As we enter the last real month of summer, some overall supply chain observations – admittedly coming in part from a beach somewhere on the east coast. My family thinks I am crazed.
I continue to be intrigued by the subject of supply chain flexibility. Hope you had a chance to see the full comments of my expert panel on the subject (see Our Guru Panel Weighs in on How to Define and Measure Supply Chain Flexibility) – collectively, they offer some excellent insight and perspective. Really worth the read.
Gilmore Says:
|
|
"Could it possibly be that WalMart's RFID strategy and the merchandising strategy are joined at the hip?"
What do you say? |
|
Send us
your Feedback here |
|
Yet, I don’t think our profession has anything close to a real definition of supply chain flexibility or how to measure it. Dr. Hau Lee of Stanford is certainly right when he says a key component in the definition and measure of flexibility must be time – “Flexibility one month out, versus flexibility three months out, are very different things,” he notes. But just how to use that truism isn’t clear.
Dr. David Simchi-Levi of MIT, in addition to having a very precise definition of manufacturing flexibility focused around how many different product lines each factory can make, also wisely notes that there are at least three areas that impact flexibility:
- System design, including the supply chain network
- Process design
- Product design, including modularity and postponement potential
The fact that Dr. Simchi-Levi’s three dimensions seem quite right shows the challenge of defining and measuring supply chain flexibility, as it encompasses at least these three and perhaps other components.
But if supply chain and business leaders want to achieve greater supply chain flexibility, I think we need something that gets us closer than where we seem to be now in terms of definition and measurement. As I a few weeks ago, we will do some work on this…
It is clear that executives value flexibility. A recent IBM study of global CEOs includes a whole section on “Building Operational Dexterity,” synonymous with flexibility or agility.
The study says that CEOs are looking to simplify processes as a key weapon to increase flexibility, primarily by reducing the time it takes their organizations to respond. However, the CEOs also recognize that a certain amount of complexity, especially in terms of supply chain interactivity, is a necessity. They hope to keep that complexity, however, “behind the curtain,” in terms of what a customer sees or experiences.
Interestingly, the CEOs most focused on operational dexterity were also those that were most focused on moving to even more variable cost structures, as shown in the figure below. (I must confess to being unclear about the CEOs who said they were pursuing both more fixed cost models and more variable costs models – maybe the strategies vary by business units).
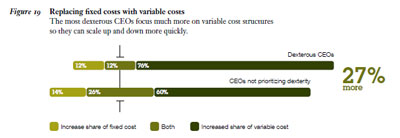
View Larger Image
Source: IBM CEO Study 2010
In general, achieving more variable cost structures implies today higher levels of outsourcing. Let the contract manufacturers and 3PLs invest in the assets, and strike deals that allow the company to flex volumes up and down with relatively little cost penalty. A great deal if you can get it.
Of course, corporate desire for more “variable costs” always comes after a recession, especially a deep one as we’ve suffered through, when almost every company wished it had lower fixed costs in the face of sharp decreases in demand and revenue. The accounting text books will show you, however, that in good times more profit is usually made from a higher percentage of fixed over variable cost, for the simple reason that “fixed costs” are just that, staying the same as revenues rise.
But the trend towards more outsourcing seems inevitable, meaning some things supply chains are doing in-house today will done by someone else tomorrow – but adding complexity and value to those who remain coordinating those ever more virtual supply chains. That’s the good news.
And at the risk of being redundant, if CEOs want more operational dexterity, as the IBM study tells us, given the truism that “what gets measured gets managed,” don’t we need a better way to track whether we are actually getting more flexible or not? Or is it just “gut feel”…
At times, when I talk to some companies or see presentations at various conferences, I despair that we are getting so good in our supply chains that there just won’t be much left to write about or discuss in the future. What some companies are doing out there today is simply impressive; just consider how amazingly far we have come in the past decade in terms of the practice and precision of supply chain management.
As just one example, I saw a presentation from a supply chain executive at Sara Lee this spring that detailed how they were using a comprehensive, integrated approach to operational metrics to drive performance that was stunning in its approach – and that left me wondering how a company could ever go off the rails with a feedback and control system such as that.
If we make the same level of progress in the next 10 years as we have in the past decade, we will have reached an incredible state of supply chain greatness.
And then… some recent supply chain challenges in the high tech industry give me hope I will still have something to say and add down the road.
I don’t know if you’ve noticed, but a global shortage of many basic electronics components has lead to a mini-crisis, with wireless network companies such as Ericsson, Nokia, Alcatel-Lucent and others reporting pretty significant hits to revenue in Q2 because they simply couldn’t deliver the goods to customers.
It’s pretty simple what happened – when the recession started in 2008, many Asian suppliers went out of business or greatly cut back capacity (stopped buying new equipment, etc.). Now the economy, especially in tech, bounces back, and suddenly there simply is not enough supply to go around.
Ironically, network giant Cisco, which almost a decade ago got caught with some $2 billion in excess inventory when it failed to react fast enough to the last recession, this time around is battling delivery and lead time issues from the component shortage that has its channel partners hopping mad. One large public reseller earlier in the year blamed its own revenue shortfall on Cisco’s inability to deliver.
Apparently, many could see the supply problems developing more than a year ago. Was it simply impossible for the OEMs to do anything about it? Or could better supply management , planning and response have avoided the problems for some of these high tech giants?
I am not sure, but what I do think is going to happen is that continued supply chain improvements are going to also mean leaner and leaner operations – making risk management a critical discipline and meaning we will see more and more supply chain disruptions for those who don’t get it right.
So I think we can still have lots to talk about for a few more years…
Amid the big news of WalMart restarting its RFID program, focusing on apparel and specifically men’s jeans and “basics” with an approach that seems quite sensible this time around (Will WalMart get RFID Right this Time?), I also caught this bit of news.
WalMart just ousted the head of its US apparel business, among other recent changes related to disappointing results in apparel.
The Wall Street Journal reported last week that WalMart “last month said that it was going to focus more on basics like underwear, socks, T-shirts and jeans.”
Could it possibly be that the RFID strategy and the merchandising strategy are joined at the hip, with the goal of turbo charging profits in jeans and basics in part by making sure inventories are just right?
We really are making supply chain progress.
Any reaction to Gilmore’s supply chain thoughts from the beach? Let us know your thoughts at the Feedback button below.
Web Page/Printable Version of Column
|