Ergonomics and Waste
At the core of Lean thinking is the removal of waste. Taiichi Ohno, Toyota’s chief of production in the post WW II period and father of the Toyota Production System, identified seven potential areas as waste:
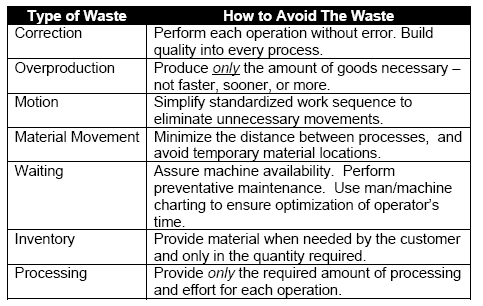
The report states that “Ergonomics plays a significant role in achieving the goals of lean thinking by reducing costs and improving productivity through eliminating waste (e.g., unnecessary motions) and reducing mistakes (improving quality). By limiting the number of repetitions and excess motion, a company will save time and money. Ergonomics plays into lean as much as lean plays into ergonomics, a effective tool that links the two is material handling assist devices, more specifically; ergonomic assist devices (e.g., carts, lift tables, tool balancers, etc).”
The report shows several examples of how a focus on ergonomics and supporting material handling equipment can further the goals of Lean improvement.
For example, the West Virginia National Guard has a repair center for Black Hawk Helicopters. The facility has replaced traditional storage racks with a new vertical carousel system for repair parts. The move led to improvements in safety and security, time savings, space savings and worker ergonomics.
The reports also says that incorporating work station cranes in manufacturing centers can significantly increase flexibility and reduce cycle times.
One company the researchers visited was looking for a way to load and unload virtually any type of parts to any location within a work cell went with a crane-based approach.
As a result, “any combination of machines placed in work cells can be serviced by the crane. Additionally the crane can provide versatile assistance for maintenance and tool/die changes. Parts can be quickly and easily be strategically delivered to the worker’s power zone or strategically to or from any machine. Manually lifting is essentially eliminated. A single worker can essentially perform all tasks within the cell with the assistance of this type of crane. Various end-effectors could be mounted on the crane to accomplished specialized tasks. Cells of almost any size can be designed.”
Impact of Fatigue
The report also argues that not enough companies well evaluate the impact of fatigue on operator and facility productivity.
“The goal of contemporary work design seeks to optimize the mutual strengths of humans and machines. Proper use of ergonomic assist devices can eliminate or reduce fatigue-related risk factors and thus allow the worker to stay both physically and mentally capable throughout the work shift,” the authors state.
The report notes, for example, that a key principle in reducing fatigue is reduction or elimination of “static work,” which is a muscle contraction without motion, such as lifting a box and holding it in position, or holding and supporting a part in one hand while performing an assembly with the other hand.
Often static work can be eliminated by utilizing a stabilizing or holding device, such as a vice, fixture, manipulator, or an adjustable height work surface (such as a lift). Not only do such devices support the part or load, but they free up a second hand or both hands for value-added work, all while reducing fatigue.
The report concludes that “Lean thinking, when implemented correctly, requires effective ergonomics. Effective ergonomics is a necessary part of any sustainable organization. Neither concept is really new, but the trend in most (if not all) industries has made the appropriate application of these ways of operating all the more vital to both short term and long term success.”
The bottom line: Interesting thoughts, but we also need to intersect Lean, ergonomics and material handling with corporate hurdle rates for investment.
Do you believe ergonomic factors, and hence material handling investment, should play a greater role in Lean thinking and process design? Do we need new ways to really calculate the economic benefit of ergonomic improvements? Let us know your thoughts at the Feedback button below.
|