Eliminating these errors is where RFID can play a key role, Rush says.
“"When you can eliminate the need to scan the pallet or the location you are putting it in – where load and location are automated – you can eliminate those errors and get to really efficient warehouses,” he says.
The opportunity to use RFID is exceptionally favorable for companies that have limited use of bar coding currently, but there is often a strong business case for RFID in the DC even if some level of bar code tracking is already in place, Rush says.
Companies are often surprised, Rush says, at how many elements of a job have been added on to workers over time, negatively impacting productivity. For example, he frequently sees DC operators writing down numbers or other information even in traditionally automated systems, delivering a hit to productivity and serving as a source of errors.
At one pharmaceutical industry company, Rush says that by automating raw materials and work in process inventory in a plant warehouse with RFID, the elimination of errors and lost time was equivalent to gained productivity of 15 operators. That provided a rapid payback and a 37% internal rate of return (IRR). These kind of numbers are common, Rush said, but only if you really spend the time to see how processes can be improved with RFID automation.
“The one question we always get is ‘Have you tried everything else? – Lean, Kaizen, etc.,”" Rush said. “The answer is usually yes, all those things have been tried. The DC needs a new set of tools.”
Fork Truck-Based Systems
An RFID tracking system in the DC for now usually is best focused on pallet and other unit load tracking, such as rolls of paper. Carton-level tracking is coming, but is probably still some time away from really working well.
The Rush Tracking Systems’ solution is interesting, and uses a wide variety of technologies on a fork truck, including a unique positioning system that actually does not use RFID tags on the locations, but rather an optical system that references location codes on the ceiling, delivering precise XYZ location coordinates. That data is then mapped to actual storage locations in racking or on the floor.
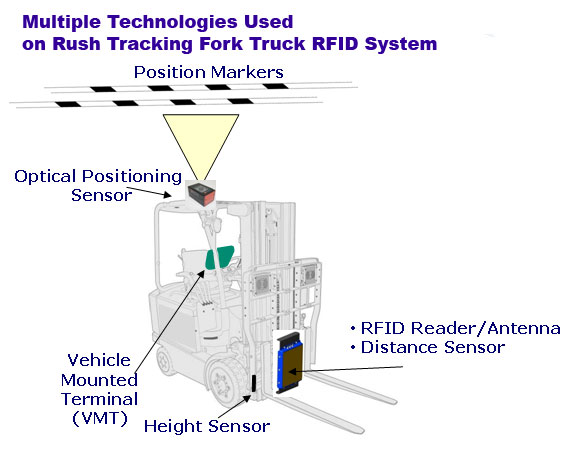
In addition to eliminating the need for tags on storage locations, the system knows if a unit load is moved even just a few feet, such as in a staging area, places where bar code-based systems can sometimes lose track of inventory.
End of Cycle Counts?
Just as bar code-based systems and WMS eliminated the need for annual physical inventories in many DCs in favor of cycle counting, RFID has the potential to eliminate cycle counting itself, given the automation and accuracy of every pallet move.
Rush says that several companies they work with are trending that way in the reserve storage areas, often only cycle counting if there has been some type of manual operator adjustment.
“The challenge is not the warehouse guys, it’s the accounting guys,” Rush said. “As companies get more comfortable with the level of accuracy, the level of cycle counting will generally decline.”
Do you think there is a good case for RFID in the DC? Why or why not? Is there a greater cost of errors and information quality than many DC managers or execs realize? Let us know your thoughts at the Feedback button below.
SCDigest is Twittering!
Follow us now at https://twitter.com/scdigest |