SCDigest Editorial Staff
SCDigest Says: |
In reality, the terms cross dock and flow through are often used somewhat interchangeably, and in some cases both processes as formally defined are used in the same facility. 
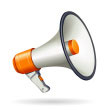
Click Here to See Reader Feedback |
Picking costs and “product touches” are the largest drivers of distribution costs for most companies. So naturally, companies would like to minimize requirements in both areas if they can.
With that in mind, SCDigest thought it would be good to review the various models for low-touch/low-picking activity distribution processes.
Distribution Cross Dock: Product that is received in one door is taken directly to staging/outbound doors without re-packing or value-added services. This approach generally requires an advanced shipping notice and a pre-allocation of the incoming goods to specific customers or retail stores. Warehouse club retailer Costco, for example, is said to cross dock 75% or more of its inbound receipts, a task made easier because it mostly handles and cross docks full pallet loads from suppliers.
Manufacturing Cross Docking: Product is taken directly to staging/shipping from production lines. This can be true for internal shipments (plants to a company’s own DCs) or to a customer. This obviously requires that product allocation to DCs/customers be known at the time of production. Typically, a pallet of goods receives a serialized bar code, and when identifier is scanned into the Warehouse Management or other system, it directs where to take that pallet. SABMiller, for example, even has rail lines running right into some of its plant DCs, and takes palletized cases of beer straight from the production line into rail cars in some cases.
Flow Through: Similar to distribution cross dock, except that it implies some level of repacking or value-added services are involved between receipt and shipping. So, for example, full pallets are brought in, and operators break those pallets down and rebuild mixed-SKU pallets for outbound shipping. In retail, price ticketing or other services may need to be executed.
In Europe, there is a unique practice of flow through not found in the US. Some large retailers, such as Tesco and Carrefour, include in their networks focused distribution facilities that start each day empty or nearly so. At the start of the day, pallets are placed on the floor, and as incoming goods are received, operators drive to the different pallets on the ground, and put cases on the appropriate floor pallets until their pallets are depleted. After all receipts are processed, the pallets are loaded for store delivery and, at the end of the day, the DC is empty again.
In reality, the terms cross dock and flow through are often used somewhat interchangeably and, in some cases, both processes as formally defined are used in the same facility. For example, a retailer might directly cross dock a given percent of receipts, and do re-packing/services on another portion (flow through). In neither case is the received product put away into storage for later picking, though, of course, many/most DCs also use traditional putaway and order picking in addition to cross dock/flow through in those operations.
(Distribution and Materials Handling Article - Continued Below)
|