SCDigest Editorial Staff
The following article first appeared in our Supply Chain Digest Letter on WMS. The full issue of that Letter, as well as a wealth of other information, can be found at our WMS resource page: Warehouse Management System (WMS) Resource Page.
SCDigest Says: |
Perhaps the most important job of the executive champion of the WMS project is to ensure the right level of internal staffing and to monitor that those resources are being utilized as planned. Dedicating full-time resources is good practice.
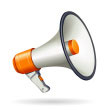
Click Here to See Reader Feedback |
Warehouse Management Systems are among the most challenging business applications to implement, for two reasons.
1. There are simply a lot of “moving parts” in a WMS deployment: perhaps hundreds of new users, data collections sub-systems, Radio Frequency or Voice Recognition sub-systems, material handling integration, new warehouse layouts, etc.
2. Unlike many software systems, WMS requires the synchronization of the “logical” world of the software with the very real physical world of the distribution center. Other systems that have related requirements, such as manufacturing software, generally don’t have as dynamic an environment to manage – material flows in a relatively static and predictable manner.
Not so in a distribution center, where material movement is dynamic and often unpredictable, and real-time accuracy is essential for effective operations.
“Matching the logical world of the WMS and the physical world of the DC is the number one challenge of the WMS designer, and also for implementation of the WMS itself,” says Mark Fralick, SCDigest Contributing Editor with experience in dozens of WMS deployments.
Despite these inherent challenges, many WMS implementations go quite well, while others flounder for months before getting right. Below is our quick guide for improved WMS implementations, several of which are not commonly discussed.
Pick the Right Time of Year
It may seem obvious, but we still hear of implementations that are done at very busy times of the year. This is usually driven by some other need – a new facility going live, or an ERP system deployment that has to be installed first.
If there really are no options but to deploy in a high volume period, you will have to live through it, but this really should be avoided if at all possible. A related issue: even when scheduling deployment in an off time, inadequate time is left before a peak period hits, so that the implementation is still in its rocky phase when the volume ramps. If you can possibly manage it, leave plenty of time.
(Distribution and Materials Handling Article - Continued Below) |