SCDigest Editorial Staff
Gilmore Says: |
While some of the things Apple is doing add extra costs to the physical logistics process, I suspect that they can also reduce total returns management costs. The process was so fast and simple that I bet it dramatically reduces support phone calls, disputes over product damage in the shipping process, returns being sent to the wrong address, etc.
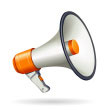
Click Here to See Reader Feedback |
Can improved reverse logistics processes deliver to the bottom line as well as to customer satisfaction levels?
That’s the question we have after a recent experience returning a defective iPod to Apple. This was the second iPod SCDigest editor Dan Gilmore has had to return for service over the past few years, and the process keeps getting better.
The process started with entering data about the problem (battery failure) on an Apple web site, along with the unit’s series number. Within about 12 hours, an email was received saying the product was still under warranty and approving the return.
Within 2 days, Apple delivered via express parcel service a box for shipping the product back to one of its service centers.
Inside the box were simple and very easy to understand instructions, which included tearing off the outer label on the top of the box. That label had all the information the customer needed to track the repair/return processes. Underneath and attached to the box was the shipping label for sending the product back.
Also inside the box was foam packaging. Taking the top piece off revealed a rectangular space for the iPod, with some adjustable pieces that could be removed, depending on the specific size/model of iPod, to achieve the most secure fit.
The iPod was then placed inside and the box closed, with Apple even providing a few strips of packaging tape to seal the box – a nice touch. That was it – the label of course contained the RMA number and all the other information Apple needed to track the return when it was received.
There was a little worry because the carrier was DHL, which is in the process of winding down its US parcel operations, but one call to the central DHL number and a driver was there to pick up the package in just a few hours.
We are also providing a video overview of the key elements of the packaging and process, which can be viewed here: Supply Chain Video: Reviewing Apple's Approach to Reverse Logistics
(Distribution and Materials Handling Article - Continued Below)
|