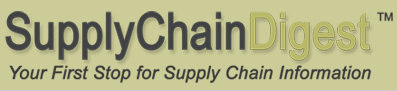 |
|
|
Featured Sponsor: CDC Software
|
|
Learn How Boston Scientific Cardiac Rhythm Management Optimized Working Capital
through Supplier Collaboration and Inventory Management
Get The Webinar and Related Aberdeen Report
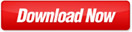
|
|
|
|
 |
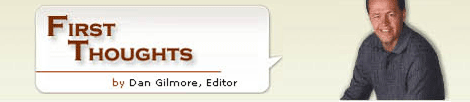 |
|
TUESDAY'S VIDEOCAST |
How Smarter Inventory Analytics Solve the "Out-of-Stock" Scenario for CPG Supply Chains
Fulfilling the Three A's:
Adaptability, Agility and Alignment
Featuring Dr. Michael S. Watson, Ph.D., WW Optimization & Supply Chain Lead at IBM and Remzi Ural, Global Supply Chain Management Solutions Lead, Consumer Products Industry at IBM
Tuesday, May 17, 2011
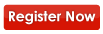
|
|
UPCOMING VIDEOCAST |
Supply Chain Risk Management: Separating Meaningful Indicators from Background Noise
Using a New Information Tool From
Dow Jones to Increase its Visibility to Sources Of Supply Chain and Supplier Risk
Featuring Dr. William Killingsworth of MIT,
Ezra Duong-Van of Dow Jones
and Dirk Martin of Safety-Kleen
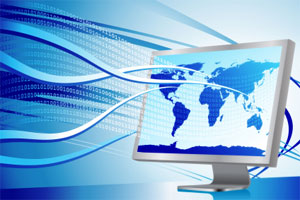
Tuesday, May 24, 2011
|
|
UPCOMING VIDEOCAST |
Vendor Compliance 101: It's about Supply Chain Excellence, not Chargebacks
Part 2: Best Practices in
Vendor Compliance Optimization
Featuring Gough Grubbs, SVP of Distribution & Logistics for Stage Stores,
Tim Divic, DC Manager for Stage Stores,
Greg Holder, CEO of Compliance Networks
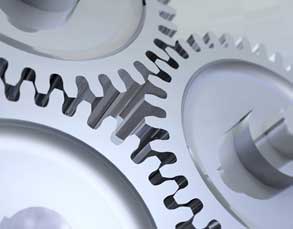
Wednesday, May 25, 2011
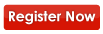
|
NEW ON DEMAND VIDEOCAST |
Harry & David Moves from Best-of-Breed WMS to SAP Extended Warehouse Management
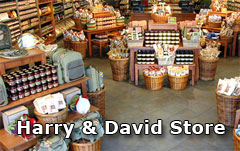
|
NEWS BITES |
This Week's Supply Chain News Bites |
|
|
|
INVENTORY MANAGEMENT CASE STUDY WEBINAR |
Key Strategies for Optimizing Working Capital
Learn How Boston Scientific Cardiac Rhythm Management Optimized Working Capital
through Supplier Collaboration and
Inventory Management
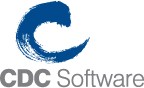
Get the Webinar and Related Aberdeen Report!
|
CARTOON CAPTION CONTEST
WINNERS ANNOUNCED! |
April 26, 2011 Contest
|
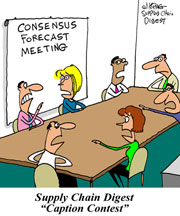
See This Week's Record Four Winners!
New Cartoon Monday on www.scdigest.com
|
|
|
|
|
|
|
EXPERT CONTRIBUTOR
FROM SEEGRID
|
By John Mazock
Vice President of Manufacturing
Seegrid
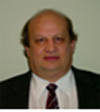
Understanding Lean Implementation
in the Supply Chain
|
|
|
|
|
Ideas for Reducing Transport Costs given Rising Fuel Prices |
Well, oil futures have recently "plummeted" to a mere $98 per barrel or so, a level that as I noted a couple of months ago that seemed like the end of the world less than five years ago. Now we complain but take it pretty much in stride.
Though some are predicting will reach $150 or so again before too long, and others citing even higher figures over the coming years, I am not so sure about that. First, in the US at least, $4.00 per gallon of gasoline does seem to be some sort of upward bound that leads to changing consumer behavior and thus demand destruction that acts as a counterbalance to upward pressures on price. Not sure if this is the same elsewhere - did you know, for example, that China significantly subsidizes gas prices for consumers and truckers?
I will also note that we are in this sort of terrible place where the most likely way we will drive oil prices back down is through a slowdown in the economy. So, if you want the lukewarm recovery to continue and maybe even expand, it has to be a the cost of higher oil prices. But higher oil prices cause the economy to contract.... my head hurts. I had one economics class as an undergrad, and one in grad school. Don't think I will drag out the textbooks to try to sort all that out.
GILMORE SAYS: |
"Your potential strategies and "degrees of freedom" will vary significantly by type of cost driver. It is a worthwhile exercise to develop that matrix and discuss it internally. "
WHAT DO YOU SAY?
Send us your
feedback here
|
All I do know is that transportation is a huge element of supply chain costs, representing 6% or so of US GDP and even higher levels in many countries, that rising oil prices add significantly to the cost of moving goods, and capacity pressures are also coming into play.
So, what can shippers do about that? I amazed at the sophistication of supply chain professionals today, so most probably know all these ideas presented below and more, but perhaps it is handy to have them in one place anyways.
One useful framework for any supply chain challenge, but I think especially so for rising transport costs, is to identify all the drivers of transportation spend and divide them into three categories:
1. Things can you can directly control: For example, how full you load your trucks
2. Things that you can't control but can manage: For example, rate or surcharge increases from carriers
3. Things that you can't control but you can influence or mitigate: For example, you can't change the price of oil, but some companies can and do hedge the price of oil to lock in a given cost.
Your potential strategies and "degrees of freedom" in each category will vary significantly. It is a worthwhile exercise to develop that matrix and discuss it internally.
With that as an intro, here are some potential areas that can lead to reduced transportation spend:
Strategic:
• |
The trade-off between inventory and transportation cost is a constant exercise. While the push in recent years is to drive down inventories; maybe it is time to shift your position on the curve. |
• |
Many networks were not built with $100+ oil in mind. I think it is here to stay - may be time to re-evaluate you network strategy. That's why having a network tool in place for continuous use can be so valuable. |
• |
Invest in a TMS, if you haven't already done so, or change/upgrade if it is old. Savings from consolidation and mode/carrier optimization through TMS can be substantial. On-demand offerings mean low upfront investment and you can be live in just a few months, and even faster in some cases. |
• |
If you haven't already, centralize transportation planning versus decisions at individual ship sites. |
• |
Hedge the price of oil (though it would have been a lot smarter a year ago) |
Tactical:
• |
Can changes to packaging be made to ship less air? For perhaps 98% of companies, the answer is yes - sometimes dramatically so. One cell phone distributor increased units on a pallet by 50% through a new package design effort. Where are you on the protection versus logistics costs curve? |
• |
Ditto for carton sizes and utilization in pick-pack operations. My friend Jack Ampuja has convinced me optimizing this can drive big transport costs for most shippers. |
• |
For those that have avoided rail/intermodal for various reasons, now may be the time to rethink that, or at least take another look. |
• |
Consider taking over greater if not total control of inbound freight. |
• |
Look for collaborative shipping opportunities; more and more companies are making arrangements with complementary shippers. But it takes work to find and develop them. |
• |
See if it may make sense to sub-optimize manufacturing to reduce transportation costs, especially in terms of uneven load patterns that exceed carrier commitments and result in expensive spot market moves. One large soft drink distributor is doing exactly that. |
• |
While you should be fair to carriers, most large companies now set fuel surcharge payment policies, rather than accepting a carrier's schedule. |
Operational/Execution:
• |
Improve trailer loading through pallet and trailer cube optimization. My friend Thomas Moore has likewise convinced me there is a lot of improvement available there for most companies. |
• |
Revisit TMS settings and assumptions. Are you limited to two-stop multi-stop routes, when maybe you could go for three, as an example? |
• |
Evaluate how consistently the transportation plan is executed as planned. Many companies have yet to well tighten up the common planning-to-execution gap in transportation. |
• |
If you have a routing guide, take steps to ensure internal shippers and external vendors are highly compliant. |
• |
Reduce the number of "bad loads" that you are dispatching (e.g., poor capacity utilization). Many shippers just live with this. See if these loads can be held for a day to improve consolidation. |
• |
Evaluate you level of expedited transportation and use root cause analysis to drop that level substantially. |
• |
Send better forecasts to core carriers to improve chances they can have capacity to support your needs. |
I am sure there are dozens of more ideas/opportunities, but these I think are some of the best.
How about adding your thoughts to the mix?
Do you like or use the framework of controllable, manageable, and mitigate-able cost drivers? What other ideas would you add to Gilmore's list of freight cost savings ideas? Let us know your thoughts at the Feedback button below.
|
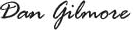
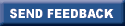
View Web/Printable Version of this Page |
|
THIS WEEK ON DISTRIBUTION DIGEST |

Holste's Blog: Managing Slow Movers -- A Renewed Sense of Urgency
|
 |
Top Story: Medical Device Maker DJO Global Finds Success with Mobile Robotic Picking System |
 |
Top Story: 16th Annual Third Party Logistics Study is Underway |
 |
Top Story: When implementing a new Warehouse Management System (WMS), Filling Two Roles on the Project Team are Key |
|
|
|
READER QUESTION |
Question: Are there guidelines for when a company should move from plant shipments to a consolidation DC?
See our Expert answers here.
Add your input - we could use some more! |
|
|
Q: |
In the famous book "The Goal" by Eli Goldratt, how long does plant manager Alex Rogo have to turn his UniCo factory around before it will be shut down? |
A: |
Found at the Bottom of the Page |
|
|
|
YOUR FEEDBACK |
We had decent Feedback on Gilmore's column on whether the Trucking Tsunami was Coming Again, and publish a few of those letters below.
That includes our Feedback of the week from David Schneider, who says shippers really need to stay on these issues, especially around Hours of Service changes, and that safety is an important facotr here, despite the critics, in a very thoughtful letter. Feedback of the Week - on New Trucking Tsunami?
A quick word on the hours of service rules.
Everybody in Supply Chain Management MUST stop demonizing FMCSA on this issue. Trucking accidents along with all of the general highway accidents were getting out of control. While there is a clear majority of safe professional truck drivers operating on our highways today there is a population that should be removed. The old hours of service rules that existed before 2003 had far too much complexity and opportunity for mischief. There is a reason why logbooks are sometimes called comic books by the driver community. Congress mandated action in 1995 and the rule changes in 2003 answered that mandate.
Since then different organizations that represented independent truck drivers and safety advocacy groups have dragged the law into the District of Columbia Circuit Court because they did not want to accept the changes. The rules took three trips through the DC circuit, and each time the court through the rules out because of technicalities. These rules are being revised again as part of the political settlement of a pending court case.
On February 17 the FM CSA posted a listing sessions on the proposed rules. This was an unprecedented event, I don't remember a time where it a listing sessions has happened after the posting of proposed rules. There is a reason why they did this. When the rules get dragged into court the attorneys that represent the plaintiffs and the defendants are allowed 15 min. to orally present their arguments. The only additional material allowed to be presented is the research used to create the rules and the comments that are legally entered into the docket during the 60 day comment phase after the rule is posted in the Federal Register. The deadline for comment is February 28, 2011. The FMCSA is actually begging for comments from the shipper community. They need data to illustrate what the cost impact is going to be.
This is an opportunity for shippers to stand up and provide information about how these proposed rule changes will affect the costs and operations of their companies. Failure to provide the data and information that the FM CSA is asking for is a mistake. If the shipper community wishes to make the change they need to stand up and be heard. Just posting it in your articles is not enough.
We have not been silent on the subject. I personally attended the listening session in Arlington yesterday. Except for some week and feeble opinions presented by the Grocery Retail Association and the Commercial Bakers Association nobody else from the shipper community bothered to speak (except for my loud mouth). In this session the shipper community was painted as the culprit for all of the safety ills -- it's the evil shippers and how they keep the truck drivers waiting on their docs that create tired drivers. I addressed how some of my clients are going to feel a significant financial pinch from the lost productivity and the lost opportunity to backhaul freight.
If you would like to learn more about the history behind the rule and what you can do to have your voice heard I recommend that you take a look at http://wearethepractitioners.com/?p=343 . I challenge you to go understand the history of why we're going through this rule setting process a fourth time. I assure you that if the shipper community does not sound off that we will be revisiting this rule again in two years.
David K. Schneider
David K Schneider & Company, LLC
More on Trucking Tsunami:
As usual, you a very timely article. Based on our executive interviews for the 2011 State of the Retail Supply Chain study, retailers are closely monitoring the CRISES issues. Fuel prices and the impact of CSA 2010 seem to be the most immediate concerns but the others are not being ignored. Also, the level of angst regarding regulatory intervention is running high.
Brian Gibson
Auburn University
To lessen the height of the Tsunami wave, shippers need to effectively use trucking.
Carriers indicate they are weeding out the "bad actors" -- shippers that, for example, keep equipment waiting, order a truck and then don't use it, or have a higher percentage of loads rejected at the scale.
Shippers must effectively use the capability of the equipment. Analysis of 850,000 5 axle trucks crossing a weigh-in-motion scale shows:
- Of the loaded vehicles, 4,000 pounds could be added to 92% of them
- 44% of trucks could haul more than 48,000 pounds
Orders need to be optimized to fully cube-out or weigh-out shipments.
Thomas A. Moore
Transportation | Warehouse Optimization
|
|
|
SUPPLY CHAIN TRIVIA |
Q: In the famous book "The Goal' by Eli Goldratt, how long does plant manager Alex Rogo have to turn his UniCo factory around before it will be shut down? |
A: Three months, a goal Rogo achieves with the help of some Theory of Constraints thinking. |
|
Copyrights © SupplyChainDigestTM 2003-2010. All Rights Reserved.
SupplyChainDigest
PO Box 714
Springboro, Ohio 45066
POWERED BY: XDIMENSION |
|
|
|
|