1. Operators are paid for three to four TIMES more hours than actual material movement time. Across multiple industries, upon initial installation, VMS data reveals a very similar and startling pattern of vehicle operation.
Typical Shift Pay 8 hours
Operator Logged in to Truck 4 hours
Truck In Motion 2 hours
Truck Moving with a Load 1 hour
One hour of product moved for every 8 hours paid!
This data has been collected from over 35,000 VMS vehicle installations. Of course, some operators are more productive than others, but a VMS provides operational visibility and productivity metrics that are not achievable in any other way. Once this type of pattern is identified, it’s easy to take action and increase productivity on the floor.
Click here to learn more about addressing lost productivity.
2. Every day you are asked to do more with less. When you walk around your facility, do you see idle and empty trucks? Yet, at the same time, are there also requests to acquire more trucks and offer more overtime? Why does this happen? Without data to assign trucks to changing workloads, it’s almost impossible to reassign vehicles to meet needs of specific areas either temporarily or permanently, without disrupting operations. A VMS can identify the needs of the operation and – based on data – give visibility to a different use of resources.
Vehicle Management Systems provide unique insight into fleet operation by evaluating how your current vehicles are being used and if there any opportunities to better allocate them. The simultaneous usage chart below identifies the use of a fleet by each area of a facility. It shows utilization, including peaks and valleys so that operations can be better balanced over time. Why buy or rent vehicles to meet perceived peak needs when data can provide real metrics to evaluate this decision?
Simultaneous Usage Report
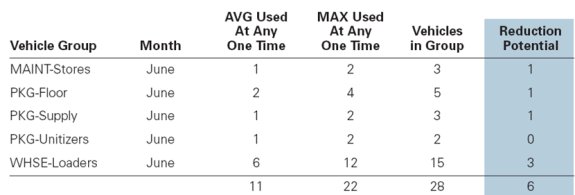
Click here to learn more about fleet reduction.
3. You want to keep your employees as safe as possible. Workplace safety for employees is important to all businesses. In warehouse and manufacturing plant environments, OSHA has put numerous safety regulations in place to help ensure a safe work environment. Specifically:
- Before use, drivers are required to inspect vehicles for unsafe conditions.
- Employers need to ensure that only trained operators can operate forklifts and like equipment
Ultimately, everyone needs to comply with these regulations. A VMS can help you do so by enforcing daily vehicle safety checklists, as well as tracking and authorizing drivers’ access to vehicles.
Using a VMS, vehicle checklists are electronic and automated, so each driver must complete the checklist before operating the vehicle. This not only enforces compliance, but it also eliminates the burden of administration and storage of paper-based checklists. Also, if safety issues are identified by a driver, maintenance is automatically notified and based on the severity of the issue, the vehicle can be locked out/tagged out.
Once you have trained a driver, how can you ensure that only those drivers are operating vehicles? By using access control, only trained drivers that are current on their licenses and certifications are permitted to operate vehicles. When an operator logs-in to a vehicle, they also become responsible for all of the actions that follow. How many times do you see anonymous damage in your facility – to the racks, inventory, and the vehicles themselves? A VMS also identifies unsafe driving, including speeding and impacts. Accountability drives behavioral changes.
A VMS makes the workplace safer not just for the drivers, but for the hundreds of other employees and pedestrians that work so closely around them. The cost of one incident, whether it’s from an untrained driver, or major damage to a rack from careless driving can often more than justify an investment in VMS technology that helps manage these conditions.
Click here to learn more about reducing damage and increasing safety.
|