Total Landed Cost Framework
While it may be tempting to think developing and using a landed cost model would not be that difficult, to do it well actually takes considerable effort and technology support. Thomchick noted the following barriers
- The data needed to populate a model is often not readily available
- Execution pressures and time-constraints often preclude sufficient analysis of the data
- Companies often do not continuously monitor and update the landed cost inputs
- Organizational structures inhibit the cross-functional effort needed to build and maintain a landed cost model
The companies in the Penn State research project were all large, with five of the six being at least $10 billion in sales, and the other between $1-10 billion in revenues. The six participants represented companies in the metals, industrial, chemical, high tech and pharmaceutical industries, giving a nice mix of verticals but missing a retail participant, which would seem like the next natural addition to the mix.
The Penn State research led to the following six-category model, with some (not all) of the key elements listed for each:
Purchase Price:
- Price paid to seller
- INCOTERMS
- Payment terms
- Exchange rates over time
Transportation and Logistics:
- Foreign inland
- Line haul
- U.S. inland
- Accessorials
- Insurance
- Packaging
Customs and Imports:
- HTUSA (tariff) rate
- Merchandise processing
- Harbor maintenance fee
- Broker fee
- Less: Duty Drawback
Inventory Costs
- Cycle stock
- Safety stock
- Inventory in-transit
Inventory costs can vary depending on the INCOTERMS in category 1 (when does ownership of the inventory change) and the way a company values its inventory.
Overhead and Administration:
- Sourcing staff
- Due diligence
- Relationship building/travel
- Learning curve
Risk and Compliance
- Compliance costs (technology, staff, other)
- C-TPAT program costs
- Insurance costs
- Cost of potential risk of supply disruption
- Cost of potential risk of damage to reputation Health, Safety, Environment
The cost elements in each of these six categories are presented at a high level. Considerable more line items and detail would go into a fully operational model.
No Company Used All Six Cost Categories
Perhaps surprisingly, of the six large company research participants, not one was fully using costs from all six categories, though one was close.
In addition, Thomchick said none of the participating companies was really doing a good job at taking actual fully loaded landed costs and comparing them to what they had calculated. Among the barriers – the cost components are actually in multiple, perhaps even dozens, or buckets in internal accounting systems, making roll-up of these numbers a huge challenge.
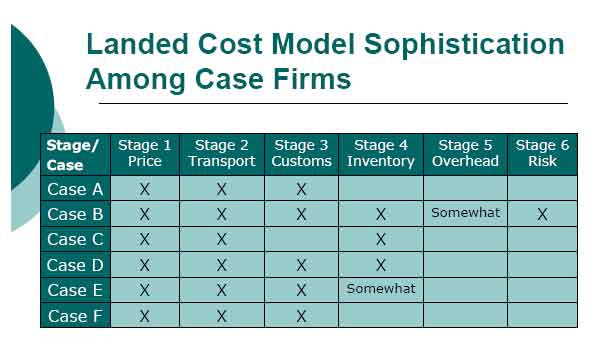
Source: Evelyn Thomchick, Penn State
Still Relatively Little Technology Support
Supply Chain Digest recently conducted some additional research on this topic, surveying nearly 100 shippers on various logistics practices, including total landed cost calculation. (To Download our Leading Edge Logistics White Paper, Click Here)
As can be seen from the chart nearby, Fourteen percent (14%) of our survey respondents said they performed little or no total landed cost management. SCDigest contacted a few of these respondents to better understand what was meant, and in most cases it appears to indicate that a company uses very static, pre-built costs that are incomplete and not in tune with the dynamics of each order.
Forty-six percent (46%) were calculating total landed costs internally using Excel or similar low automation tools, while 20% were using a commercially developed total landed cost calculator of one kind or another. A number of supply chain software providers now offer total landed cost calculation “engines.” GM, for example, is in the process of rolling out a TLC engine across its vast global supply chain.
Another 20% of companies said had developed their own total landed cost engine.
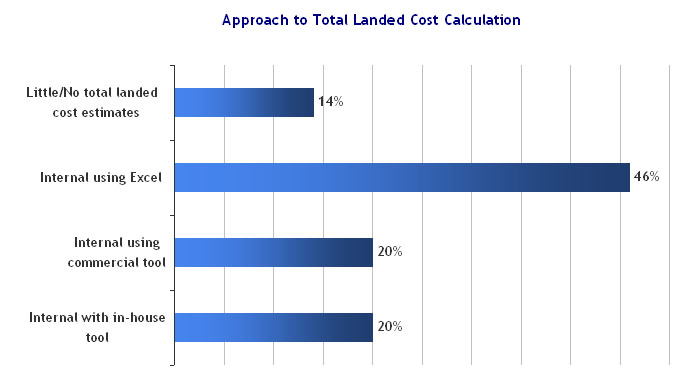
Source: SCDigest Leading Edge Logistics White Paper
For most companies, there is a significant gain to be had from better understanding total landed costs, in terms of better decision-making on sourcing, carriers, pricing and a variety of other supply chain components.
Clearly, total landed cost management is a ripe area for process and technology improvements.
How well do you think most companies do at calculating total landed costs? What are the cost categories most often left out? What are the keys to getting it right? Let us know your thoughts at the Feedback button below.
|