Dr. Watson Says: |
 |
...Another way to take control of inbound freight is to analyze the trade-off between delivery frequency and inventory. |
|
What Do You Say?
|
|
|
|
Supply Chain Digest recently ran an article about the increasing pressure supply chain managers are facing to reduce transportation costs. The article lists several ways to reduce transportation, including taking control of inbound freight.
Another way to take control of inbound freight is to analyze the trade-off between delivery frequency and inventory. Often, firms stick to a single plan across all SKUs—like having shipments every week.
There is a trade-off between inbound shipment frequency and inventory. As your vendors tend to ship more frequently, transportation costs tend to increase as you shift from full truck load to less-than-truckload (LTL). But, inventory costs decrease. As you ship less frequently, transportation costs decrease as you start to fill up trucks. But, inventory costs increase since you have more cycle stock and safety stock to protect against the long lead-times. The graph below highlights the trade-off.
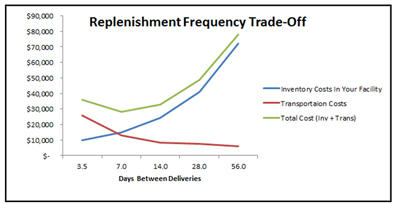
Previous Columns by
Dr. Watson |
|
|
The analysis is complicated by the fact that neither transportation or inventory costs follow a straight linear pattern. When you shift from the truckload market to the LTL market, the cost per unit of product can increase quickly. Safety stock costs also follow a non-linear pattern. The analysis is even more interesting when you consider that a vendor supplies multiple SKUs.
Each vendor will have a unique trade-off between transportation and inventory costs. As the relative costs between transportation and inventory costs change, the best delivery frequency will also change.
If you are looking to reduce inbound costs and have a blanket policy for frequency of inbound shipments, you should use this type of analysis to determine the best frequency for each vendor in your supply chain.
Final Thoughts
Interestingly, this trade-off relates to how you buffer variability in your supply chain. The Just-in-Time movement taught us that frequent shipments were better to reduce inventory. However, this implies that you are buffering variability with extra capacity (more shipments and more cost) and that buffering with inventory is somehow inferior. Instead, the analysis above questions this rigid approach and suggests that you may do better by determining how frequently you want to deliver.
|