Things really do come in threes, don't they?
Over the past month or so, I have been involved in three separate conversations relative to the inter-related topics of inventory, cash flow, working capital, etc. . One was with with a 3PL provider, one with a manufacturer, and most recently with a software provider.
Gilmore Says: |
Gerry Marsh has convinced me with his proprietary models that reducing inventory and improving cash flows has an positive impact on a company's valuation or stock price beyond just the impact lower inventory carrying costs will have on profits/earnings per share.
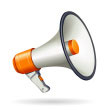
Click Here to See
Reader Feedback
|
These led me to two observations. First, even though most of us are today about generally aware of these supply chain finance matters than we were say 10 years ago, I would say most supply chain professionals are only modestly knowledgeable at best in terms of the details. Second, even for someone like me that follows this stuff for a living, and who considers himself pretty good (for an amateur) on the financial side of the business, if you don't keep at it you have to sort of re-teach yourself the stuff time and time again to keep it straight.
So I am going to make an attempt here, I hope for the benefit of many. I have tackled this topic before, but not quite in this way.
We're going to start with working capital. Part of the confusion is that the term sounds like it is a good thing - I'd like to have a little more "working capital." But it isn't. Working capital is basically the amount of cash a company has tied up just running the business. The more that is tied up, the less cash is available to do something else with, or the more a company has to borrow to fund its operations.
There are various definitions, but current assets (inventory, accounts receivable) minus current liabilities (accounts payable) is the standard one. So, if you shrink the former by reducing inventory and/or reducing the time it takes to collect money from customers, or increase the latter (accounts payable) by stretching out the time it takes to pay vendors, you will reduce the amount of the company's working capital, and that is a good thing. Dell for awhile famously had negative working capital, having little inventory that it owned (it used a lot of JIT and consignment inventory, and used a make-to-order model) and was paid by credit card customers faster than it paid its vendors.
While inventory levels are the most prominent way the supply chain can affect working capital, it impacts the other two main categories as well; that is, timing of payments to vendors (stretching them out is good for working capital if not exactly fair to suppliers) and having perfect orders to customers so that payment isn't delayed while working out the discrepancies.
But inventory is the main focus here, a key indicator of supply chain excellence, the area where supply meets demand. Where it gets confusing to most of us is that changes in inventory levels impact key financial statements differently.
Let's say a company holds on average $1 billion in inventory. Let's further state that through various initiatives, it is planning to reduce those inventories 10%, or $100 million.
What will happen on the three key corporate financial statements (the balance sheet, income statement, and cash flow statement)?
Inventory levels on the balance sheet would decline by $100 million.
Cash flow on the cash flow statement would also increase by $100 million - a dollar for dollar improvement. This would happen because working capital would be reduced by $100 million. The reduced inventory would move from being tied up in working capital turn into cash.
The trickier thing is what would happen on the income statement. Does having lower inventory improve profitability as well as improving cash flow?
Well, it certainly is assumed to do so for most companies when estimating the payback from various initiatives. For an easy and timely example, when calculating the benefits of low cost country sourcing, the lower unit price obtainable of course has to be balanced with extra costs for transportation, duties, etc., plus the costs of holding additional inventory due to the longer supply chain, more supply uncertainty, etc.
Now, what should that cost of inventory number be? And frankly, I will say that there is the theoretical number and then ultimately the actual number that will eventually show up (or not) on the real future income statement.
Do you know, as an aside, that in the annual state of logistics report from CSCMP (coming in two weeks, by the way), that a key driver of total US logistics costs is the cost of holding inventory - and that can vary significantly from year to year, based primarily on interest rates. In 2009, for example, coming from the 2010 report, inventory carrying costs were down a significant 14.1% from the previous year, partly from lower interest rates, partly from lower overall inventories. That inventory cost decline was an important part of the sharp drop in 2009 in the percent of GDP related to logistics costs.
There are actually several potential ways to calculate the cost of inventory relative to the income statement:
1. What is costs a company to borrow money: right now in the mid-single digits for most firms.
2. The company's "cost of capital": this gets a bit trickier (going into something called weighted average cost of capital, for example), and basically means the return shareholders expect from the company's use of capital. Varies from company to company, but let's say in general it ranges from 8-12%.
3. Inventory carrying costs: interest costs or cost of capital plus all the other costs associated with inventory (storage, handling, obsolescence, insurance, taxes, shrink, etc.). Here, there is huge variation in the numbers companies use. Dr. Stephen Timme of Georgia Tech and FinListics argues persuasively that most companies underestimate true inventory carrying costs (more on this soon). Inventory carrying costs can certainly range well into double digits for many companies. As a note, in the CSCMP state of logistics model, inventory carrying costs for 2009 were calculated at about 19%, but that included all warehouse/distribution costs. But we will use that percent here for this example.
So, back to our example: if the company was pondering moves that would reduce inventories by $100 million, the estimate of what the return from an income/earnings perspective would be is not the $100 million in improved cash flow that would be achieved but instead that $100 million times some number of the CFO's choosing, roughly picking a number from the three categories above. So, we might say $5 million on the low end, and as much as $19 million give or take on the high end (using a 19% inventory carrying cost). That's the estimate. Would those increased profit dollars really show up on the income statement? That is often the key question, in part because the cost of capital part of inventory carrying costs is not an income statement item.
Still, supply chain financial consultant Gerry Marsh of High-Tech Analyst Group told me this week that "As you correctly point out, this $19 million savings will never be seen in the income statement because only some portion of the carrying costs represent a reduction in operating expense (which goes through the income statement). The capital reduction benefit goes through the cash flow statement. Nevertheless, converting the capital reduction benefit of $100 million into an annual benefit by multiplying it by an annual cost of capital figure is not unreasonable."
I will make two other quick points. First, the $100 million in inventory reduction will also improve other ratios of key interest to investors, notably return on assets and return on invested capital. You divide profits by assets and/or capital, and since the denominator in either case is now lower by $100 million, the percentage will improve.
Second, as we have noted before, Gerry Marsh has convinced me with his proprietary models that reducing inventory and improving cash flows has an positive impact on a company's valuation or stock price beyond just the impact lower inventory carrying costs will have on profits/earnings per share. He has demonstrated how the difference in share price for two companies with otherwise similar earnings and growth numbers can be explained by differences in cash flow. See our supply chain graphic of the week for more on this (it's very good).
Another way to look at this same issue is the "economic profit" of a firm, which gets into the whole "economic value add"/EVA model and such, measuring how much capital is required to generate profits, and this comes out somewhat similar to Marsh's view in the end.
I summarize this made up case study in the small table below.
Impact of Reducing Inventory on Company Financials |
Financial Area |
Financial Statements Affected |
Impact |
Original Average Inventory Level |
Balance Sheet |
$1 billion |
Expected Reduction |
Balance Sheet |
$100 million (10%) |
Impact on Working Capital |
Balance Sheet, Cash Flow Statement |
Reduction of $100 million |
Impact on Cash Flow |
Cash Flow Statement |
Increase of $100 million |
Impact on Profits/Earnings: |
Income Statement |
|
Using Interest Cost Method (e.g., 5%) |
|
$ 5 million (reduction in interest expense) |
Using Cost of Capital Method (e.g. 9%) |
|
$5 million (reduction in interest expense), plus possible imputed value of an extra $4 million |
Using Inventory Carrying Cost Method (e.g., 19%) |
|
$15 million (interest expense plus operational cost savings) plus possible imputed value of an extra $4 million |
Hope this helped - and didn't put too many of you to sleep. Video on this next week.
Do you well understand these types of supply chain issues? Do most supply chain professionals understand them well? Is this kind of information useful? What would you change in whar we have presented? Let us know your thoughts at the Feedback button below.
|