March
9, 2004 |
 |
 |
 |
 |
 |
  |
 |
 |
|
|
 |
 |
 |
 |
SupplyChainDigest’s
Quality Web Seminars
The "No
Spin Zone" -
only from SCDigest!
Did
You Miss the Live Events?
Download
Your "Pay-Per-View" Archived Recording Today!
|
 |
 |
|
 |
|
 |
Nearby,
we carry an article on Harley-Davidson's effective
use of a supplier portal, and ask why more companies
haven't taken similar steps. Please take a moment
to answer these two brief questions.
You
may also add your comments by clicking
here.
|
 |
 |
|
|
|
 |
 |
  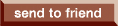 |
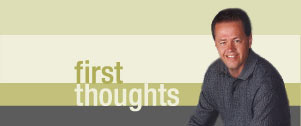 |
 |
|
Dan Gilmore
Editor-in-Chief |
 |
 |
 |
With
thousands of our corporate and technology vendor readers
toiling away to create solutions for RFID compliance
for Wal-Mart, Target, and soon others, for many of us
there's a strong sense of "we've seen this all before."
The
early 1990s produced a similar wave of logistics "compliance"
requirements for bar code labeling and EDI (advance
ship notices), largely under the umbrella of the "Quick
Response" retail-consumer goods initiative.
The
parallels to today's RFID activity are remarkable. Here
are a few:
|
Then,
as now, large retailers led the charge by requiring
unique identification of pallets and (sometimes)
cases, then with UCC-128 serialized bar code labels.
RFID is needed now, as we've noted here before,
because it's apparently just too hard to scan.
|
|
Operationally,
the challenge was moderate for full pallet labeling,
somewhat greater if you were already picking at
the full case level, and monumental if you were
picking in full pallets, but had to label at the
individual carton level. This generally occurred
for suppliers to "flow through" retail operations,
where orders to a retail DC were aggregated to full
pallet quantities, but suppliers had to place a
"Mark for" label on each case for a specific store.
|
|
There
were significant and related IT challenges. Then,
it involved the tremendous effort to support EDI
transactions, as well as map data to a variety of
retailer-specific label formats. While the "standards"
for UCC-128 labels and VICS EDI formats provided
a structure, each retailer's specific implementation
of the standard was different. We could see something
of the same thing now. EPC provides the basic tag
standard, but specific use of the tag bandwidth,
related EDI requirements, and the level of bar code
"co-existence" could create a similar scenario of
multiple formats and compliance requirements for
vendors. Fortunately, RFID can largely piggyback
off of the EDI investments - the real IT challenge
will be around enabling core operation systems,
and managing all that data. |
|
The goals of Quick
Response included significantly reducing the retailer's
time to receive shipments, enabling flow through
processes, increasing visibility to in-transit goods,
and, of course, reducing pipeline inventories and
reducing retail stock-outs. Sound familiar? |
The
current RFID wave really has to be seen as part of this
continuum that started with Efficient Consumer Response
(ECR), then moved to Quick Response, then CPFR, and
now RFID, each with the goal of improving the flow of
information and goods. In each case, there has been
the active hand of the Uniform Code Council (albeit
a little late to the game with RFID, taking on the Auto
ID Center's role), and a substantial amount of investment
for both suppliers to comply, and retailers (and consumer
goods companies themselves) to take advantage of the
new technology. The previous efforts (ECR, Quick Response,
etc.) have all led to important gains - but from my
view, not nearly to the level the initial promotion
of the initiatives promised.
There
are a variety of lessons learned in these first compliance
go-rounds, and we'll cover them in out next issue. But
for those for whom this looks like a revolution - maybe
so, but it sure seems a lot like what we saw in 1992.
Is
"RFID compliance" similar to these earlier bar coding
and EDI requirements? Is RFID what is finally needed
to reach the promise of ECR, Quick Response, etc.?
Let
us know your thoughts.
|
 |
|
|
|
 |
|
 |
This
Week:
Dustin
Hoffman Had it Wrong - "the Future is Logistics"
Harley-Davidson's
Supplier Portal Drives Efficiencies
Bear
Sterns Shipper Survey Finds TL Capacity Tight,
Little Change in Inventory Levels
Summary
and comment below.
|
|
|
|
Supply
Chain Investment News
It was a mixed week for Logistics software,
3PL and transportation stocks, with the most
noticeable moves from Vastera (up 6.5%), Prologis
(up 5.7%), and Symbol (down 8.93%).
|
|
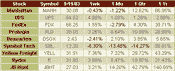
|
|
Click
here to see performance over the past week, month,
quarter and year >> |
|
|
|
It was a relatively flat week for Supply
Chain stocks as the majority of the stocks in
our index moved up or down less than 3%,
the exceptions being Manugistics (down
4%) and Peoplesoft (down 5.9%), while Logility
soared 13%.
|
|
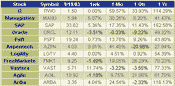 |
|
Click
here to see performance over the past week, month,
quarter and year >> |
|
|
 |
|
 |
While
in the spirit of retail compliance, the UCC-128
serial shipping container format includes a serialized
tracking number that is how many digits long?
Answer below
|
|
|
 |
|
 |
Reader
feedback from the topics in SupplyChainDigest
is growing every week! Keep the comments coming!
If you would like to keep your identity or company
anonymous, please let us know in your response.
We
had a large amount of reader feedback last week
on our First Thoughts column on event management,
including our Feedback of the Week from Ken Smith
of Celestica. We have more letters on this topic
and others, including one reader who thinks Albertson's
best investment would be to fund union organizing
efforts at Wal-Mart instead of more spending on
technology.
For
more complete comments from readers, click
here.
Keep the dialog going!
Give us your thoughts on this week’s logistics
topics at feedback@scdigest.com.
|
 |
 |
|
|
|
|
|
 |
A
nice article in the Wall St. Journal notes that among
the good jobs that are being created by globalization
and the offshore manufacturing trend, are in supply
chain management and logistics to manage all this international
complexity.
The
article states that "the frenetic pace of global trade,
coupled with outsourcing of manufacturing around the
world, has transformed delivery into a complex engineering
task. Companies enlist logistics consultants to untangle
supply chains and to monitor shipping lanes and weather
patterns. In one small indicator of how intricate the
task has become, the Massachusetts Institute of Technology
has expanded its logistics program and started a new
master's degree dedicated to logistics in the school
of engineering."
In
addition to the obvious need to manage complex global
deliveries, the article also notes that globalization
combined with more demanding customers and just-in-time
requirements means more planning and skills are needed
to build agile supply chain capabilities.
The
Key Takeaways: All told, supply chain management and
logistics look like pretty good career choices. Both
fields should continue to get board-level focus and
attention. But I also wonder whether global logistics
requirements for U.S. companies will increasingly be
themselves outsourced to 3PLs/4PLs, to the levels seen
in Europe, driven in part by the complexities even of
cross border movements in the E.U.
No
link to the story is available, but let us know if you
would like a copy emailed to you.
Do
you think logistics will be a good area for job growth?
Is the offshore movement increasing the profile of corporate
logistics? Or will this complexity drive much greater
use of outsourced logistics? Let us know your thoughts.
|
  |
 |
 |
Harley-Davidson
is wrapping up a two-year project to integrate its material
suppliers, using the web to provide a new level of visibility
and transaction management.
The
capabilities and goals are similar to supplier portal
efforts:
|
Eliminate
EDI charges for large suppliers and provide on-line
transactions to smaller non-EDI capable suppliers.
|
|
Provide automated
replenishment notifications to suppliers based on
current inventory levels and planned production.
In the just-in-time world of the automotive-related
industry, suppliers then have 48 hours before the
Harley truck stops to pick up the parts. |
|
Suppliers
can receive on-line performance metrics relative
to quality, on-time delivery, order fill rates,
etc. |
|
Visibility and
a common set of data for use by Harley buyers and
the suppliers. |
Currently,
300 of Harley's nearly 700 suppliers are using the portal,
with the rest expected to come on line over the next
year.
Though
there are no specific metrics associated with the supplier
portal, the benefits seem obvious, and Harley is clearly
doing something right with its supply chain. Operating
expense as a percentage of sales continues to fall,
driving up margins.
Key
Takeaway: The benefits of these web-based supplier portals
seem so obvious, I don't understand why more companies
don't use them. Many vendors have very packaged capabilities
to facility web-based supplier integration. I suspect
the real barrier is that many companies don't have their
own back-end systems ready to expose over the web.
Why
don't more companies use web portals to integrate suppliers?
Is the ROI not there, or are there other technical,
cultural and process barriers? Let us know your thoughts.
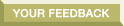 |
  |
 |
 |
View
full article>>
Ed
Wolfe, Phil Alling, and the other good folks at Bear
Stearns survey about 1000 "shippers" each quarter to
research key supply chain and logistics issues. Although
the subsequent report is created to support their investment
perspectives on transportation, logistics and supply
chain technology stocks, the work also always contains
good insight for supply chain professionals.
Highlights
from the just released Q4 2003 survey below. Keep in
mind the survey population is mostly from large companies:
|
Shippers
expect to pay 1.3% of UPS announced 2004 list
price rate increases, and 1.4% of similar increases
from FedEx. These numbers are down slightly from
the Q3 2003 survey, when shippers for example
initially expected to pay 1.8% of the UPS increase.
|
|
A small but significant
amount of shippers (22%) intend to divert some LTL
freight away from the new Yellow-Roadway combination,
primarily due to concerns about potential price
increases, and to achieve greater carrier diversification.
Bear Stearns expects the new Yellow Roadway to lose
about 8-9% of the combined companies' previous revenues.
|
|
While
respondents felt LTL capacity remained plentiful,
there was a growing perception of tightening in
truckload capacities. Those expecting "balanced"
TL capacities in 2004 shrank dramatically from 55%
in the Q3 survey to 17% in Q4. |
|
53% of shippers
did not expect to incur any carrier rate increases
due to new hours of service regulations, while the
47% who expect some rate increases expect them to
average 3.5%. |
|
Respondents expect
inventories to remain relatively flat despite the
economic upswing. 36% of respondents said their
company's inventory levels would be static, while
30% felt inventories would drop by 10% or less due
to increased demand. |
The
report is worth reading for a broad overview of what
large shippers are thinking. Do
you expect freight rates to be impacted by new hours
of service regulations - or is that just a handy excuse
by carriers to raise rates? Are you seeing TL capacity
tightening? Let us know your thoughts.
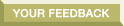
|
  |
 |
|
|
|
|
 |
I have been involved
with developing event management in our company for
four years. I have found that the timing in a
complete supply chain from raw materials to end-user
is critical especially in complex integration industries.
Missing a milestone for one operation quickly
bullwhips downstream driving inventory, labor and equipment
resources resulting in consumer management issues. Considering
that it takes only one weak link in the chain, and there
are millions of events to be tracked, using event management
to filter information is of primary operations control
benefit.
There are three stages to proper event management: measurement,
knowledge creation and management. Many of the
original dot.com entries in this space sold management
and completely under estimated the required precursors
of measurement and knowledge creation. The latest trend
where large application providers are moving to measure
critical events shows how big this task is. Considering
that many application providers have been working in
this space for several years and are only now providing
robust configurable solutions, we can see how difficult
the task is.
Knowledge creation given a robust and accurate data
set is the true value add piece of event management.
Understanding which event is critical from the
millions of tracked events and understanding the implications
driven by the key event has stumped even the best and
brightest in the supply chain control field. Creation
of a cause and effect matrix provides operations with
the levers to accurately and quickly control supply
chain issues.
Management of a supply chain is simplified by the design
team providing easy-to-use and effective levers. Operations
teams need to be able to respond to supply chain issues
quickly. The team on the ground does not have the time
to determine control points and responses. A team
without predefined levers is forced to hunt and peck
for solutions and the result is a supply chain that
quickly spirals out of control.
I agree that we are on the cusp of a new age in supply
chain management. Once disparate suppliers, manufacturers,
designers and customers, are now collaborating and communicating
to build responsive and efficient total fulfillment
solutions. The true winners, the companies that
prove to be the most efficient and hence the most profitable,
will be those that embrace event management for the
total supply chain.
Ken
Smith, M.Sc. P.Eng.
Celestica Inc.
|
  |
 |
 |
Supply Chain
Event Management is not easy. There is no two ways about
it. Think about the variety of information that must
be accumulated in order to perform this task:
Purchasing -
Purchase orders, materials, specifications, delivery
dates
Operations -
Scheduling, MES type information
Quality - Specifications,
conformance to spec, corrective actions
There are very
few systems in the market that bring these together
in a cohesive format that allows a multi-site manufacturer
to have clarity into these activities. There are several
market research reports that quantify the benefits of
a company extending its quality practices with its supplier
organization. Specifically, AMR produced a study in
September, 2002, that quantifies the savings realized
by providing real time access to supplier quality processes.
The report discusses a variety of benefits that a manufacturer
can achieve through an Internet enabled supply chain.
The report described measurable benefits, which include:
Reduced cost
of poor quality (67% reduction)
Improved incoming
inspection yield
Reduced non-conformance
cycle time (30 days to 3)
Reduced backlog
(by 83%)
If a company
can incorporate these activities into their supply chain,
the financial benefits through reduction in disruptions
can be significant.
Dan
Creinin
EMNS,
Inc.
I
agree that adoption of event management solutions has
been surprisingly slow given the potential. Before
we could claim some capability in this space, PeopleSoft
partnered with one of the start-up vendors. I did a
seminar with a large PeopleSoft Supply Chain customer,
along with the vendor, the point of which was to identify
the best opportunities for event management across the
enterprise (about 12 distinct divisions, manufacturing
different products in factories around the world). The
result? The company had a corporate-wide initiative
to improve DSO, and there were points identified along
the information chain (from discounts not taken, to
the analysis of customer behavior through analytics
to identify when paying practices vary or trend negatively)
where event management solutions would fit well. This
was a supply chain group of about 30 with a few finance
folks along.
The project never received commitment, and perhaps this
was at a time, 2 years ago, when IT investment was at
an all time low. Still, here we are two years
later and very few companies have adopted the technology.
If you view event management from a Supply Chain
Planning perspective, it can become the net-change action
messages that drive a business between plan cycles.
From this perspective, though, I think companies
may look at the tool as an expediter that creates, potentially,
volumes of "process failures" to be responded
too, when it may in fact be less-than-real-time transactions
causing the violations. This will be the case
if the use of the tool is not well planned and there
aren't sufficient controls over event management tolerance.
Good article, and thanks for the continuous excellence
of your newsletter.
Joe
Shobe
Peoplesoft
What is interesting
about this topic is that most of the big vendors have
implemented this new architecture at some level. Especially,
the supply chain management vendors have working customer
implemented solutions in this space. Some of these
projects have been huge, like at the DoD, and large
auto, chemical etc. companies.
Yet the standalone
vendor has not flourished!
The challenge
has been for the stand-alone event management vendor.
It always made sense to me that the standalone vendor
would have a play here, since the very nature of event
management is to deal with heterogeneous, non-synchronous
events, across systems and enterprises. Even more
importantly the architecture was designed to reduce
latency. So if you layer this wonderful concept on top
of an ERP, you are still stuck with all the layers of
latency that these big ole systems introduce into your
processes.
If you think
about this from a "big trend" perspective, every ten
years or so, we have a major overhaul of IT. The
realization hit me last year that we have passed the
ten-year mark on ERP.
I think for any
company who cares about real-time or what we call at
ChainLink "Smart-time", you need to think about ways
to out-fox your CIO, who ironically still seems to be
the embracer of this old technology and think about
your true supply chain requirements:
|
Do your customers want
real-time status? |
|
Does your supply chain require trace
and track? (Retail, DoD, Pharma/HealthCare, Compliant
Global Logistics) |
|
Do you take orders
all day long and fulfill to markets and units of
one? |
If you answer
yes to any of these, you need to think about event
management as a major architectural component of your
enterprise
structure since it will allow you to deal with the
real world of asynchronous events.
If you are a
big user of ERP, you can go to them and get this, but
you need to think about how it fits into your supply
chain network, beyond your internal processes.
However, in the
logistics space, to get this capability layered onto
of a web based transportation solution, you need to
consider the best of breed guys. It will be a different
twist on the typical project, embracing trading partners,
but the value is huge!
Ann
Grackin
ChainLink
Research
|
  |
 |
 |
Albertson's
investments in technology are impressive, and I wish
them well in their quest to compete with Wal-Mart.
Clearly Wal-Mart needs real competition.
However
I think Albertson's might get a better ROI from funding
Labor Union efforts at organizing the Wal-Mart workforce.
Until the grocery retailers' labor costs are comparable
to Wal-Mart's there can be no competition. In
our area, Wal-Mart clearly has lower prices by a wide
margin pretty much across the board. Some of this
may come from supply chain efficiency, but much has
to do with the cost of warehouse and store labor.
Consumers
believe this and will shop Wal-Mart because it fits
their budget. Handheld computers with web based
shopping lists will not do a lot to change their minds.
Steve
Murray |
  |
|
|
|
|
 |
Q. |
While in the spirit of retail
compliance, the UCC-128 serial shipping container
format includes a serialized tracking number that
is how many digits long?
|
A. |
In the
20-character long bar code, which includes an
application identifier, packaging indicator, vendor's
UPC number, and check digit, nine characters are
used to provide a unique, serialized tracking
number, or "license plate," for each container.
|
|
  |
 |
|
|
|