SCDigest Editorial Staff
Automatic, high speed sortation systems are one of the most common approaches to automating distribution centers, especially those with heavy case pick volumes.
But for many companies, the cost of this level of automation can exceed either the capital they have to spend, or would not lead to a good ROI, as volumes aren’t enough to justify full automation.
SCDigest Says: |
Holste says this kind of system can be implemented for as little as $250,000 - $350,000, a level a much greater number of distribution operations can afford.
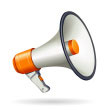
Click Here to See Reader Feedback |
“You need at least 10,000 cases per shift to consider a fully automated sortation system,” says SCDigest Materials Handling Editor Cliff Holste.
Those systems typically involve some level of “pick to belt” case pick operations and mechanized “split case picking” as appropriate. Picked cartons move via conveyor to any one of various types of high speed sorters, which divert the cartons down lanes for shipping based on customer order and/or carrier.
Options for Smaller Operations
“Smaller operations, however, should not abandon the possibility of reducing labor costs by adding mechanization,” Holste says. He believes that “a scaled down, but still effective use of automation can serve many of these companies very well,” an approach he has seen work first hand at several companies over his career.
The approach uses a manual sorting system utilizing a simple re-circulating conveyor loop connected via conveyors to picking areas (as illustrated below).
Manual Mechanized Sortation System
In this approach, order pickers use batch picking techniques, which are at the heart of the labor savings delivered by traditional sortation systems. As a wave or batch of orders is released to the floor, picks per location are consolidated, meaning a picker visits that location just once, and picks cartons across orders for that wave.
(Distribution and Materials Handling Article - Continued Below)
|