|
|
SCDigest Expert Insight: Supply Chain by Design
|
About the Author |
|
Dr. Michael Watson, one of the industry’s foremost experts on supply chain network design and advanced analytics, is a columnist and subject matter expert (SME) for Supply Chain Digest.
Dr. Watson, of Northwestern University, was the lead author of the just released book Supply Chain Network Design, co-authored with Sara Lewis, Peter Cacioppi, and Jay Jayaraman, all of IBM. (See Supply Chain Network Design – the Book.)
Prior to his current role at Northwestern, Watson was a key manager in IBM's network optimization group. In addition to his roles at IBM and now at Northwestern, Watson is director of The Optimization and Analytics Group.
|
|
By Dr. Michael Watson
February 10, 2015
|
|
Network Design and Accounting Data
Accounting Data is Good for Accounting and it Might not be the Right Data for Network Design Projects
|
|
Dr. Watson Says: |
 |
...The simple answer is that accounting data is for accounting and paying taxes, not for making operational decisions... |
|
What Do You Say?
|
|
|
|
When I ask, “do you have clean data?” before a network design project starts, the answer is almost always “Yes.” The realitiy is that almost no one has data that is ready for a network design project.
At first, I tought people just didn’t know that their data wasn’t clean. But, something didn’t feel right—how could people not know the state of their data. I had to develop a new hypothesis. The new hypothesis was that when I said, “do you have clean data?” people were answering a different question—that question was: “do you data that allows you to keep product flowing, close your books, pay your bills, and do proper financial reporting?”
For that latter question the answer is almost always “yes.”
So, how can you have clean enough data to meet all your financial obligations and not clean enough to to a network design project?
The simple answer is that accounting data is for accounting and paying taxes, not for making operational decisions.
For example, accounting systems need to allocate costs to products. This cost includes assupmptions on fixed costs and the utilizaiton of equipment. Using this cost to make decisions on what should be made where, including the overhead cost may lead to poor decisions.
In other cases, the accounting system only needs to know that it sold product to a certain customer—it doesn’t need to know where it shipped products for that customer. Knowing where you ship your products is obviously important to a network design study.
Previous Columns by
Dr. Watson |
|
|
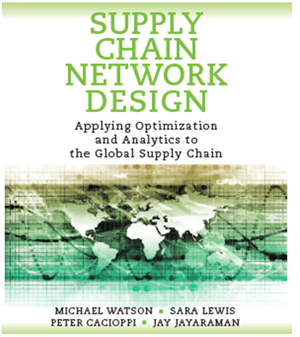 |
|
In our book, Supply Chain Network Design, we devote a chapter to modeling fixed and variable costs. In this chapter, we stress that you should think about the types of decisions you need to make before deciding how you want to model fixed and variable costs.
At the beginning of a week I had VP of Supply Chain tell me: “There is no such thing as a variable cost, I can’t make any meaningful change to building or labor force once they are in place.” At the end of that same week, another Supply Chain VP told me: “There is no such thing as a fixed cost. I can change anything over time.” |
Those two quotes sum up your challenge as when doing network design studies. You need to determine the right balance for the decisions you are making.
|
Final Thoughts
Dan Gilmore wrote a nice series of articles on what a supply chain manager should tell an accountant (part 1 and part 2). I think it is important for both sides to the business to better understand how they use and look at data. |
|
|
|
|
|
Recent Feedback |
Michael, I read with interest, your article on the importance of clean data (accurate data for intended purposes). I thought I'd offer an actual example of the importance and the impact it can have on a business, from a non-accountant's view. Sometime back, I was working as an employee for a Fortune 500 company, with manufacturing and distribution locations across the globe. The "Corporate Objective" was to implement the Company's version of "EVA", as a universal means of evaluating Subsidiary performance. However, my charge was to help the subs implement continuous improvement. After performing an operational review along with a review of Holland's financial statements, I had my first meeting with the Holland Subs President and his Controller at dinner. We discussed both topics and plans for EVA and Continuous Improvement. I also expressed my concerns about their use of Standard Cost as if it were the "Actual Cost", in the evaluation of CI team improvements. I explained in detail, why GAAP accounting and allocating overhead using labor/machine hours, could lead to erroneous pricing decisions, and the Controller agreed with me. This floored the Subs President. I proposed to them, a simplified form of "Activity Based Costing" for developing their cost data, off-line, and contrasting it against the Std. Cost. The Controller liked the idea. With guidance from me, it took approximately 6 weeks to develop the ABC data. The contrast in costs were eye opening. What they saw was that their biggest sellers (highest volume) were actually over absorbing their share of the overhead, meaning they were in reality higher in profit. And the lower volume products, were actually under absorbing their share of the OH, making some of them actually unprofitable. The Subs President was perplexed and asked for advice. My comment to him was that he had a decision to make: a.) continue to sell certain products at a loss, knowing full well the impact, or, b.) raise prices on those same products to make them profitable, running the risk of perhaps losing some revenue. The second part to decide was whether to lower pricing on the high volume products and perhaps gain market share, or leave the existing pricing in place. He decided to contact the customers who were buying the affected lower volume products and explain that a price increase was coming, because it was no longer profitable for the company to manufacture and sell. The result was "0" loss in sales, with some customers actually increasing their orders. There were no order cancellations, and he retained all affected customers. He elected to leave the pricing in place for the higher volume items. The conclusion is that the Holland subsidiary went from 2nd to last in Europe, within the corporation out of a field of 12, to 2nd highest in profitability in a 7 month period. Also, the CI teams now had a more accurate measure of what activities cost, as they implemented improvements. That's how important it is to use data properly, for it's intended purposes. They continued to use the Std. Cost data for financial reporting to Corporate and the financial statements, but, used the off-line cost data to make business/operating decisions. I hope I have in someway illustrated your point on the importance of "clean" data, being careful to understand how it's constructed and the purpose for using the data. Once word got around, requests for my assistance increased dramatically and expanded to include the Asia Pacific. Subsequently, the parent company was acquired in a hostile takeover.
John Casper
Free-Lance Consultant
Searching for a Position
Apr, 09 2015
|
|
|
|
|
|
|