to dashboards, and how new BI offerings are enabling cost-effective, easier to implement BI solutions to mid-market and even many larger companies
Featuring Donna Fritz of TAKE Supply Chain,Tom Dadmun, former head of supply chain for high tech manufacturer Adtran and SCDigest's Dan Gilmore
|
 |
Available On Demand |
|
On-Demand Videocast: |
Innovations in Supply Chain Design
|
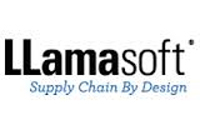 |
How Smart Companies are Finding New Ways to Reduce Costs and Improve Performance
Includes a Number of Real World Case Studies about how Leading Companies are Putting these new Applications to Work
Featuring Toby Brzoznowski, Exec Vice President at LLamasoft, Dr. Michael Watson, Partner Opex Analytics Lead Author, Supply Chain Network Design and Dan Gilmore, Editor, SCDigest
|
 |
Available On Demand |
|
|