I am very keen on the subject of supply chain innovation right now, for a variety of reasons.
First, CEOs across the globe are putting innovation as the top or near top priority for the companies they run. It's pretty simple why: innovation is what drives the growth and attractive margins. Supply chain in turn obviously has a key role to play in overall corporate/product innovation. This is perhaps most manifestly seen right now in the Internet of Things and how industrial companies especially are currently or prospectively leveraging IoT to create new priducts and services.
Gilmore Says: |
The Kiva system true innovation, and has ushered in the "goods to picker" concept that is now so prominent in materials handling circles.
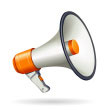
Click Here to See
Reader Feedback
|
So, supply chains need to both supoort product innovation, while also innovating in its own domain. But I would argue that supply chain innovation is not well understood. Certainly we don't have any good ways to measure it.
I have been doing some light collaboration on supply chain innovation with Dr. Jim Rice of MIT, who has also been researching this topic. MIT in fact has something it calls the Forum for Supply Chain Innovation, which is doing research in this area, among other activities.
Hope to have something more to share from the two of us soon on this, but there are a number of issues to be explored, from defining supply chain innovation, to measuring it, to the difference between innovation and continuous improvement and many more.
I am quite excited to be working on these types of questions, which I think will be good for the industry if we can wrestle some of them to the ground.
As some readers may remember, back in 2010 I came up with the top 10 supply chain innovations of all-time. Given my focus on this topic here in 2015, I thought it would be appropriate to repost that list, which I think is a good one. But too add some new value I decided to add two innovations to make it an even dozen.
I will note Rice used my list during his own excellent presentation on supply chain innovation at the MHI annual conference last October.
It was difficult to create this list, because many innovations either have no clear origins or came from a
sort of a combined evolution along a number of fronts. This is
especially true in terms of much supply chain technology innovation.
So then as now, I was looking for:
• Innovation for
which we can identify pretty clearly that some single company or
individual(s) was/were responsible for the breakthrough - though of course everything builds off the past
• The innovation had a deep and lasting impact on supply chain practice
That said, here is the expanded list, in reverse order:
12. The First True Network Optimization System: While there there were a few very primitive single commodity network optimization attempts by various academics that were not of much value, the first true "multi-product" network optimization tool was developed by Dr. Arthur Geoffrion and Dr. Glenn Graves, both of UCLA, in 1972. It was formally reported in the literature in a seminal work that appeared in the Management Science journal in 1974. That article is studied by many OR students even today. The network analyzed was that of Hunt-Wesson Foods. Geoffrion and Graves became two of the five co-founders of Insight, which still does this kind of work today, and really created the network optimization industry.
11. The Kiva Robotic Picking System: The idea for the orange AGV-like robots that bring inventory to order pickers was first conceived in 2003 by CEO Mick Mountz, and with the help of some MIT professors Kiva brought the technology to market less than two-years later. In 2012, Amazon spent an amazing $775 million to acquire Kiva - a small company at the time - which is one measure of the system's value, as Amazon now keeps the technology to itself and eventually into dozens of its fulfillment centers. This was true innovation, and has ushered in the "goods to picker" concept that is now so prominent in materials handling circles.
No. 10: Taylorism: In the late 1800s, the great Frederick Taylor
takes the first scientific approach to manufacturing. In the early
1880s, he invents the concepts of using time studies on the factory
floor, and based on that work, the notion of "standard times" for
getting specific tasks done. Later develops the concept of incentive
systems and piece-rate pay plans. Taylor's ideas were simply seminal -
and often controversial - and dramatically influenced the practice of
manufacturing over the next few decades and even to this very day.
No. 9: 3M's Transportation Load Control Center: In 1982, 3M, like every other company, had to leave transportation decisions to each plant and distribution center. Roy Mayeske,
at that time the Executive Director of 3M Transportation, had the idea
to centralize transportation planning to look for network synergies. 3M
took mainframe software that had been developed for Schneider National - one of its
major carriers - and had it modified it to be workable from a shipper
perspective. Ship sites called in planned shipments, and then carriers and
routings were phoned back. The LCC is now of course a standard logistics practice
today.
No. 8: Distribution Requirements Planning (DRP): In the late 1970s, Andre Martin ran operations for Abbott Labs Canada, and found himself caught between
manufacturing and distribution managers, who could never seem to get
inventory questions right and always blamed each other. Realizing that
what was needed was a sort of Manufacturing Resources Planning for
inventory distribution, Martin led a successful effort to build the
first computerized DRP system, which in turn led to a book that created
the software category of DRP, as several technology firms built products
based on these ideas. Was in many way the start of today's supply chain
planning software industry.
No. 7: The FedEx Tracking System: After re-inventing the category of express parcel shipments, FedEx went
a step further in the mid-1980s with its development of a new
computerized tracking system that provided near real-time information
about package delivery. Outfitting drivers with small handheld computers
for scanning pick-ups and deliveries, a shipment's status was available
end-to-end. The FedEx system really drove the idea that "information
was as important as the package itself," and was foundation of our
current supply chain visibility systems and concepts.
No. 6 - The Universal Product Code:
Though the idea to use some form of printed and even wireless automatic
product identification had been around for decades, lack of standards
had precluded individual ideas from gaining any sort of critical mass.
In 1970, a company called Logicon wrote a standard for something close
to what became known as the Universal Product Code (UPC) to identify via
a bar code a specific SKU, an effort that was finalized a few years
later by George Laurer at IBM. The first implementation of the
UPC was in 1974 at a Marsh's supermarket in Troy, OH north of Dayton.
The invention triggered the auto ID movement, forever changing supply
chain practice and information flow.
No. 5: The Ford Assembly Line: Henry Ford actually got the idea for the assembly line approach from
the flow systems of meat packing operations in the Midwest, but it was
Ford's adoption of the production approach with a continuously moving
line for Model T's in 1913 that revolutionized not only automobile
assembly but took the practice of manufacturing to new levels in other
sectors as well. Total time of assembly for a single car using the
production line fell from 12.5 labor hours to 93 labor minutes,
ultimately making cars affordable for the masses, changing not only
supply chain but society.
No. 4: Economic Order Quantity (EOQ): Economic Order Quantity is a mathematical approach for determining the
financially optimal amount of product to order from suppliers based on
inventory holding costs and ordering costs. The original concept is
generally credited to Ford Whitman Harris, a Westinghouse engineer, from an article in 1913, but it was a much later article in the Harvard Business Review in 1934 by RH Wilson that made EOQ mainstream. The formulas are still taught today, and the
basis for much supply chain decision-making even in this era.
No. 3: The Ocean Shipping Container: It is hard to imagine today, but until the mid-1950s, there was no
standard way to ship products on ocean carriers, and most were shipped
on whatever container or platform the producing company deemed best. The
result was terribly inefficient handling on both sides of the equation,
poor space utilization on the cargo ships, freight damage, and high logistics costs.
Enter Malcom McLean, legendary logistics entrepreneur
and visionary who invented the standard steel shipping container first
implemented in 1956 at the port of New Jersey. Someone would have
thought of it eventually, but McLean's invention started the explosion
in global trade.
No. 2: P&G's Continuous Replenishment: Until 1987 or so, order patterns in the consumer goods supply chain
were almost totally dependent on whatever the manufacturer's sales person
and retail buyer decided between them. That's until Procter & Gamble
bought a mainframe application from IBM for "continuous replenishment"
(which had been deployed a handful of times in other markets), re-wrote
it for consumer goods to retail, and as a result dramatically changed
that entire value chain by driving orders based on DC withdrawals and
sales data.
P&G first implemented the approach with Schnuck's Markets in St.
Louis, with dramatic results in both lowering inventories while
increasing in-stock at retail. KMart was next, taking pipeline diaper
inventories from two months to two weeks - but KMart never completely
embraced the possibilities. A legendary 1988 meeting between P&G's
CEO and Sam Walton led to a CR program there and
changed supply chain history, helping propel Wal-Mart to retail
dominance and providing the foundation for Efficient Consumer Response
(ECR), Category Management, Continuous Planning, Forecasting and
Replenishment (CPFR), and more.
And finally.... (drum roll and envelop please):
No. 1: The Toyota Production System: When James Womack and several co-authors wrote "The Machine that Changed the World" in
1990, it was of course not a Toyota car that had such an impact, but
rather the Toyota Production System (TPS) that was the foundation of the
company's dramatic success across the globe. Pioneered by Toyota's Taiichi Ohno and a few colleagues, TPS not only is the foundation for today's Lean
manufacturing and supply chain practices, but the concepts have
penetrated versus every area business. TPS truly did change the world.
Hope you enjoyed this. Updated video version soon. Would love to hear your list or suggested additions.
Please send us your reaction or improvements to our list of the top supply chain innovations at the Feedback button or section below.
|