Holste Says: |
 |
When faced with a system purchase, especially for the first time, companies are well advised to bring onboard an industry consultant or independent project manager who has a proven track record and will ask the appropriate questions and provide trusted advice. |
|
What Do You Say?
|
|
|
|
Previous Columns by
Cliff Holste |
|
|
When considering a system purchase, companies are almost certainly entering into a relationship of some considerable duration which makes the choice of system providers all the more critical. Buyers should be aware that some system providers subcontract critical portions of the project, such as controls engineering and software development, to an independent contractor. All too often a subcontractor’s lack of involvement in the proposal development and initial planning stage can lead to missed functionality, confusion and delays during installation and commissioning.
When faced with a system purchase, especially for the first time, companies are well advised to bring onboard an industry consultant or independent project manager who has a proven track record and will ask the appropriate questions and provide trusted advice.
Prior to signing the sales agreement, buyers should make sure they understand who will be designing and providing the major components and system integration by asking HOW the system design specification and implementation requirements will be met, and WHO will train operators and provide backup services during the warranty period. The buyer should request a list of subcontractors and their contractual responsibilities.
Differentiating between a standalone equipment purchase and a system purchase can be tricky. It's not unusual for a company to be thrown off track by what appears to be a straight forward equipment purchase but is actually a more complex system purchase.
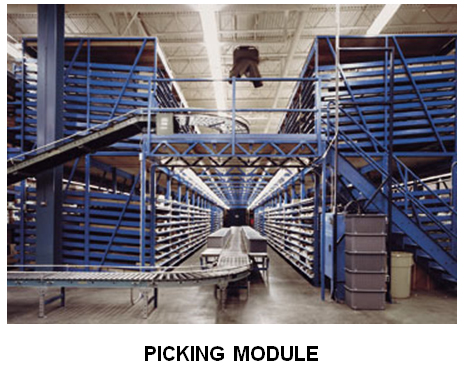
Picking Modules (see picture) are a good example. Most companies choose their picking modules based on the type of products to be stored and operational features relative to pallet flow, carton flow, or piece picking functionality. Exclusive of any powered equipment and software programs, pick modules may appear to be a commodity item similar to static storage racking. However, given the number of different components included in a pick module, they tend to be application engineering intensive. And, while they are stand-alone static structures, they must integrate with system operations and the people using them. Upon closer examination, you discover that there are many issues/questions that need to be considered, such as:
|