Financial Versus Operational Accuracy
One thing is clear – the financial organization has a need to ensure the financial accuracy of inventory on the balance sheet. Addressing that issue, however, may not be enough to really drive operational improvement.
Dr. Jim Tompkins, president of Tompkins Associates, agrees that there are many different approaches to inventory accuracy calculation – which are often necessary.
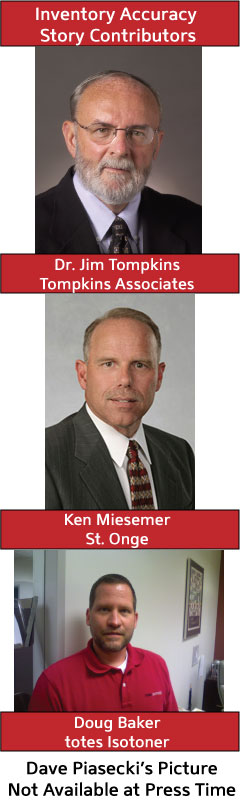
“I am not surprised that companies are unclear on this metric. It depends upon who is asking and on the context,” Tompkins told SCDigest.
He says that for the purposes of Tompkins’ supply chain benchmarking consortium, the following definition of accuracy is used: Correct cycle counts (determined by a match of product, quantity and location to the inventory system) as a percentage of total annual cycle counts. (Counts should be measured by the number of storage slots counted.)
From a financial perspective, Tompkins says what is most often used is the following formula:
- (Reported/counted Value inventory-System inventory Value)/Expected inventory value.
From an operational perspective, the following:
- Total inventory UOM Variation/Total Expected Inventory (System reported).
Also from an operational perspective, a SKU-Level Inventory Management is often used:
- Inventory Variation by SKU/Total Expected Inventory by SKU (System reported).
From a Location Management perspective, Tompkins says the below is often used:
- Number of locations with variances/Total locations (should be split by location type – pick, reserve, etc.). He adds that this should be done through cycle counting as well – and often includes “tolerances” that allow some small amount of error to still be considered as “accurate.”
Dave Piasecki of Inventory Operations Consulting, who has written a book on inventory accuracy, says that it is with good reason that there are a number of accuracy measures in use – but that companies make a mistake focusing on just one of them.
“Every accuracy measurement is flawed in that it can’t by itself show a true picture of your accuracy,” he told SCDigest. “So for those in charge of making decisions related to accuracy, I suggest they regularly review several accuracy measurements.”
He adds that for executives or others that require a single measure, a composite score (using a weighted average) of these different measurements can be created. The composite score can be used to track overall improvement (or lack of improvement) at a high level, “but isn’t very useful in narrowing down the nature of the problems or their impact on the operation,” Piasecki added.
Ken Miesemer, a consultant at St. Onge and former Director of Distribution and International Logistics at Hershey Foods, as well as past president of the Warehouse Education & Research Council (WERC), agrees that while you have to keep the financial group and auditors happy, the inventory accuracy numbers they require aren’t generally enough to find DC problems and drive continuous operational improvement.
“In general, I recommend cycle counts by location, or geographic counts, an aisle or two at a time,” Miesemer says. “Every SKU/Location should be of equal importance– and every error viewed as having the same weight since it points to a process error, rather than APICS old velocity/value definition.”
“Aggregate case count or dollar value-based measures will inflate the numbers,” Miesemer says. “Location-specific accuracy will have a lower grade, but points to the process error, which is my preference.
Miesemer says that this highlights the difference between the accuracy needed for financial reporting and the needs of operations.
“If you have a hundred locations each with a hundred cases, and you are off one case at each location, from a financial perspective, you have an accuracy of 99%,” Miesemer says. “From an operational perspective, at a location level, you would have an inventory accuracy of 0%.”
That may seem like a harsh way to measure it, Miesemer acknowledges, but he says that too often DC and logistics managers develop accuracy metrics “that will make themselves look good.”
He says that, in reality, each error is the symptom of a process flaw somewhere, and that by taking this strict approach to accuracy, it will usually force managers to identify what in the process or people is going wrong to cause even small absolute level errors.
Miesemer adds, however, that “it is understandable that companies measure inventory accuracy differently since their needs and environment might dictate different controls. What is critical is that whatever calculations are used must be standard within a company and across all their DCs to make the measure valuable.”
He notes, for example, one of the many challenges in having any sort of overall industry standard measures that could work across industries. For example, in the food and other industries with “date coded” product - having the date code in the system right as well as the location and quantity should generally be included in the calculation. That’s a variable companies in other sectors don’t need to worry about.
Still, in the end, most companies today rely primarily on absolute errors (plus and minus) divided by the value of the inventory that was counted over a period.
That’s how consumer goods company totes Isotoner does it, according to VP of Operations Doug Baker.
“Formally, we audit twice per year based on absolute dollar variance divided by total dollar of sample size and expressed as a percentage,” Baker says, elaborating that the company’s financial group tells them each time how many locations to count.
“Informally, through the cycle count process, we are watching absolute and net dollar variance, as well as unit variances resulting from the cycle count process. These numbers are available daily,” Baker said.
Another logistics manager from the food industry, who asked not to be named, said his company cycle counts .75% to as much as 1% of locations each day.
“We have about 150,000 pallet positions and, on average, we count about 1000 positions per day,” he said. “The number comes from the finance group, and varies up and down depending on our level of accuracy,” he added, saying that the company's DCs have about 10 full-time cycle counters.
“Accuracy is critically important to DC operations,” St. Onge’s Miesemer says. “I had experience at one company that was running only about 95-96% accurate, and it really had an impact on our line fill rates.”
How do you calculate inventory accuracy? What are the keys to getting it right? Do companies need multiple measures? Let us know your thoughts at the Feedback button below.
SCDigest is Twittering!
Follow us now at https://twitter.com/scdigest |