Dr. Watson Says: |
 |
...you should consider using air shipments to avoid opening a new warehouse. |
|
What Do You Say?
|
|
|
|
Dan Gilmore’s article on A Decade in Supply Chain Mega Changes inspired me to think about a classic problem that hasn’t changed in the last 10 years.
Over ten years ago, I published an article, along with Jim Morton (at the time with UPS and now with Ernst and Young) in Parcel Shipping and Distribution (now just Parcel) about how the use of air freight can alter the traditional cost vs service trade-off in network design.
In the traditional view of the trade-off, you need to have more facilities closer to your customers to get better service. Here service is defined by the time from when a product ships from your warehouse until it reaches your customer. (There are other service definitions like making sure you can actually pick the order quickly or making sure you have the item in stock when needed—but that is for a another article).
But, adding an additional warehouse to your supply chain adds costs—there is the cost to build and run the facility, the cost to replenish the facility, and the cost to hold inventory in another location.
The following map shows five warehouses and the territories serviced within 1-, 2-, and 3-days of the warehouse using UPS Ground services.
Previous Columns by
Dr. Watson |
|
|
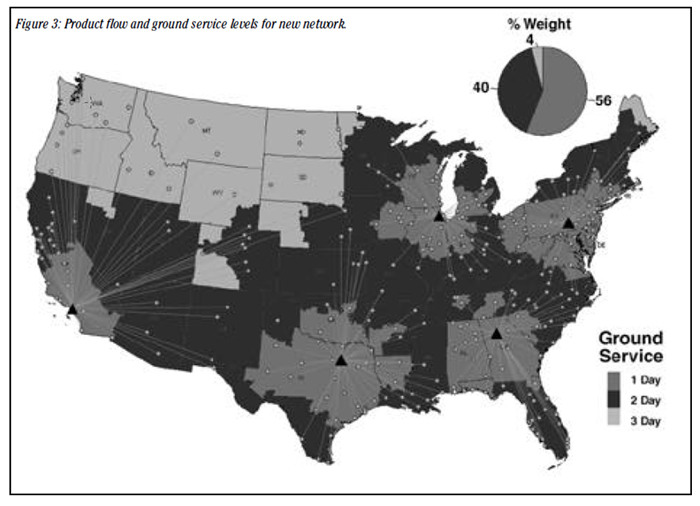
The old network design tip which is still applicable today, is that you should also consider air shipments (or expedited shipments, in general) instead of just locating more warehouses. That is, it may be less expensive to use a different mode than to add additional warehouses.
The new trade-off is between the number of warehouses, the mode and carrier service you use, and the customers you can reach within your service agreements. In the case above, you should consider using air shipments to avoid opening another warehouse.
|