|
|
|
Next-Generation Supply Chain Management
New Practices and Profits for Process Manufacturers
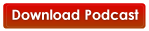
|
|
 |
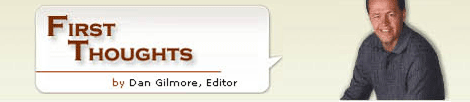 |
 |
WEDNESDAY'S VIDEOCAST |
Videocast: Agility in Consumer Goods Demand Driven Manufacturing
Improving Customer Service Despite Tight Production Constraints
Featuring Filippo Focacci, Product Manager, IBM ILOG Optimization and Analytical Decision Support Solutions
Wednesday, October 13, 2010
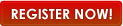
|
UPCOMING VIDEOCAST |
Videocast Series: Achieving Real Results with Supply Chain Software
Part 2: ADS Gains Flexibility in a Highly Automated DC
Featuring Paul Peavey, Director of Operations, ADS Logistic Services and Tom Kozenski, VP Product Strategy, RedPrairie
Wednesday, October 20, 2010
|
NEWS BITES |
This Week's Supply Chain News Bites
- Only from SCDigest
|
|
|
|
NEW! WHITE PAPER FROM INFOR
|
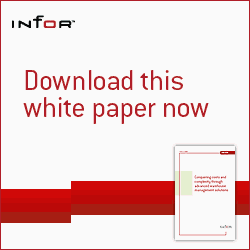
Conquering Warehouse Costs
And Complexity:
Increase Productivity Through Advanced Warehouse Management
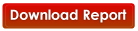
|
ON TARGET e-MAGAZINE |
Each Week: |
RFID/AIDC Transportation Procurement/Sourcing Manufacturing Global Supply Chain Trends and Issues |
|
|
|
NEW! EXPERT CONTRIBUTOR |
By James Giermanski
President
Powers International, LLC
The Southern Border and its
Commercial Traffic - A Fundamental
Weakness in US Security
|
THIS WEEK ON DISTRIBUTION DIGEST |
|
Holste's Blog: Logistics Outsourcing – Gaining In Popularity with SMBs Looking to Compete With Larger More Automated Distributors
|
|
|
 |
Top Story: Review of the 2010 3PL Study |
 |
Top Story: Key to Lift Truck Optimization may Lie in Fixing Inventory Accuracy |
 |
Vendor News: Voxware Inc. Announces 4.0 Of Its Voxware 3 Product Is Now Available |
|
|
|
SUPPLY CHAIN TRIVIA |
|
|
|
Supply Chain Tactics for the New Normal
|
As seems an unfortunate habit for me, last spring I accepted a conference speaking engagement on a subject I would have to build from scratch. What was the presentation theme the conference wanted? How about this: "Carpe Supply Chain - Thriving in the Post Recession Economy," with the abstract noting in part that the "economy will eventually erupt in confidence and opportunity. But supply chains must change to absorb the lessons of the downturn and thrive in the "new normal."
How's that for an assignment? As usual, I did nothing for quite awhile, and am glad I did, as the "recovery summer" didn't exactly happen, and I was able to offer some thoughts about what I would do given the current state of the new normal, which is certainly better than the worst, but not exactly "erupting with confidence and opportunity" quite yet.
Gilmore Says:
|
|
"Tougher times - and the desperate need for growth drivers - will likely have changed the mindsets of many trading partners with regard to collaboration."
What do you say? |
|
Send us
your Feedback here |
|
After attending a slew of conferences over the past 4 weeks, it is clear that current supply chain strategies are as varied as companies themselves, so the idea that there really a set of moves most companies should take right now is "mission impossible," as I quickly realized.
That said, what I decided to do was think of myself as the new VP of Supply Chain for the "every company," a generic composite of the average firm. From there, based on what I am seeing across companies, I tried to envision what I might do across the strategic, tactical and operational/execution domains. As usual, I tried to get pretty specific instead of resorting to empty platitudes such as "become more demand-driven" or whatever.
Strategic Actions:
- Revisit or Build Supply Chain Strategy: May be obvious in one sense, but do you even really have a supply chain strategy? Or is it just an operational plan, which is somewhat different? As
Dr. Mahender Singh of MIT noted recently, a strategy must include what trade-offs are being made, and why. No supply chain can do it all. An increasing number of companies are using SWOT analysis (Strengths, Weaknesses, Opportunities and Threats) as an element of the SCM strategy process. But the key in the end of course is compete alignment with the business strategy, which is ever dynamic today.
Inherent in the trade-offs notion as well are decisions about what we do internally and what we outsource. I suggested use of Geoffrey Moore's interesting "core versus context" framework as one useful approach to this decision.
- Re-Look at the Network Design - Frequently: Flowing from strategy, I would do a supply chain network analysis/optimization, if one had not been very recently done. The reality is many moves in the recession were reactionary: e.g., consolidating several DCs into one as demand dropped and leases expired or whatever. Demand forecasts, business and product strategies, outsourcing considerations, and many other variables have changed substantially for many companies.
A network degrades from optimal actually before the network redesign project is actually finished. Leading companies (PepsiCo, Publix, WalMart) are re-optimizing their networks quarterly, or at least looking a the potential benefits of change. Unless I had a very simple network, I would implement this same practice, convinced that for most the return is there. Analyst Lora Cecere when she was at AMR Research noted that “Average companies model their network every 2 ½ years. Best-in-class companies model their network every quarter.”
- Re-Look at Your Software Portfolio: It's time to take stock of what you use, what you own but aren't using, what options you may have from previous purchases to buy other modules at a discount. Add to that reviews with vendors about what valuable capabilities may be there in the software that you are not currently using. I would combine that assessment with a strategy that considers the growing impact and opportunity from on-demand software over the next 3-5 years.
Tactical Actions:
- Re-Think Trading Partner Collaboration: Tougher times - and the desperate need for growth drivers - will likely have changed the mindsets of many trading partners with regard to collaboration. Have a retail partner which wasn't much interested in CPFR in 2008? I would knock on that door again. It is a new normal. Lock in the collaboration now before the economy does recover and everyone gets too busy again.
- Take Control of Inbound Freight: We could (correctly) debate about the best way to think about this, which is clearly to make joint decisions with trading partners about how the freight should move in the interests of lowest total costs. But in practice, most companies not taking control of inbound freight are leaving substantial dollars (and usually service and visibility as well) on the table. Internal resistance before? Again, the barriers to change are likely down.
- Reduce SKU Counts: A VP of supply chain for a large beverage company told me recently he believes the drive to lower SKU counts are going to stick. Why? Because in a low growth, price sensitive economic environment, you need to get more profit out of your inventory, and drive production and distribution efficiencies to squeeze out more profit from each SKU you carry (so, make and sell more of fewer SKUs). To repeat the same theme again, the corporation will likely never be as open to the SKU reduciton message. One thing for sure, most will cut their losers faster, using tools like Gross Margin Return on Inventory.
- Take a Look at Inventory Optimization Software: It's complicated, and some have not succeeded, largely due to the process changes required, but this relatively new class of software has delivered substantial benefits for the companies that make it work. The key advantage: truly considers the needs for inventory holistically, across the many levels of the supply chain, not a node or level at a time. If my new company didn't have it, I would assess what it might do for us, and move forward accordingly.
Operational/Execution Actions
- Conduct a SKU/Activity Profile Analysis in Distribution: Demand and order patterns have change. Facilities have been consolidated. I have rarely seen a case where a SKU/Activity profile analysis didn't shed some important insight in regular times, and would expect that to be doubly so in the new normal. Can lead to improvement in DC layout, WMS configuration, storage mode decisions, slotting, and ultimately technology employed in the DC. Good bang for the buck.
- Consider a DC/Plant Audit: Somewhat along the same lines, consider a DC or plant audit. Companies and managers are often reluctant to bring in an outsider to do this, in part because they don't want someone pointing out what they are doing wrong, and often because too often the audit is really just a sales exercise for more work from the consultant/vendor. But if done well, audits can provide ideas and insight. Find someone who specializes in this work, see examples of past audits they have done, and spend $5000 or something to get an outside perspective.
- Don't be the Last to Adopt Labor Management: As I have said many times, Labor Management Systems have a proven track record of high success and a very favorable "pain to gain" ratio. Once a niche, they are now mainstream. If my new company hadn't yet gone forward, I would get a program together quickly. Note LMS (now increasingly called Workforce Management) isn't just for DCs any more - it is being used for delivery drivers, retail stores, hospitality, even the shop floor (e.g., solution from ScheduleSoft).
- Relook at RFID: Much has changed since the rise and fall of the WalMart program - even at WalMart itself. While it makes no sense to take a technology and try to find a business problem, given the improvements in technology, price and other factors - including rate of adoption - I would re-invigorate taking a look at what supply chain challenges we have and how RFID might be part of the solution.
So that was my list. I realize some or none of it may make sense for you, but my audience seemed to like it. I'd be interested in what you think are key steps to take in this "new normal" - whatever that really is.
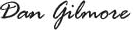
Any reaction to Gilmore's recommendations? What would you add to the list of things to do now as we slowly emerge from the recession? Let us know your thoughts at the Feedback button below.
Web Page/Printable Version of Column
|
|
|
|
|
|
|
SCDIGEST RSS FEEDS |
Do you use an RSS reader? Do you
have a MyYahoo! or personalized Google page?
For
these and more you can have SCDigest delivered right
to your personal pages, all week long.
You can subscribe to our RSS feeds in two ways: |
- Copy our RSS link into your
RSS reader - it's easy! www.scdigest.com/rssfeeds.xml
- Click on a button below to
quickly add it to your favorite readers.
|
|
|
|
YOUR FEEDBACK |
We received a large number of letters om a series of articles we did on WalMart's program to take greater control of its inbound freight, including a guest First Thoughts column from Dsvid Schneider on the subject. (See
Understanding WalMart's Inbound Freight Strategy.)
Most of the letters were short and sweet thank yous for the work and thoughts, but some added additonal insight ,including our Feedback of the week from Paul Soper.
Feedback of the Week - WalMart Takes Control of Inbound Freight:
The 100 mile deadhead from DC back to a vendor is one point, but a similar deadhead exists at the other end or at the Store. For an inbound carrier to go to a store sounds good, he is unloading at one side of the DC and the load to “a store” is already loaded on a fleet trailer with roll up doors, whether its truly their own or a contracted dedicated fleet who has to operate with specified grocery trailers.
If its food DC and perishables it’s a multi temp trailer, it may work with dry vans but here again, that inbound carrier would have to have drops or live load. The drops on the dry side are mostly walmarts own trailers for outbound I believe with exeption of a few very large carriers. I think they can accomplish more on the dry side than the Grocery DC side. The stores and the DC prefer roll up doors.
Shippers on the other hand often prefer swing doors on refrigerated longer haul movements Also many grocery trailers are flat floor and lack circulation for temp controlled loads and generally weigh more. In that the grocery side represents 51 percent of WMT sales revenues, they will have to deal with these scenarios.
Many of the big volume vendors have drop trailer from the core carriers, but presently its not feasible to have all the extra trailers that may be needed,,,,not so much a cost standpoint of trailers, but the shear lack of room for them at vendors premises, some vendors now only have so much room for drops. The same goes for the Walmart DCs, they do have extra property to pave, but presently they were designed for X number of trailer spaces. The guy coming in for a customer pick up live load at a vendor is getting loaded later, not faster in most cases.
I watch it closely, as I was instrumental in talking WMT into using outside dedicated carriage for grocery distribution in the fall of 1992, at a time when they had every intention to do it themselves..the trucks and trailers form Great Dane were already ordered for the first food DC in Clarksville, Ark. We called it Clarksville Refrigerated Lines, or CRL, later named it Transport Industries. I left, 2 years later it was sold and the new owners renamed it Greatwide. (and yes we did plenty of pickups when it made sense.) its an old idea being aggressively ramped up.
Paul Soper
More On WalMart Takes Control of Inbound Freight:
Great article; excellent work. I particularly liked the delineation between tactics and strategies.
Andrew Owens
Ingram Micro
Good edition.
We saw the value of leveraging our in-house fleet following the implementation of our E-Tendering tools in 2009. Later that year, we launched the Direct Ship Initiative to ensure that our suppliers had visibility to our delivery routes/returning vehicles for the purposes of scheduling inbound materials. Rolled-out in January 2010, the program has begun to gain real traction as the tendering application continues to evolve in both coverage and sophistication. As we evaluate the next generation TMS, the ability to manage, expand, and optimize the utilization of the in-house assets will be a key differentiator.
Bill Ray
Director of Procurement
Ply Gem Industries, Inc.
Billing back every Wal-Mart vendor 6% of invoice doesn’t hurt their cause either ! I believe that was the point being made in the original article “Wal*Mart Takes Control Of Inbound Transportation”. That extra cash pays for a lot of potential ½ loads and “dead” miles.
What I can’t wait to hear about is what is going to happen when Wal*Mart can no longer blame and (more importantly) penalize vendors for “missed window” deliveries as they will be handling these themselves.
For my money, Wal*Mart will never service themselves in this area as well as they are being serviced by others. Transportation is not now – nor will ever be a “core competency” of Wal*Mart. They will find (like many others have already) it is better to be a customer of someone else who is actually in the business of the service they need – than to try and provide it themselves.
Wal*Mart isn’t just any other retailer and their culture certainly shows that – just ask their vendors.
Sometimes you just have to know when too much is too much!
D. Anthony
I agree with everything you’ve stated so far. However, the high percentage of empty miles the Wal-Mart fleet is traveling has got to be one of their main goals. As an experienced cost justified transportation manager with a large grocery retailer, I can attest to the benefits. It took me years to battle the merchandisers over this concept and just days with our distribution management group. We became a profit center as a result, not a cost center.
P. Bleeker
Rochester, NY
|
|
|
SUPPLY CHAIN TRIVIA |
Q. |
How many cases does Wal-Mart move through its US distribution center each year?
|
A. |
About 5.5 billion cases.
|
|
|
Copyrights © SupplyChainDigestTM 2003-2010. All Rights Reserved.
SupplyChainDigest
PO Box 714
Springboro, Ohio 45066 |
|
|
|