You may have seen somewhere along the way - I certainly have many times - a statement along the following lines: 80% of a supply chain's total cost structure is locked in based on its physical design.
The import of that statement - to the extent it is true - is that it means all the other work companies do to reduce supply costs (improved productivity, better transportation planning, etc.) can only impact the mere 20% of those costs that are not locked in by the design, indicating you should be spending a lot more time on the latter area than most companies do.
It is not clear where that 80% factoid came from, though I know (I read it myself at the time) it may have emanated from an article written by a PRTM consultant many years ago (I can't find the reference today). It has been repeated many times since, including by me, whether or not that was the original source.
Gilmore Says: |
I think the Unilever approach was very innovative, not dissimilar to an unconstrained network analysis but with a different goal and thus result.
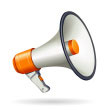
Click Here to See
Reader Feedback |
Is it true? I don't think anyone really knows. I have asked several of the best minds in supply chain network design (Mike Watson of Northwestern, David Simchi-Levi of MIT, Tony Brzoznowski of LLamasoft, Jeff Karrenbauer of Insight, etc.) whether they believe this statement to be true, and all have said they aren't really sure. Several of them have said they would be interested in looking at this question more closely.
All that as a preamble to one of the more interesting conference presentations I have seen lately, from Matt Algar of Unilever, at the recent LLamasoft user conference in Ann Arbor, MI.
I believe it sheds some bright light on this very question.
I attended the session based on its title of "Defining the Perfect Logistics Network," interesting on its own right, but especially relevant for me based on some thinking I have shared on the coming era of what I call perfect logistics. The presentation turned out different than I expected - but was compelling nevertheless.
Algar made the initial point that as in virtually every company, each year the Unilever logistics organization was given targets from the top relative to cost reductions for the coming year. But he said, did anyone really have the context or understanding to know whether those targets made sense? And while Unilever generally found a way to hit those targets, did it sometimes do so at the expense of other areas less closely measured, or achieve the short term goals while doing some damage to the mid- or long-term strategies?
These I think are very interesting, important and near universal questions. How to address them?
These issues somehow led Unilever to ask deeper questions about what comprised and drove its total logistics costs. And the starting point was this: what would its logistics costs be if it in fact had a "perfect" US network? And if it could determine that, how then could it explain the delta between what those perfect network costs would be and what it actually spent?
I have certainly heard of many companies doing "unconstrained" supply chain network designs at the start of a project, but never quite in the way Unilever went at it.
So using the LLamasoft network design tool, that is exactly what Unilever did. It started by calculating what its logistics costs would be in a perfect logistics network , where all plants all plants could make all products, everything went out in a full truckload from manufacturing sites, there were never any expediting costs, etc. It also involved benchmarking what the best market rates for transportation would be in such a network.
That ideal network, it turned out, would operate at logistics costs equal to 55.8% of the current spend.
So, how to explain the other 44.2% of costs? Unilever then nicely segmented those out by category:
• Costs of from its actual physical network of DCs and third party co-packers (logistics costs only): 25.7% of the total
• Operational inefficiencies, include transportation mix deviation from the perfect model: 8.78%
• Customer "Cost to Service" (accessorial charges from customer deliveries, orders that caused extra logistics costs, etc.): 7.98%
• Volume phasing (production/shipping volumes fluctuate, causing overtime, end of period inefficiency, etc.): 1.66%.
This is shown in the chart below (SCDigest re-creation from presentation data):
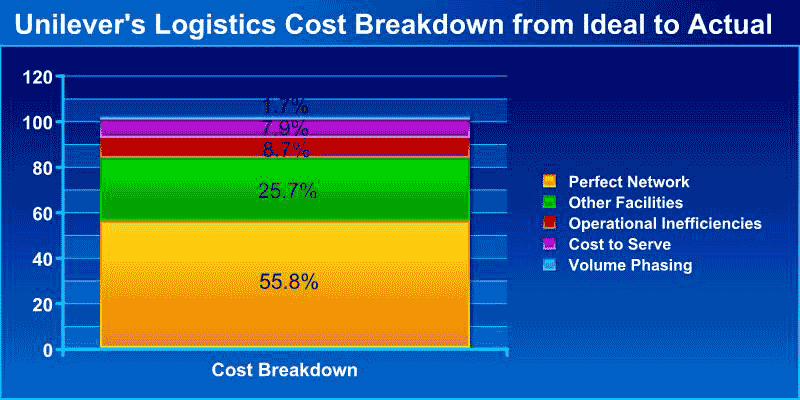
I hope the merit of all this is clear. Unilever was able to attain a much deeper understanding of what drove its logistics costs, and pinpoint the true impact of inefficiencies. It allowed a much more informed and intelligent approach to setting cost reduction targets. It provided great insight to help with the effort to reconfigure its existing network towards a more optimal one. And it would provide much greater clarity in making trade-off decisions, such as between manufacturing and logistics costs.
It also in the end changed the mindset within Unilever.
"We saw that logistics savings would need to shift from tactical operating efficiencies to strategic changes in customer terms of sale, manufacturing profiles, and distribution," Algar said.
LLamasoft's Brzoznowski recently told me that "This approach helps show supply chain and corporate leaders how far their current operations are from optimal." I think that would be eye opening for many companies.
The aforementioned Mike Watson, who writes our "Supply Chain by Design" column, noted that generally, the first step in a network design project is to build a model that can explain/predict current logistics costs. Next, he says, you build an "optimized baseline," where you apply all the rules that should have been followed but often aren't, to see what costs should have been.
"The Unilever team took this idea a step further - they came up with a nice extension to the idea of the optimized baseline," Watson recently wrote for us. "They asked questions like what if every product could be made everywhere, what if every part was transported as if it were on a full truck, and what if everything traveled on the ground vs air."
So, I think the Unilever approach was very innovative, not dissimilar to an unconstrained network analysis but with a different goal and thus result. I think many if not all would benefit from doing this kind of analysis.
By the way, Unilever has started to do this same program in other geographies, and found the cost breakdown - from the ideal network costs as a percent of current spend to the percents in each of the "inefficiencies" buckets, varies significantly.
So, with that last thought, I circle back to the issue of how much of a supply chain cost is "locked in" by the network design. Does this Unilever exercise provide any insight into that question?
Indeed it does. In its case, the network costs locked in are a combination of the ideal costs (55.8%) plus the costs of the network it really operates (25.7%) - for a total of 81.5%. The only costs that could be attacked from operational improvements, if you will, are in the other three categories, equaling just 18.5% of the total. Conversely, it has a 25.7% opportunity from improved network design. That is very interesting indeed.
Those numbers will be different for all, of course, but it looks like the PRTM guy or whoever it was may just have been right.
What is your reaction to Unilever's perfect network exercise? Do you agree it sheds light on how a network locks in costs? Let us know your thoughts at the Feedback section below.
|