|
Can Western Manufacturing be Saved? Part 6
I wrote my initial "Can Western Manufacturing be Saved" First Thoughts column in 2009.
Here as I coin the sixth one in the series, I will note that first one actually was titled "Can - and Should - Western Manufacturing be Saved?" The "and Should" part came from some legitimate questions as to whether the US and others were simply headed down a "post manufacturing" economic path, with the ability to compete on a low cost world stage certainly in question. And was a future of low-skill, repetitive manufacturing work really what we wanted?
Now in mid-2014, I would say the "should" question has been answered, and it is certainly Yes - though what US manufacturing looks like in the future certainly won't be much like it has in the past.
GILMORE SAYS: |
" That Parkdale Mills plant I referenced above? It produces 2.5 million pounds of yarn a week with about 140 workers. In 1980, that production level would have required more than 2,000 people, the company says."
WHAT DO YOU SAY?
Send us your
Feedback here
|
So let's look at what has transpired in recent years.
Costs in China continue to rise, and frankly wage stagnation in the US (even if that's not a good thing) continues to change global cost dynamics. The smart folks over at the Boston Consulting Group continue to do good work in this area, and recently concluded that China's manufacturing cost index was at a 96 level compared to US costs, meaning they are just 4% lower before taking into account longer supply chain, quality issues, inventory costs, etc. All of that certainly doesn't seem worth just 4%, does it?
Perhaps more important than the absolute numbers is the trend. BCG says that in 2004, China's relative index score was 86, meaning it has lost 10 points of competitiveness in a decade. (Part of me has to wonder if that 86 score is right though, because I was hearing unit cost savings in the 30+% range back then).
Beyond rising Chinese costs, we have a general move towards regional manufacturing strategies, meaning companies are becoming more likely to build in North America for this market rather than in Asia.
Another huge factor is energy costs. The US has very low costs for natural gas versus the rest of the world. At about $4.15 right now for a million BTU, that compares to about $16 in Japan, $11 in Europe, and much higher than the US in most of the rest of the world. China is paying $15 or so, but it subsidizes the price for businesses and consumers, though it has been letting the end price rise recently.
This has, anecdotally at least, led to new US manufacturing activity in energy-intensive sectors such as chemicals, metals manufacturing, and fertilizers. First new US fertilizer plant in more than 20 years is going up in Iowa, a major new Dow Chemical plant being built in Texas, etc.
There are many other similar anecdotes, and the number of them seems to be increasing. Otis Elevator recently moved production back to the US from Mexico (though not without some problems - too much, too soon). Some apparel and textile production and jobs are actually coming back to the once great Southeast textile belt. Parkdale Mills, for instance, re-opened a long shuttered yarn factory in South Carolina, and recently started supplying nearby apparel maker American Giant, which over the past couple of years has brought back most of its production from India to the US.
In American Giant's case, it was actually the "Quick Response" concepts from the 1980s that Roger Milliken tried to use to save US textile and apparel manufacturing - unsuccessfully, as it turned out - that emerged as the real driver behind its reshoring move.
LA apparel maker Karen Kane has reshored about 80% of its production from China in recent years, saying costs in China have risen, quality has deteriorated, and that domestic manufacturing provides greater supply chain agility. Brooklyn, New York recently reported that apparel production was now the fastest growing manufacturing sector in the borough, and accounts for 18% of all manufacturing jobs there, a big increase from a few years ago.
Etc.
But anecdotes are not necessarily reality, though it certainly seems as if there is something happening. But then there are the pesky numbers.
Some good news: after seven long years or so, in June US manufacturing came within a whisker of finally getting back to 2007 levels, the peak year all time for US manufacturing and the base year of the Federal Reserve's production index. Manufacturing output last month was at a level of 99.7, up from 99.5 in May. I thought we might get to the 100 level this month, but the US should be reach the old highs in the next couple of months. We're now up almost 20 points from the recent index low of 80.3% in June of 2009.
See the Full Image
But that overall rebound, which again took seven years, masks huge differences in recovery and growth by sector. Consumer goods is at 97.2, still almost 3% below 2007 levels, while the consumer durables portion of that crept over the 100 mark about six months ago and has stayed there. Automotive-related production is at a ripping 118 level - 18% above 2007. Clothing output, though, is at a mere 60.6% of even weak 2007 levels, though up a bit from the 56 mark seen in 2009. Chemicals, surprising to me, are still only at 85% of 2007 production.
You get the idea - the evidence is mixed. We'll have more detail by sector next week in OnTarget.
But I did do an interesting other little piece of research for this column. Over the last 12 months (June 2103 to May 2014 - the last month for which we have data - US imports of manufactured goods (excluding oil/energy) are actually down 2.2%. Meanwhile, US manufacturing volumes over the past 12 months are up about 3%.
Does it not make sense that this delta - 2.2% down in goods imports, up 3% in US production - could be due at some level to a real reshoring phenomenon? Maybe the trend is real beyond the anecdotes. However, one thing you realize when looking at numbers this huge - in the trillions of dollars - is that it will take a long time to see any major changes in the big picture from a reshoring trend.
As an aside, you may have seen that SCDigest and the MIT Supply Chain Forum (Dr. David Simchi-Levi) are repeating are very successful survey on US manufacturing/reshoring trends we last did in 2012. We need some more survey respondents. Can you help? Please go here: US Manufacturing Survey.
One thing we also know, however, is that manufacturing in the US is becoming more "advanced," a somewhat synonym for automated. And the robotics age is really just getting started. A whole new generation of robots from companies such as Rethink Robotics and now Google itself I think unquestionably will be populating factory floors by the tens of thousands if not millions in the coming decade. The real breakthroughs, actually, are huge advances on the software side, not the physical, though there is much progress there too. But the new robots are far more flexible than previous generations - a critical change.
And now we face the jobs reality. As we reported earlier this week, a report out of California found that manufacturing output in the state is up 73% over the past 15 years - while manufacturing jobs fell 34% over the same period. Think about that - production nearly doubles, and employment falls by a third.
That Parkdale Mills plant I referenced above? It produces 2.5 million pounds of yarn a week with about 140 workers. In 1980, that production level would have required more than 2,000 people, the company says.
This is simply the reality.
There is new and I think real hope for US manufacturing. I don't thing that Europe and Japan have as bright a path, for a variety of reasons. One big question mark for the US though is how much of the potentially "reshored" production will wind up in Mexico, not within the US border.
But this is the best spot we have been in since the 1990s. Yes US manufacturing should be saved due to the overall economic impact, some positive impact on direct manufacturing jobs but an even bigger impact on indirect jobs, keeping ahead in innovation, better retaining intellectual property, and improving national security from not losing too much production capacity.
Hope you agree. Please help the cause by taking the survey.
Do you think the reshoring trend is real? What do you takeaway from these numbers? Let us know your thoughts at the Feedback section below.
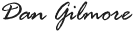
|