Gilmore Says: |
“Voice picking” isn’t at all new, but after a number of years of relatively slow growth, voice has rapidly gone mainstream.
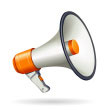
Click Here to See Reader Feedback |
Order picking is, of course, at the heart of distribution center operations.
What’s interesting is that, in many respects, our basic thinking and supporting technology options for order picking have remained fairly static for a long while. We’ve had the basics of advanced warehouse management system (WMS) support, use of radio frequency (RF) technology to enable paperless picking, and (where volumes and other conditions warrant) the use of physical automation such as pick-to-belt and downstream sortation (or related approaches such as use of tilt tray sorters) in place for almost 20 years now.
I have a friend who does a lot of conference presentations, and when I see him at an event he often jokes about giving “the same old order picking presentation” he’s been delivering for a decade or so. We need some new approaches, it seems to me. And there are some things brewing.
A month ago, we released our Supply Chain Digest Letter on advanced order picking systems, which many thousands of you received in the mail and others downloaded. You can access a copy of the 16-page Letter, which includes an excellent comparison table of picking technologies across a number of attributes, as well as many other resources here: Order Picking Resources.
Based on that work, here are a few of my thoughts:
- “Voice picking” isn’t at all new, but after a number of years of relatively slow growth, voice has rapidly gone mainstream. While the technology has been around since the mid-1990s, it just couldn’t seem to gain much critical mass for awhile before exploding over the last 3-4 years. Part of the reason the technology took some time to take off was that most WMS suppliers, and a good part of the consultants in the WMS ecosystem, were simply slow to really embrace voice. In fact, for just about every one of the WMS vendors, prospects and customers really forced them to add voice support, rather than the WMS vendors recognizing the many advantages of the technology on their own.
The good news is that now that support is largely there as standard WMS functionality, and the voice terminals can be “direct connected” to the WMS picking system. In the past, most voice deployments were interfaced, and required a separate software sub-system to drive the voice terminals. In many cases, that simply isn’t required today, though it still may be if you want to add voice to an older or legacy WMS environment (not a big deal, just not as clean as direct connect).
But regardless, the sheer number of proof points today and the clear advantages of voice in many environments has made it something almost every distribution operation should be taking a look at. What will be interesting to see is how well voice is able to penetrate applications in the DC outside of the picking area where most of the deployments are.
- I think there is really something to this “multi-modal” concept in terms of order picking technologies. Multi-modal basically means operators might use a combination of technologies (voice, RFID, RF) in support of a picking application.
I’ve always said that one clear opportunity to drive value from RFID in distribution was to help automate case picking, and that’s the same view I have of multi-modal. Several vendors are now working on systems that combine voice direction with an RFID reader that can sense cartons being placed onto a pallet. So, an order picker receives direction for the next picking location and quantity via voice, then places cartons on a pallet jack or other equipment without the usual need to confirm the picks via voice. The RFID reader validates that the right cartons and quantities are being placed on the pick pallet, and the operator hears a signal or voice warning if there are any errors.
We’re not quite there yet, but I do believe this type of approach is where we are headed.
- There actually are a number of interesting developments happening in the area of physical automation of case picking (meaning some type of automation device to pick cases) – sort of a holy grail in terms of DC automation. I can say at least one large soft drink company is looking very hard at the technology. More on this soon in SCDigest.
- There are some interesting things happening in the area of sortation and automation systems that impact order picking too. Several vendors (e.g., Invar Systems) have developed “warehouse control systems” that not only manage the automation but reach back into the picking operation to optimize the flow of picks and products to feed that automation. The goal: increased equipment utilization. In some of the cases I have looked at, the impact can be significant.
- Slotting is a key driver of order picking efficiency. More and more companies are taking the almost always beneficial step of proactively and consistently doing SKU and volume profiling analyses, and using that to drive slotting, storage media, and DC layout decisions. There’s nothing new there, but I’ve seen a definite uptick in companies doing this exercise on a more frequent/proactive basis.
Often, that profiling is being done manually. But I am also seeing renewed interest in slotting optimization tools to help do the job. In the past, these tools have had the reputation of being too hard for many companies to use, but I am just back this week from the Manhattan Associates User Conference, where I heard representatives from a diverse array of companies (pharma wholesaler McKesson, purse and accessory company Vera Bradley, O’Reilly Auto Parts, etc.) discuss very positive results from their slotting optimization deployments.
Among several interesting observations from that group, I liked this one from McKesson: they track the level of “emergency replenishments” as a percent of total replenishments, with emergency being defined as where a replenishment is needed to meet current picking requirements on the floor. Prior to implementation of the slotting tool, emergency replenishments in some DCs was as high as 20% of the total. After slotting, that figure dropped to the low single digits.
I have many more thoughts, but that’s my order picking update. You’ll find more on the Order Picking Resources page. But the bottom line is that after a long period of not much new, we’re seeing some innovation again. And that’s a good thing as distribution costs continue to accelerate, largely driven by order picking expense.
Do you agree it’s about time we have some new innovation in order picking strategies and technologies? What are you seeing out there? What’s your reaction to our list of developments? Let us know your thoughts at the Feedback button below.
|