|
Featured Sponsor: Kinaxis |
|
|
 |
|
 |
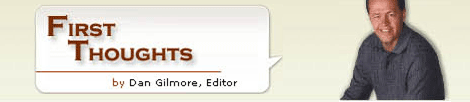 |
 |
FEATURED EVENTS |
 |
"MUST NOT MISS"
ON-DEMAND VIDEOCAST
WATCH IT NOW! |
How Multi-Modal Wireless
Technology is Driving New
Productivity Gains
in Distribution
|
Upcoming Videocast |
Thinking "Inside the Box":
Utilizing Packaging
Optimization to Achieve
a World-Class Supply Chain
August 11, 2009

|
|
NEWS BITES |
This Week's Supply Chain News Bites
Only from SCDigest
|
|
|
|
SCM STOCK REPORT |
It was a week for recovery on Wall Street as the second quarter earnings report brought better news than expected. Our Supply Chain and Logistics Stock Index responded well to the unforeseen good news.
In the software group, Descartes climbed 12.4% and is now up 11.8% over last year’s mark. In the hardware group, Intermec was up a whopping 14.2%, followed closely by Zebra (up 9.3%). In the transportation and logistics group, CSX took the lead (up 18.2%). Others within the group with double-digit gains: Prologis (+13.4%), Norfolk Southern (+12.9%), Union Pacific (+12.8%), Canadian National (+11.8%), and FedEx (+10.2%).
See Full Stock Report
|
|
|
ON TARGET e-MAGAZINE |
Each Week: |
RFID/AIDC Transportation Procurement/Sourcing Manufacturing Global Supply Chain Trends and Issues |
EXPERT INSIGHT |
Guest Column
by Steve Osburn, Kurt Salmon Associates
|
|
|
|
EXPERT INSIGHT |
Guest Column
by Kelly Thomas, i2 Technologies |
|
|
EXPERT INSIGHT |
Daily Jab
by Dan Gilmore, Editor, SCDigest |
|
|
THIS WEEK ON DISTRIBUTION DIGEST |

Holste's Blog:
Does Retrofitting Older DCs to Improve Performance Make Good Business Sense?
|
 |
Top Story: Card Check Appears Dead for Now, but Coming Back in Another Guise that May Lead to Same Result
|
 |
Supply Chain Video: Understanding Lean Thinking in Distribution
|
Visit Distribution Digest
|
|
|
SUPPLY CHAIN TRIVIA |
|
|
We're repeating last week's question, because we made a mistake, as several readers pointed out, misinterpreting a 200% increase as doubling, when it is actually tripling. |
|
Q. |
With all other things being equal (and they never are), but nonetheless, in a single tier distribution network, how many distribution centers does it take for the total inventory level in the network to double, versus having just a single DC, according to classic inventory management theory? |
|
|
A. |
Click to find the answer below |
|
|
|
|
|
|
|
The "New Normal" for Supply Chain, Part 2 |
A “new normal’ for supply chains – will there really be one?
We started asking that question last week, and included highlights of some fine thoughts from leading supply chain thinkers such as Dr. Tom Mentzer of the University of Tennessee, Dr. Jim Tompkins of Tompkins Associates, Bill Read of Accenture, and Rich Sherman of Gold & Domas. (You can read the full comments of Mentzer and Tompkins here: The New Supply Chain Normal: Supply Chain Gurus Weigh In.) Read and Sherman’s comments will be in On-Target next Tuesday.
So, let’s go back to the beginning for a second. I first heard the term “new normal” late last year in a financial context. Market pundits started talking about a “new normal” for the investment world following this “great recession.” The basic idea was that certain assumptions and results that this sector had generally relied on for a number of years were likely to be replaced with new ones. The severe downturn will have caused fundamental shifts in how the investment sphere operates.
The term has since turned up in all kinds of places. I just received an email this week from transportation industry analyst John Larkin at Stifel Nicholas for a webinar on the “new normal” for the railroad industry.
Gilmore Says:
|
|
"CEOs and CFOs will not soon forget this period, even as the economy recovers. Credit will never again be as easy as it was before the crash (or at least for many, many years), and executives will have learned powerful lessons on the value of a strong balance sheet."
What do you say? |
|
Send us
your Feedback here |
|
So, will we have a “new normal” for the supply chain, or will our world pretty much be the same once we get out of this thing?
Yes and No. How’s that for an answer?
All of our pundits last week emphasized that it’s hard to talk much about “normal” in the supply chain, since, for many years, supply chain has been characterized by rapid change and unpredictability. They are certainly right.
On the other hand, supply chain is, in the end, a means for companies to respond to business strategies and the needs and wants of customers – so, if there are important changes in those areas, there will, I think, clearly be some related changes in the supply chain.
I think the depth and breadth of any “new normal” will depend on how much longer the downturn lasts. There are a number of positive signs, but many worrisome ones still out there too. Jim Tompkins has been studying this for many months, and he is convinced economic “comeback” is on the horizon; he makes a convincing case, and I sure hope he is right.
The length and depth of this recession even now, in my opinion, has already made a lasting imprint on today’s consumers and businesses, but one that may fade relatively soon if we do start to pull out before the end of the year. If it goes on much longer than that, the psychological impact will be substantial. If you ever heard parents or grandparents talk about living through the Great Depression, you probably know what I mean.
All that said, I think, for at least a few years, there will indeed be a new “supply chain normal,” in the following ways:
- The consumer will be different: I don’t think there is any doubt that we will see a multi-year trend towards a more conservative and value-oriented consumer. I liked the term from the Harvard Business Review article I quoted last week: “discretionary thrift.”
This means a few things. Economic growth, or at least retail spending, will remain low by historic or at least recent recovery standards, meaning, in general, we will see a slower ramp in “units.” It will, in general, mean a lingering tough time for more “luxury goods,” and/or a need to package and price those products in a more “value-oriented” way. It means perceived “discount channels” should have a real edge for some time. Finally, it means demand planning, especially based on what we think we understand from history and experience, will be especially tricky and different.
- Promotions become even more important: Promotions have become ever more important in the supply chain mix, but this will now accelerate. A promotion/package that seems to offer a “great value” will often drive phenomenal sales with the new consumer mind set.
That means “promotion optimization” and close collaboration between market and the supply chain will be more important than ever.
- Cash will remain king: Just as with consumers, CEOs and CFOs will not soon forget this period, even as the economy recovers. Credit will never again be as easy as it was before the crash (or at least for many, many years), and executives will have learned powerful lessons on the value of a strong balance sheet. Cash may not stay king forever, but it will be “prince” at least for a long time.
This has all sorts of ramifications: companies will start to make more supply chain investments, but be conservative in doing so, and favor ones that require less cash outlay, such as “on-demand” software. There will be more (maybe better said - more persistent) attention paid to inventory levels. It also means that with very conservative inventory levels, the supply chain will have to be capable of sensing changes in demand and be able to respond if sales spike above expectations.
- Simplicity imperative will stick: As we’ve noted, the frequent attempts, rarely successful, to reduce SKU counts is actually starting to work in this environment (see Will Large Retailers Help Manufacturers Drive Out Supply Chain Complexity?) While we may see some swing back the other way, I believe this is another trend that will stay for quite awhile even after recovery. It will be a lot harder to get new SKUs into the system for quite a long time at most companies.
This will reduce supply chain complexity and, simultaneously, put greater emphasis on efficiency (as if we weren’t already highly focused there). But there will be a tilt, in combination with trading partners, on gaining real efficiencies around a smaller number of SKUs. This could also have implications, perhaps unfortunately, for some smaller suppliers, and retail and wholesale channels – though some may thrive by delivering more choices.
- Companies will shed assets even faster: As CEOs learned that cash is king, they also learned that owning supply chain assets and having high fixed costs in a slump is very costly – maybe even fatal.
We all hope this was a once-in-a-several-generation slump, but that won’t matter – companies that can will look to outsource more functions and especially assets (plants, DCs) to third parties. Note that just this week, Dell announced it was selling its US “remanufacturing” facility and operations to Genco, as just one of what will be many more examples.
This means, I’m afraid, that many will find themselves working for third parties rather than the company they have been with, and that many supply chains will find that they have to work extremely hard to justify why given functions should be kept in-house, especially if they involve physical assets.
The financial industry will stay relatively less attractive as a career destination, and more talent will go to “physical product” sectors: That, in my view, is a very positive development.
Beyond that, there are a lot of questions, such as:
- Will this experience put some breaks on globalization, or not?
- How heavy handed will the role of government regulation become?
- Will emerging markets continue to be the growth story, or will they take much longer to recover, as some believe?
- How dominant a role, and how fast, will China achieve coming out of all this (for example, the push to get rid of the dollar as the global reserved currency)?
Some may disagree, but I think looking back, we will say the supply chain world was different for awhile after this, or that it was an inflection point, even given all the change we always see.
A “new normal un-normal,” perhaps.
Do you think we will see any multi-year shifts in supply chain thinking and actions? Will changes in how corporate executives now see the world be a big driver of this? What would you add or take away from Gilmore’s list? Let us know your thoughts at the Feedback button below.
Let us know your thoughts.
Web Page/Printable Version of Column
|
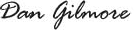 |
|
|
|
SCDIGEST RSS FEEDS |
Do you use an RSS reader? Do you
have a MyYahoo! or personalized Google page?
For
these and more you can have SCDigest delivered right
to your personal pages, all week long.
You can subscribe to our RSS feeds in two ways: |
- Copy our RSS link into your
RSS reader - it's easy! www.scdigest.com/rssfeeds.xml
- Click on a button below to
quickly add it to your favorite readers.
|
|
|
|
YOUR FEEDBACK |
We received some short, but very good letters on our Top Supply Chain Disasters of All Time article.
Our Feedback of the Week is from David Meyers from Tompkins Associates, who became involved later after the Toys R Us Christmas 1999 meltdown, and shares what he saw as some of the real issues.
Paul Gooch of The Logical Group brought up a candidate we might have missed at grocer Sainsbury’s in the UK (and Dan Gilmore says he’s right), while Chris McEliece of Lindblad Expeditions provides a link to the story we were looking for about a boatload of automobiles that had to be destroyed – turns out they were Mazda, and there is a link to the very interesting story on that one.
You will find those, plus a couple of other interesting letters below.
Feedback of the Week – On Top SCM Disasters of All Time:
I am having fond memories of Toys R Us.com Christmas 1999, which we later helped them turn around.
Here were the problems we found when we arrived there:
- There was a lack of surge capacity in the Memphis DC (physically, operationally, and through the material handling system (conveyor and sortation));
- Communication between the WMS and the MHE was neither stable nor robust - requiring frequent reboots, reloads, and exception handling;
- The processing of orders required intricate verbal/radio communication among departmental leads (on a wave-by-wave basis) throughout the DC – exceptions in one link (replenishment, picking, packing, etc.) required excessive research, resolution, and time for the downstream processing areas to recover; and
- The solution required a physical retrofit of the Memphis DC (storage, processing areas, pick modules, conveyor, sortation) including an upgrade to the WMS, a new WCS, and the integration of those systems to accommodate exceptions, surge conditions, and multiple “active” waves in the system at the same time, which provided flexibility on top of the surge capacity.
David Meyers, CSCP
Principal
Tompkins Associates
More On Top SCM Disasters of All Time:
In 2004, Sainsbury's, the UK supermarket group, blamed Accenture for the disastrous state of a new logistics system. It had to recruit 3,000 shelf stackers to fix the damage manually.
The new system was unable to track stock properly and Sainsbury's took a £550m charge to its profits. Writing off IT assets which were useless cost the supermarket £140m, writing off the cost of automated equipment in its distribution centres added another £120m. The failed systems also cost Sainsbury's £30m in stock lost or damaged by the new system. The brand suffered significant damage.
Paul Gooch
The Logical Group
Note from Editor:
I had heard about this one, but forgot about it, and it didn’t turn up in our research. There was a similar type of WMS disaster in the early 2000s at Kmart, as I now recall. May add them to the list next time we do this.
Thanks.
Dan Gilmore
I remember hearing about Frito Lay changing the supplier of the corn for the Frito's corn chips in an effort to reduce costs. Lower quality resulted in lower sales, which persisted for years. Not sure if they ever recovered, but they did switch back once the impact was realized. The story I heard had a pretty low-level manager making the change that nearly tanked the brand.
Brian Coats
Inventory Manager
Carrier Global Operations Group
I’ll bet some readers winced when this article reminded them of these events. A good follow-up article would be to summarize the lessons learned. I had direct involvement in the aftermath of one of the projects on the list to help determine what was needed to fix the problems. Ultimately, everything worked, and it has served the company well for many years. The lesson learned was SIMPLIFY!
I can think of 5 other projects that could have been candidates for the list. In four of them, the lesson learned was “When your technology vendor can’t show you that they have ever done anything like this before, PAY ATTENTION!" In the fifth case, the lesson was “When you insist on having at least one of every material handling technology known to man in your operation, DON’T!"
Fred Kimball, Principal
Distribution Design, Inc.
You mentioned that you wanted info on the MV COUGAR ACE incident, and the subsequent destruction of about 4700 brand new Mazdas. I’m not sure this falls into the same category as the other “disasters” on your list, but it was certainly costly (including a human fatality).
My understanding is that Mazda could have salvaged those vehicles, but, for fear of never-ending warranty issues, they were destroyed (as you can see from the picture, many of these cars spent some time on their sides). It took 2 years to destroy all of the vehicles, and the VINs are all listed at Mazda’s website.
http://en.wikipedia.org/wiki/Cougar_Ace
Chris McEliece
Purchasing Manager
Lindblad Expeditions
|
|
SUPPLY CHAIN TRIVIA |
Q. |
With all other things being equal (and they never are), but nonetheless, in a single tier distribution network, how many distribution centers does it take for the total inventory level in the network to double, versus having just a single DC, according to classic inventory management theory? |
A. |
4 - the formula, actually, is Inventory in All DCs = Inventory in One DC, divided by the square root of the number of DCs in the tier. At 4, inventory is doubled over that held in a single DC. At 9, it triples.
|
|
|
Copyrights © SupplyChainDigestTM 2003-2009. All Rights Reserved.
SupplyChainDigest
PO Box 714
Springboro, Ohio 45066 |
|
|
|