|
|
About the Author |
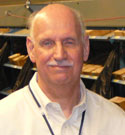 |
Cliff Holste is Supply Chain Digest's Material Handling Editor. With more than 30 years experience in designing and implementing material handling and order picking systems in distribution, Holste has worked with dozens of large and smaller companies to improve distribution performance. |
|
Logistics News
By Cliff Holste
June 11, 2014
|
|
Facility Design Factors To Consider When Expanding Operations
Getting the Building Structure Right is Dependent on Understanding Current and Future Fulfillment Requirements
|
|
Holste Says: |
 |
In addition to questions around size and throughput needs, companies also need to consider their potential requirements for or interest in materials handling systems (MHS) when building new or leasing existing buildings. |
|
What Do You Say?
|
|
|
|
Previous Columns by
Cliff Holste |
|
|
As the US economy continues to slowly improve most companies are seeing solid increases in unit volume sales and inventory that are putting the squeeze on existing facility space and design. In addition, many e-commerce retailers are adopting tactics to facilitate direct supplier-to-consumer transactions. Unable to transition from bulk to direct shipping in their current facilities, suppliers are strategically investing in industrial real estate to reduce their shipping times and operating expenses in order to remain competitive.
Retailers like Wal-Mart and Best Buy are adopting drop shipping and third party marketplace arrangements in order to connect customers with a wider array of products and suppliers. This closer cooperation has created a boom in industrial real estate, as suppliers and distributors realize the need for new facilities designed to meet intense fulfillment demands.
As we have reported before, sizing and designing a new facility is not an exact science. It is heavily dependent on the company’s ability to forecast where sales and unit/case volumes are going over the next 3-5 years.
In addition to questions around size and throughput needs, companies also need to consider their potential requirements for or interest in materials handling systems (MHS) when building new or leasing existing buildings. The designs of some facilities are simply more suited than others in terms of support for MHS inside them. Certainly, if a greenfield facility is being planned, companies need to think deeply about what types of equipment/automation may be deployed, and the resulting physical facility requirements (internal & external) before any final agreement with an architect or builder.
While it’s almost always possible to add at least some level of automation to an existing building (you can now even literally “raise the roof” of many DCs, solving the low clear height restriction that used to be a nearly absolute barrier to sortation systems in some buildings), certain building designs may be inherently less friendly to MHS, leading to limitations in system functionality, and/or higher operating costs.
This topic is especially pertinent right now, as leased floor space is generally available in most markets and therefore may look especially cheap (and quick) versus a build-to-suit facility, as those costs continue to increase. |
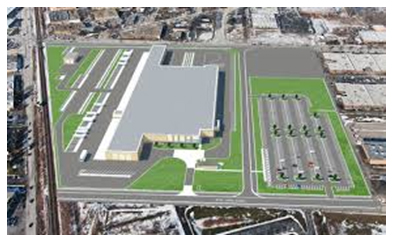
Form follows function is a principle associated with architecture and industrial design. The principle is that the shape of a building or object should be predicated upon its intended function or purpose. Therefore, a new facility project presents a unique opportunity to consider what the optimum DC operation would look like if building design was not a factor. In other words – take the time now to develop the “ideal” internal arrangement for your current and future business requirements and “wrap” the building around it. This approach will guide you to selecting the best facility option(s) for your business.
|
Below, are a number of key building design criteria that should be considered to optimize performance whether you are building or leasing an existing facility, considering MHS automation or not.
|
• |
Size: While size is an obvious factor, there are several considerations often overlooked when determining square footage requirements. The first is the opportunity to reduce total building costs by going up to increase cube, rather than out (see “Building Height” below). The second is that while MHS such as picking and automated carton sortation can deliver significant productivity gains, it also takes floor space that must be planned for when building or leasing a new facility. |
|
|
• |
Building Height: A traditional “spec” building will have a clear height of 24 to 26 feet, tall enough for 4-high pallet storage racking. However, as it is usually less expensive to build up rather than out, and maximizing storage capacity is an almost universal goal, the trend today for companies commissioning their own facility is to build with a clear height of 32 feet or even greater. At this height, 6-high pallet storage can be used, with some companies going even higher to achieve 8-level storage rack configurations. In most municipalities, fire safety codes have being written to permit ESFR (Early Suppression, Fast Response) ceiling mounted sprinkler systems to be installed in buildings of this height in place of in-rack fire sprinkler systems (yielding a considerable cost savings while increasing flexibility). |
|
|
• |
Floor Flatness: Standard warehouse floors will support normal fork truck movement and activity, but are generally used with conventional, wide-aisle storage configurations (12-foot aisle between racking). Standard floors may preclude use of narrow aisle (8-foot aisles) and are definitely not acceptable for very narrow aisle (5-6 foot aisle) technology, which require so-called “very flat” and “super flat” floor construction, respectively. While these floors are more expensive to install and can add weeks to the project schedule, the long-term gains in storage cube, operator productivity due to faster travel speed, and reduced truck maintenance are often worth the one-time initial building cost. To make this decision, an analysis is required to determine total storage requirements and the optimum rack configuration by comparing building cost, the cost of specialized lift truck equipment, pallet storage density, and expected worker productivity.
Note: It is possible to have existing floors improved to “super flat” levels, but obviously this is more expensive than building the floor that way to begin with. |
|
|
• |
Column Grid Pattern: The traditional 40-foot by 40-foot building column spacing is rarely optimum for an engineered DC. Roof support columns should always be located in the flue space in-between racks. However, with any of the narrow aisle approaches a standard grid will rarely allow the columns to be buried in the rack, resulting in a significant loss of storage positions. It is also frequently desirable to make the first bay extra deep to eliminate columns that impede fork truck traffic on the dock, by moving the first column row back to 60-70 feet away from the doors. |
|
|
• |
Roof Reinforcement: It is often possible to hang portions of a MHS from the ceiling rather than using floor supports. This can both provide for greater movement of vehicles and people around and through the system, as well as allow those portions of the system to occupy otherwise “dead space,” such as above a traffic aisle. However, the ability to hang conveyors and other equipment is generally dependent upon having defined sections of the building roof structure strategically reinforced during construction to take a greater load per square foot.
A “spec” building will almost never have reinforced roofing. An empty building previously occupied by another tenant may, but likely not consistent with your specific needs. More than you would think, even companies building new DCs don’t get this question answered early enough in the process. While roof reinforcement can usually be added later, it will be a lot more expensive to do so than at the time of construction. That should also be considered in the lease versus build decision. |
|
|
• |
Dock Doors: The typical warehouse building has receiving doors on one side of the building, and shipping doors across on the other side. While this flow-thru design is often the best configuration, it is sometimes better to look at other arrangements. For example, placing receiving and shipping doors on the same side of the building may allow both functions to share sortation equipment, using one set of diverts to sort received cartons for palletizing and put-away, and another to build outbound customer orders. Another advantage is that you can provide one common and secure space for both delivery and pickup drivers to congregate. While there is usually flexibility to add doors even to a spec building, the final arrangement of doors needs to be closely tied to the MHS layout, especially for fluid loading and unloading applications. |
|
|
• |
Lighting: Lighting should be placed so that it hangs directly above storage and pick aisles, which will rarely be the case if lighting is in place before the storage system has been designed and laid out. |
|
|
• |
Egress: Depending on the number of trucks and employees arriving and departing, assess to highways and parking space must be factored into the decision. |
Final Thoughts
Clearly, there are a number of factors that go into deciding whether to build or lease a DC, i.e., the optimal location including proximity to access roads, taxes, parking, future expansion capability and many other attributes. Compromises with fixed assists often have to be made. Therefore, make sure you have thought through the operational impacts of how the facility design will help or hinder current and future business requirements including the addition of higher levels of system automation. |
|
|
Recent Feedback |
No Feedback on this article yet
|
|
|
|
|
|
|