|
SCDigest Editorial Staff
SCDigest Says: |
In this particular application, the grocer finds its overall productivity is higher if it lets experienced operators see the upcoming picks and intelligently build the pallets based on that knowledge of the SKU slotting and case attributes.
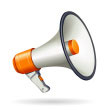
Click Here to See Reader Feedback |
The use of Voice technology in order picking has been growing rapidly in recent years, as companies find the productivity and accuracy advantages of this “hands free” approach offer significant operational benefits. (See our Advanced Order Picking Systems Resource page.)
But Radio Frequency (RF) terminal providers aren’t sitting still and watching market share just go away. Some providers, such as Motorola’s Enterprise Mobility Group, have released a new generation of “wearable computers” that offer many of the same potential benefits as Voice. These devices are small, wireless terminals worn on an operator’s wrist, typically with a small “ring scanner” worn on a finger (see photo nearby).
In doing research in this area, Steve Banker, an analyst at ARC Advisory Group, uncovered an interesting potential advantage of the wearables for some distribution applications – specifically, the ability to leverage an operator’s experience and intelligence in performing the task.
Banker interviewed one large grocery chain (17 total distribution centers) that has extensive experience with both traditional RF and Voice (which has strongly penetrated many companies in the grocery industry). In a recent research brief (Warehouse "Wearables": How to Turn Pickers into Knowledge Workers), Banker says the company turned to wearables over Voice because the technology, in conjunction with its WMS, allowed workers to see several picks ahead and, therefore, use their experience to build better mixed-SKU pallets for stores.
Using “Look Ahead” Processing
Banker says that like many companies, this grocer wants to build good pallets that come close to always putting the heaviest items on the bottom, medium SKUs in the middle, and the lightest on top. This minimizes product damage and can contribute to efficient receiving and shelf stocking in the store.
(Distribution and Materials Handling Article - Continued Below)
|
|
|
The chain, as many others, slots its DC by store aisle, so that “aisle ready” pallets can be built, and in general slots SKUs from heaviest to lightest in the direction of picking. However, orders and slotting aren’t perfect, so a direct picking sequence for any specific order, in location sequence, would often not result in building a pallet the optimal way.
However, the wearables, integrated with the grocer’s Warehouse Management System (from Infor), allow order pickers to look ahead at a number of upcoming picks and make pallet-building decisions upfront.
Banker says he found that “The biggest advantage of RF wearable computers for this retailer is that they have designed the screens to give their workers forward visibility into what they need to pick so they can apply human intelligence to moving efficiently through the warehouse. This is something that speech [Voice] does not permit.”
The WMS at the grocer pre-builds pallets based on weight, cube and sometimes store receiving constraints. However, it does not force the pickers in a specific pick sequence. In an interesting approach, the wearable RF terminals (Motorola’s WT4000’s) allow the operators to quickly toggle between three screens:
- Aisle Screens: Shows the aisles that their next wave of picks will come from. There is an asterisk next to those aisles that have “base” (large/heavy) products to be picked. If an aisle does not have an asterisk next to it, the picker knows not to start the wave in that aisle.
- Bay Screen: Shows the bays in the aisle the operator will need to pick from, along with the number of cases to be picked in the bay. “This screen helps the order selector to move intelligently within an aisle,” Banker says.
- SKU Screen: Contains a description of the item on the top of the screen. For example it might say, "Brand X Ketchup, size 10 ounces, UPC number 123456." In the middle of the screen, in a large bold font, it shows the number of cases to be picked.
In this particular application, the grocer finds its overall productivity is higher if it lets experienced operators see the upcoming picks and intelligently build the pallets based on that knowledge of the SKU slotting and case attributes. With Voice, which would not enable “look ahead,” Banker says that the grocer’s order selectors spend more time rebuilding the pallets to ensure the base items are on the bottom.
Of course, there are trade-offs, SCDigest believes. First, the grocer’s approach must mean extra travel time in order picking, as pickers pass SKUs early in the aisle to go select a heavier product first, then return to the skipped slot. Second, the approach would not work with inexperienced pickers, which would probably benefit more from complete system direction of the picking process. Third, in theory, the WMS in conjunction with the slotting plan could replicate the order pickers experience and sequence them in the same way, but that would require additional logic and likely more system maintenance.
In fact, Banker says the grocer finds an additional advantage of this approach is that it reduces the need for product slotting changes, which come at a cost.
“While most full case picking operations would not want their pickers to be concerned with managing a pick strategy that optimizes pallet build, for the few that would benefit, this “look ahead” approach has its advantages,” says Cliff Holste, SCDigest’s Materials Handling Editor.
“Even without this feature the hands-free benefit of wearable RF units is worth considering,” he adds. “A Voice directed picking solution often requires significant development time and cost. With the wearable RF computing alternative, the initial investment is often not as great. The implementation process is simpler and it usually means little or no changes to your existing software applications.”
What is your opinion of the “look ahead” approach taken by this grocer? Do you want operators or the system to build pallets? What are the trade-off considerations here? Let us know your thoughts at the Feedback button below.
|
|