I was down in Orlando again this week for the WERC (Warehouse Education and Research Council) annual conference, and as usual it was a good event.
WERC is always an interesting conference for me. It is larger than a boutique event, with some 850 attendees - but not so large it loses its characteristic low key, relaxed feel. Many WERC members are very dedicated to the organization.
CEO Mike Mikitka and his team added some new wrinkles this year, including new tracks around retail and healthcare, and my observation was that there was solid attendance for sessions in both tracks.
Gilmore Says: |
A year or so in, there are now 11 disabled workers at that Kroger DC, out of almost 1000 total employees, but the goal is to get to 100, and Martz believes it can be done.
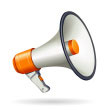
Click Here to See
Reader Feedback
|
With that intro, I attended 7 breakout sessions over my two days thee. All told very good - two top 10 presentations of the year candidates, four very good presentations, one that started out strong but in the end didn't really deliver what I was hoping for. All told, that's a pretty good batting average.
So let's get right to my two favorites.
Sven Verstrepen is from consulting firm Tri-Vizor, a spin out coming from some research performed at the University of Antwerp in Belgium that focused on so-called " horizontal collaboration." What does that mean? As contrasted with vertical collaboration between trading partners such as suppliers or customers, horizontal collaboration involves arrangements with peer companies - sometimes even a company's own competitors.
More specifically, it really focuses on logistics collaboration, sharing warehouse and especially transportation resources across two or more shippers.
I am of course familiar with this trend, but according to Verstepen it's really starting to gain critical mass right now in Europe. While transportation cost saving are of course a major driver here, it seems as if reducing CO2 emissions is nearly as big a factor. In one example cited, there wasn't any real cost advantage, but the collaboration went ahead based on sustainability factors alone.
There are six or seven forms of this horizontal collaboration. One you could call "co-mingled freight." Real example is an auto parts producer making heavy metal products, and a plastics manufacturer making products often filled with air. So course the parts maker would weigh out and the plastics maker would cube out a trailer. Located almost across the street from each other and shipping to some similar destinations, as you probably suspect the two companies wound up shipping combined loads with some metal products and some plastic.
How exactly this can generate a savings I am not quite sure, but the claim is transport costs were reduced 10%.
Then there is simple round trip creation - not common today but certainly not unheard of either here in the US - where companies find a partner basically moving freight in directly opposite patterns on some lanes. Vertstrepen said the approach being explored and in a growing number of cases happening between shippers in Europe.
Then there is "modal shift" and a handful of other types. There was a lot more here than I can fit - I plan to cover this in more detail soon.
A few other points: the arrangements have been blessed and now encouraged by EU regulators. There is a clear network effect - the more companies and lanes in an analysis, the more and better opportunities can be found. To make this work, a new type of 3PL is required - some company that can coordinate across multiple shippers, provide visibility, and accurately allocate the now lowered costs to all participants. Verstrepen said some are calling these new firms "5PLs." All very interesting - this could represent huge potential impact on the practice of logistics.
Saw another very good presentation on omni-channel fulfillment from consultant Holden Bale of Kurt Salmon and Josh Mayer of Belk department stores. I am sometimes hard on consultants for flying way too high in these kinds of presentations, but that was far from the case with KSA's Bale, who clearly knows what he is talking about and who offered high levels of detail. Mayer was pretty good too.
Bale said that nothing was really more important to most retailers right now than developing in-store fulfillment capabilities. Why? Because for many it will lead to an immediate jump in revenue, primarily through being able to sell products that are out of stock in an ecommerce DC. Mayer noted that when Belk's analysis showed a meaningful bump to the top line from such a move, then the orders from the top were to get this done yesterday, which presented its own set of challenges.
Bale noted ship from store can help move items at near full price that won't sell at all in the store they are in and avoids a liquidation path, and that this capability also sets the stage for other offerings, such as "click and collect."
Both speakers emphasized that you really have to understand what the drivers are in building store fulfillment capabilities. Is it to reduce costs and improve margins? Improve service to customers? Goose the top line? The answer to that question should drive what your omni-channel fulfillment network looks like - including stores - and will dictate the logic that is developed in say the distributed order management system as to where product should be sourced from.
Ok, totally changing direction, on Tuesday I attended an interesting presentation from several panelists on developing programs to hire disabled workers for distribution centers. As you may know, this type of program really started in 2006, by Walgreen's and then VP of logistics Randy Lewis. Unbelievably, Walgreen's now has one DC in CT with more than 50% disabled workers, including -get this - 40 deaf fork truck drivers.
But despite Walgreen's success, progress has been slow, with Lowes, Starbucks, Toy R US and now Kroger joining the list of companies pursuing this strategy - and at Kroger is starting in just one DC in Cleveland, TN, according to HR manager Stan Martz, who has been leading the charge there.
A year or so in, there are now 11 disabled workers at that Kroger DC, out of almost 1000 total employees, but the goal is to get to 100, and Martz believes it can be done. They lost a couple of workers along the way, and that includes for performance-based reasons. I was modestly surprised to learn that none of the companies mentioned pursuing these programs lowers their standards for disabled workers, and while there is usually a lot of prescreening and testing and then coaching once the worker starts, in some cases they just can't reach the minimum standard and have to be let go.
Martz offered some lessons learned. Coaching of the new disabled workers, especially in the first two weeks, is critical, as is training of supervisors, who are generally very unsure how to approach these workers, and in Kroger's case, once they accepted them, were then very reluctant to report them if they had low productivity levels.
"This is the right thing to do," Martz said. I agree - more companies should being headed down this path, often in the end for their own benefit, not just do gooding - these workers stay longer and call off less frequently.
Also on a lower tech subject, Pat Sheridan of Pepsico gave a very interesting presentation on a new driver safety training program that company has developed and that is having big results.
You have to start with the facts, Sheridan said: who is causing most of your accidents (usually new drivers and repeat offenders) and understanding what characterizes your most serious accidents are examples of how the data can focus a program's structure.
As part of its program, Pepsico developed 10 simple behaviors its drivers need to follow. One for example is to wait 5 seconds after a light at an intersection turns green before starting to go - obviously, this helps to avoid collisions with drivers moving through the intersection late after the light has turned red. And this points indicates Pepsi's goal is in part is to reduce accidents that others may deem unpreventable or not the company's driver's fault.
So when there is an accident, it is assessed by whether the Pepsi driver failed to follow one or more of these 10 rules. There are multiple training videos with the program, in-cab driver observations and more. It's working - Sheridan said claims paid by Pepsi co are down 50% in 2015, representing about $8 million worldwide.
I am out of space. There was a packed session on the new age robot Baxter. My take: there are trade-offs (speed for safety) and there isn't yet a "killer app" in distribution. But we are early in this game.
Any reaction to the issues or insight from WERC 2015 coverage? Let us know your thoughts at the Feedback button or section below.
|