|
|
About the Author |
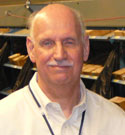 |
Cliff Holste is Supply Chain Digest's Material Handling Editor. With more than 30 years experience in designing and implementing material handling and order picking systems in distribution, Holste has worked with dozens of large and smaller companies to improve distribution performance. |
|
Logistics News
By Cliff Holste
September 16, 2015
|
|
Logistics News: DC Environment Exposes Seasonal Workers & Companies to Numerous Risk Factors
Improving Physical Conditions Key to Managing Workplace Safety
|
|
Holste Says: |
 |
Cross training, can help reduce workers' exposure to risk factors by limiting the amount of time workers spend on "problem jobs". |
|
What Do You Say?
|
|
|
|
Previous Columns by
Cliff Holste |
|
|
A busy distribution center can be an intimidating workplace environment especially during peak shipping periods. Even in the most up-to-date, efficient and mechanized DCs, there are still lots of tasks requiring manual labor. Companies typically double or triple their workforce for the last 100 days of the year. That adds up to a lot of inexperienced “hands-on-deck” and an elevated risk for accidents.
In addition to the obvious dangers associated with forklift trucks and pedestrian traffic, various studies have shown that the main risk factors with manual operations include the following:
|
Awkward postures - bending, twisting, grasping loads
|
|
Repetitive motions – frequent reaching, lifting, carrying
|
|
Forceful exertions – carrying or lifting heavy loads
|
|
Pressure points – leaning against parts or surfaces that are hard or have sharp edges
|
|
Static postures – maintaining fixed positions for a long period of time |
These are referred to as Muscular Skeletal Disorder (MSD) injuries and include damage to muscles, tendons, ligaments, nerves and blood vessels. In addition, poor environmental conditions such as extreme heat, cold, and noise may increase workers’ chances of developing other types of problems.
By law, employers are responsible for informing employees about OSHA regulations https://www.osha.gov , as well as various safety and health alerts. According to OSHA, employers must post health and safety program information in prominent workplace locations. But how many employees really look at those signs?
A true safety culture does not happen overnight; a successful transition to a safety centric workplace takes time. Companies can help smoothly enforce this transition move by consistently displaying safety reminders to supervisors and employees in unique, visually stimulating ways, across an array of digital screens.
The amount of training that companies can provide for temporary workers is limited. Yet, it is in the best interest of the both the company and the worker to pay close attention to DC environmental and ergonomic issues. Nobody should go home from the job with chronic pain and/or injury.
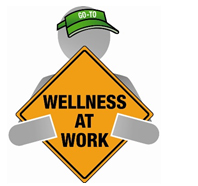
The law requires employers to provide their employees with working conditions that are free of known dangers. The Act created the Occupational Safety and Health Administration (OSHA), which sets and enforces protective workplace safety and health standards.
|
RMG Networks, a leader in intelligent visual communication, found that for $1 invested in safety communication, companies saw $6 saved. Plus 63% of people reported that digital signage catches their eye.
Types of Ergonomic Improvements
In general, there are (2) types of ergonomic improvements that can be made to “improve the fit” between the demands of work tasks and the workers’ capabilities to perform them:
Operational Improvements: – These include rearranging, modifying, redesigning, providing or replacing tools, equipment, workstations, packaging, parts, processes, or systems. The Materials Handling Industry of America www.mhia.org and the Material Handling Equipment Distributors Association www.mheda.org are comprised of many diverse and specialized manufacturers and engineering firms offering a large variety of solutions.
Industrial Engineering Improvements: – Here the focus is on observing how different workers perform the same task to get ideas for improving work practices or organizing the work, such as: |
|
|
• |
Alternate heavy tasks with light tasks |
• |
Provide variety in jobs to eliminate or reduce repetition (overuse of the same muscle groups) |
• |
Adjust work schedules, work pace, or work practices |
• |
Provide recovery time (multiple short rest breaks) |
• |
Modify work practices so that workers perform work within their power zone (above the knees, below the shoulders, and close to the body) and provide training on these techniques. |
• |
Rotate workers through jobs that use different muscles, body parts, or postures. |
Cross training, can help reduce workers’ exposure to risk factors by limiting the amount of time workers spend on “problem jobs”. However, these measures may still expose workers to risk factors that can lead to injuries. For these reasons, the most effective way to eliminate “problem jobs” is to change them. This can be done by putting into place the appropriate engineering improvements (mechanized and/or automated solutions) and modifying work practices accordingly. Companies should seek answers to questions such as:
|
• |
Why are workplace injuries occurring? |
• |
Which tasks are most likely to cause injuries? |
• |
What to do about problem jobs once you find them? |
• |
How to reduce workers’ exposure to injuries? |
One of the best ways to answer these questions is to be proactive in your problem solving. This simply means finding the problem first by looking thoroughly around the DC rather than waiting for problems to occur. Then improve the fit between the work and the worker by putting the appropriate changes into place. And be sure to do at least the following:
|
• |
Talk to various employees. Brainstorming with engineers, maintenance personnel, floor managers, supervisors, and production workers is a great way to generate ideas. |
• |
Contact others in your industry. Network at trade shows. Chances are good that your peers have already been down this path and have solutions that could also apply to your problems, saving you time, money, and effort. |
• |
Look through trade publications and equipment catalogs. Focus on solutions dealing with the types of problems/challenges you are trying to solve. Supply Chain Digest also provides an opportunity for you to “Ask a Question” on its website www.scdigest.com |
• |
Talk with industry experts and providers. They draw on experience from a variety of applications and will be able to share ideas that would never occur to you. |
• |
Consult with an expert in workplace ergonomics. An ergonomics specialist can “cut-to-the-chase” providing insights into available improvements, the cost, and the potential value. Unnecessary handling and duplication of material and product movement is expensive and a misuse of valuable resources. |
Final Thoughts
Making tasks less physically demanding and more efficient is the first step to higher productivity and lower operating cost. Peak shipping periods can and should be, opportunities to improve operations. With higher shipping volumes and increases labor, investments in order fulfillment and customer value added service will produce a better ROI.
|
|
|
|
Recent Feedback |
No Feedback on this article yet
|
|
|
|