Printer/applicators don’t work alone. A variety of other necessary equipment makes up a complete working system. The illustration above shows a typical configuration. The following is a brief description of each major component:
De-Palletizing Station (Optional)
This optional piece of equipment addresses the ergonomic issues involved in the manual de-palletizing operation. The unit automatically positions the pallet load while eliminating the need to bend, stretch or strain. Its unique design allows the pallet to elevate as the cases are removed maintaining the top of the load at a convenient working height. The rotating top ring minimizes walking or reaching during the de-palletizing process thereby increasing productivity.
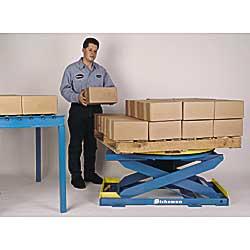
Printer/Applicator
Mounted directly to the conveyor, or on an adjustable stand, the print-and-apply machine incorporates a print engine, and an application device which uses one of several common technologies (e.g., tamp or blow-on). It also provides user settings and controls, and label media unwind and rewind devices. The applicator is mounted so that it can place the label exactly where it is needed on the case (e.g., precisely positioned on the side, top, or end).
Warning Lights
A series of colored lights on a pole, easily visible to operators, that flash to signify various errors or conditions, such as low media and “no read” bar codes.
Carton Notification Scanner
Usually a fixed-mount line or omnidirectional scanner that reads the appropriate bar code on the case, such as a license plate ID or SKU/UPC number, and relays that code to the control software.
Photo eye (P/E)
A sensor that detects the product as it moves down the conveyor and sends a signal for the applicator to print a label. Sometimes other sensors serve this purpose.
Buffer Conveyor
Can be a couple of sections of gravity roller conveyor, or if more buffer is needed, it could be a longer run of zero pressure accumulation conveyor.
Meter Conveyor
A conveyor just upstream from the applicator; it provides adequate spacing between cases to be labeled.
Skew Conveyor
A live roller conveyor, with skewed rollers, that drives the case over to the applicator side of the conveyor bed.
PC with Applicator Control Software
Can be anything from a simple label design/print package with database look-up capabilities to a more sophisticated software program that accepts downloads from the host, does database look-ups, generates printer formats and data streams, and sends data records back to the host, WMS, WCS, or some other system.
Programmable Logic Controller (PLC not shown)
The PLC provides conveyor control, such as shutting off the conveyor in the event of a “no read”. It may also be used to activate warning lights, or to actually send the firing signal to the applicator. More sophisticated controls may be used for controlling induction into the applicator system, downstream weigh in-motion scale, and the shipping sortation system.
Verification Scanner
This scanner verifies that a readable label was applied to the correct case. This information is usually sent back to the applicator or conveyor control system. If a “no read” occurs, the conveying system should shut down until the problem is resolved.
|